Chrysler this week started production of the 2007 Aspen SUV – essentially a high-end version of the Dodge Durango – at its Newark Assembly Plant in Newark, Delaware, following a $US180m retooling and body shop renovation that allows the facility to build two models on one assembly line.
The plant’s second model is the Durango, last redesigned for the 2004 model year.
“Newark Assembly Plant is joining our growing list of flexible manufacturing plants, and by the end of this year, five of our six US truck and activity vehicle assembly plants will produce more than one model,” said Byron Green, Chrysler’s head of truck and activity vehicle manufacturing.
Chrysler Group’s Flexible Manufacturing Strategy (FMS) allows the automaker to produce a higher quality product, faster, for lower cost and is key enabler to the company’s plan to launch 10 new vehicles in 2006, the most in its history.
In order to balance production with demand, the FMS approach allows the company to efficiently build lower-volume vehicles that take advantage of market niche, and to quickly shift production volumes to different models within a single plant or between multiple plants. Manufacturing flexibility gives the company the ability to better respond to consumer demand for its growing vehicle range. Newark can vary the production mix between the two vehicles as needed.
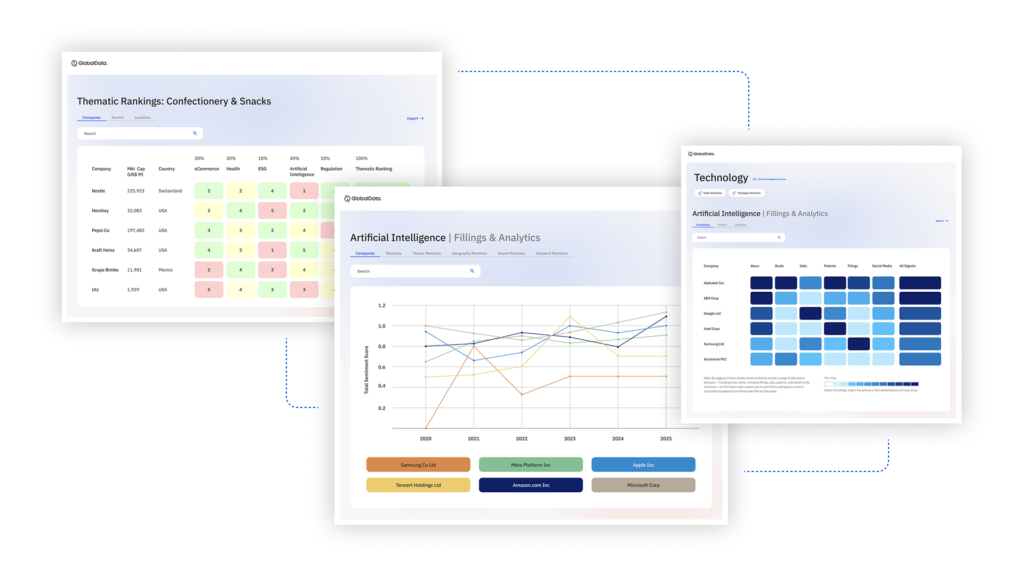
US Tariffs are shifting - will you react or anticipate?
Don’t let policy changes catch you off guard. Stay proactive with real-time data and expert analysis.
By GlobalDataFMS is being implemented product by product and plant by plant across the group.
The rolling launch of the Aspen was completed in 24 months. Ahead of the launch, 2,100 employees were trained to operate new robotic equipment and perform advanced manufacturing processes, resulting in new methods of error-proofing and a new level of manufacturing efficiency.
The Newark plant has also adopted so-called ‘smart’ manufacturing which empowers assembly line workers and fosters creativity on the shop floor, according to Chrysler. Smart processes include work teams, self-designed workstations, and a framework for flexible job classifications all designed to further improve plant flexibility and efficiency.
Chrysler Group is Newark’s largest employer and has over 2,100 workers in Delaware.