Since early 2003, the number of repairs-per-thousand at three-months-in-service for Ford’s huge F-series Super Duty pickup trucks sold mainly in North America has improved 55% and the number of things-gone-wrong has improved 19%, according to Ford’s internal data.
Pete Reyes, 2008 Super Duty chief engineer, said one of the quality strategies to help continue that trend was to focus on customer wants.
“Features such as brakes, chassis and steering already are highly competitive – probably best in class – with the current model, so the team concentrated on improving the interior and adding more features,” said Reyes. “Those actions should help boost quality because of the appeal effect.”
Added attention also was given to the new 6.4-liter ‘Power Stroke’ diesel engine, traditionally chosen by 75% of buyers.
The engine was put through the equivalent of more than 10m miles of dynamometer and vehicle testing. A fleet of trucks with the current six-litre diesel engine were instrumented to collect real-world data to give engineers an even better understanding of how customers used their trucks.
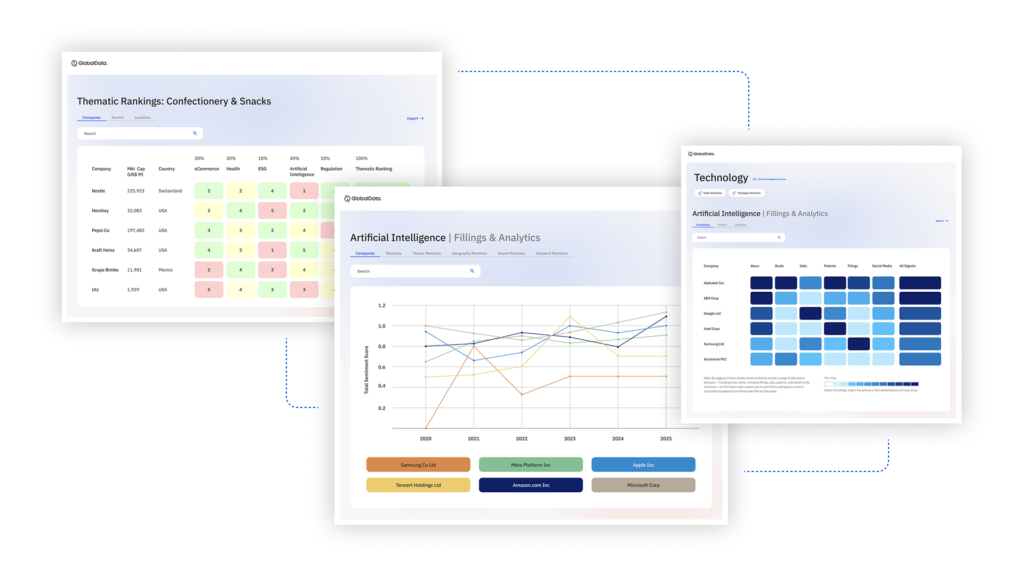
US Tariffs are shifting - will you react or anticipate?
Don’t let policy changes catch you off guard. Stay proactive with real-time data and expert analysis.
By GlobalDataThe information was used to develop additional tests for the new diesel engine to help improve its durability and performance.
“The process we followed gives us high confidence that the new diesel engine will be very reliable, quiet and provide exceptional capability and performance in a balanced package,” said Dan Davidson, Ford powertrain engineering supervisor.
Reyes said that involving technical specialists from Ford, Navistar and Ford of Europe also benefited the new engine, as did using employees from Ford supplier quality assurance to oversee and assist with critical systems.
“We were involved as far down as Tier 3 and Tier 4 suppliers, in some cases. Fuel rails, for example, were one of the critical systems. It’s a high-speed line and a complicated rail, so we took extraordinary measures very early to ensure a quality process,” Reyes said.
Another key was deployment of 8tools early in the development of the work-oriented truck line. In certain situations where outside firms were identified as having more advanced technology, the automaker outsourced the job to ensure even better analysis.
Prototypes logged 10m miles of testing in all types of conditions, including nearly 3m miles of real-world customer durability testing in some of the most extreme conditions possible.
By the time the Super Duty began the normal launch phase at Ford’s Kentucky truck plant, Reyes says the programme was far enough ahead of schedule that the team fine-tuned certain production processes. Items such as fender, door and glass fits, cab quietness and sheet metal finish received closer scrutiny.
“Anything you can do to improve wind noise, fit and finish and craftsmanship results in a better experience for the customer,” said Reyes.