The manufacturing productivity gap among North American automotive manufacturers continued to narrow as quality advances and more flexible labour agreements drove major improvements, according to an annual study of the auto industry released on Thursday by Harbour Consulting.
The larger gap in financial performances of the Detroit-based and Japan-based automakers reflect domestic companies’ higher incentive costs, legacy costs and their slower response to shifts in consumer choices more than any large competitive disadvantage on their factory floors, according to the report.
“Improving productivity in the face of lower production is a huge accomplishment, but none of the domestic manufacturers can afford to let up,” said Harbour Consulting president Ron Harbour.
“General Motors essentially caught Toyota in vehicle assembly productivity. Considering that they will be building vehicles in 2007 with dramatically fewer hourly employees in the US, GM, Ford and Chrysler likely will reduce their hours per vehicle significantly.”
The UAW and CAW were more proactive in 2006 than ever before in creating a more competitive environment among the companies whose hourly workers they represent. Chrysler, General Motors and, especially Ford, negotiated more flexible local labour agreements prior to this summer’s pivotal national talks with the UAW. However, they must go further to overcome their persistent health care and pension cost disadvantage compared with Honda, Nissan and Toyota, the report said, adding that restrictive labour agreements that create cost disadvantages still exist and could jeopardise the survival of certain automakers.
How well do you really know your competitors?
Access the most comprehensive Company Profiles on the market, powered by GlobalData. Save hours of research. Gain competitive edge.
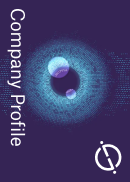
Thank you!
Your download email will arrive shortly
Not ready to buy yet? Download a free sample
We are confident about the unique quality of our Company Profiles. However, we want you to make the most beneficial decision for your business, so we offer a free sample that you can download by submitting the below form
By GlobalDataThe difference between the most and least productive in terms of total (assembly, stamping and powertrain) labour hours was 5.17 hours per vehicle (or about $US300 per vehicle), down from 7.33 hours per vehicle in 2005, and less than one-third the 17.17 HPV gap in 1998.
This year, Honda’s showed the biggest improvement (2.7%) across this combined assembly, stamping and powertrain measure.
In overall productivity, four of the six companies with assembly, stamping and powertrain operations in North America – GM, Honda, Chrysler and Ford – showed improvement in 2006.
Nissan Motor did not participate in this year’s report. Toyota’s total manufacturing hours per vehicle, while leading the way among the participating companies at 29.93 HPV, was not as strong as its 2005 performance of 29.40. Honda was second at 31.63 HPV.
Among vehicle assembly plants, GM’s Oshawa #2 plant, which assembles the Pontiac Grand Prix, Buick LaCrosse and Buick Allure, set the individual plant benchmark for labour productivity with a measure of 15.68 hours per vehicle, followed closely by its adjoining Oshawa #1 plant that produces the Chevrolet Impala and Monte Carlo, Oshawa #1 posted a 16.34 HPV performance.
“GM Oshawa historically has had one of the best work forces of any assembly plant in the industry and the data proves that,” Harbour said. “The total site builds 20% of GM’s North American volume and does it well.”
DaimlerChrysler, Ford and General Motors still have a wider variation in capacity utilisation among their assembly plants, while they continue to work on plant flexibility. By closing plants in the next two years, all three domestics should see improvement on capacity utilization. Others, such as Toyota, which had its assembly plants running between 95% and 108% of capacity, are leveraging their design, engineering and manufacturing organisations to increase flexibility and use common parts and processes.
The other differentiator is profitability. Toyota and Honda each earned a pre-tax margin of more than $1,200 on every vehicle they sold in North America. In contrast, Chrysler Group lost $1,072, while General Motors lost $1,436 and Ford lost $5,234 on each vehicle sold in 2006.
This reflects a variety of factors, including the large difference in health care and pension costs, lower average revenue, as well as higher costs of rebates and low-interest rate financing required to trim inventories.
Honda led all multi-plant companies in assembly performance with 21.13 hours per vehicle, but CAMI Automotive, which produces the Chevrolet Equinox, Pontiac Torrent and Suzuki XL-7 in Ingersoll, Ontario, achieved a 17.85 HPV and the New United Motors Manufacturing Inc. (NUMMI) plant in Fremont, California, posted an impressive 19.34 HPV.
General Motors had four of the 10 most productive assembly plants: Oshawa #2 (15.68 HPV for Pontiac Grand Prix, Buick LaCrosse and Allure); Oshawa #1 (16.34 HPV for Chevrolet Impala and Monte Carlo); Fairfax, Kan, (17.89 HPV for Chevrolet Malibu and Saturn Aura); and Lordstown, Ohio (19.17 HPV for Chevrolet Cobalt, Pontiac G5 and Pursuit).
Toyota’s Georgetown #2 plant, which produces the Camry and Solara, ranked 10th with 19.77 HPV, an impressive feat considering that it launched the new Camry and the Camry Hybrid during 2006. Overall, Toyota’s assembly performance declined 3.3% from 2005. Despite a 13% increase in North American sales Toyota’s North American production volume actually declined 4% at the five assembly plants participating in the report.