After spending over $US500m recently to improve manufacturing flexibility at its Windsor assembly plant in Ontario, Canada, Chrysler on Tuesday celebrated the manufacturing launch of its redesigned 2008 Chrysler and Dodge minivan lines.
The Canadian plant will gain additional volume frm this year as it will build the right-hand-drive, diesel and other export versions of the new minivans. Previous models were assembled under contract by Magna Steyr in Graz, Austria.
Chrysler pioneered the minivan in North America (Renault’s Espace arguably took the same honour here in Europe) about 24 years ago and has since built nearly 12m. The segment subsequently expanded greatly as rival Detroit automakers, followed by the Japanese and Koreans, fielded competitors but several automakers have subsequently abandoned the segment as it has fragmented and contracted somewhat with the more recent arrival of SUV-like ‘crossovers’.
Chrysler is claiming an industry first for its latest minivan models – the ‘Swivel ‘n Go’ seating system and a removeable centre console table.
Flexible manufacturing
How well do you really know your competitors?
Access the most comprehensive Company Profiles on the market, powered by GlobalData. Save hours of research. Gain competitive edge.
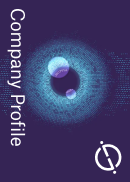
Thank you!
Your download email will arrive shortly
Not ready to buy yet? Download a free sample
We are confident about the unique quality of our Company Profiles. However, we want you to make the most beneficial decision for your business, so we offer a free sample that you can download by submitting the below form
By GlobalDataTom LaSorda, vice chairman and president of so-called ‘The New Chrysler’, newly under private equity ownership, said: “…the home of the minivan has become one of our first plants to implement an enhanced flexible manufacturing strategy and added a smart manufacturing workplace model promoting greater innovation and creativity on the plant floor.”
Under DaimlerChrysler management, the former Chrysler Group allocated $511m in 2005 on manufacturing and paint operations at Windsor to allow the redesigned 2008 Chrysler Town & Country and Dodge Grand Caravan minivans to be built on the same assembly line as Chrysler’s Pacifica crossover.
Chrysler said yesterday a spend of $286m of the total investment would allow the plant to build three different vehicle platforms and pilot a fourth simultaneously on the same production line. The ability to build multiple products on the same line enables the company to build and test prototype vehicles much earlier in the launch phase.
Because production tooling and processes are used (rather than a simulated line which is often used for prototypes), the company can train operators and resolve manufacturing issues much sooner, improving quality.
Frank Ewasyshyn, Chrysler’s manufacturing chief, said: “Our focus on flexible manufacturing and new investments, adding state-of-the art technology to plant operations, will help us ensure we can meet those demands and build almost anything, anywhere, with improving speed and quality.”
Under-body pallet system
The order in which the body is assembled using a unique under-body pallet system in the body shop is key to the flexible manufacturing process. The same flexible pallet system has also been used at the company’s Sterling Heights plant in Michigan where the Chrysler Sebring and Dodge Avenger are made, as well as the Toledo North Assembly Plant in Ohio, where the Jeep Liberty and Dodge Nitro are built. This means that the same production system may be used to build almost any type and size of vehicle.
This flexible manufacturing system was first used in the launch of the redesigned 2001 minivan models in summer 2000.
Windsor assembly ramped up to maximum production of about 25,000 of the fully redesigned model in just 25 days, compared to a 110-day industry average for a major change-over of this type.
Windsor underwent a major change-over with extensive upgrades to accommodate the new minivans’ production requirements and smart manufacturing methods.
The enhanced processes and installation of new technology will also benefit future product launches and additional product variants due to the greater levels of flexibility, Chrysler said.
The body shop’s under-body pallet system, an enabler of flexibility, gave the plant the ability to maintain production of the 2007 model year vehicles concurrent with change-over and pilot production for the new 2008 model year minivans. The system carries on the same line the under-body components for minivans and the Pacifica, eliminating the need for separate lines for each product.
Flexible robotics
New, flexible robotic lines were added to weld the vehicle’s body sides and under-body sub-assemblies, which will accommodate future models and product variants at reduced investment levels. Once assembled, over 350 points on the minivan’s body frame are automatically checked for weld precision and dimensional quality.
In the trim, chassis and final area, new processes were developed to install the new safety features including third-row side curtain airbags, inflatable knee blocker and multi-stage front airbags, among others. Ergonomic assist arms were added to enable smooth and safe installation of second- and third-row seats, as well as cockpit, suspension and front-end modules. The plant’s increased use of modular sub-assemblies supports enhanced model flexibility and smart manufacturing processes.
New paint shop
The remaining $225m of the investment in Windsor went toward developing a new paint facility capable of accommodating the dimensions of at least 11 different body styles. The paint shop was modified to accommodate new robotic applications of two types of sound dampener technology.
Chrysler said the 185,000 square foot paint shop is completely new, and designed to be one of the most flexible, leanest and environmentally-sound paint shops in the company. The shop floor contains the latest energy efficient ovens, booths, fans and 127 robots, controlled by an environmental management system. The level of automation keeps employees out of the hazardous material area.
New features making the new paint shop more energy- efficient and environmentally friendly include a new powder spray booth with innovative temperature controls and re-circulated air supply which demands less energy and improves control. The condensate control tunnel requires less energy, improves quality by reducing defects and solvent emissions to the atmosphere.
Advanced oven design, ‘bottom entry & exit’, eliminates air-seal requirements which saves heat and further reduces the potential of foreign material defects. A new sludge dryer transforms saturated liquid sludge, reducing waste. The dried sludge can potentially be used as a supplemental fuel in future applications.
New base and clear coat spray booths re-circulate the majority of their air, significantly reducing energy consumption and providing greater control over the paint process to improve quality. The colour coat application process is entirely robotic with high voltage electrostatic bell applicators which requires less energy, reduces paint usage and solvent emission, and improves quality at the same time. The rapid repair system eliminates the need to reprocess the entire vehicle, which shortens the process time. A fully robotic foam application system automatically injects sound deadening material into the vehicle by locating 11mm holes using a laser guide vision system.
Finally, a robotic inspection system measures film build, colour, and appearance of five vehicles per hour and returns that information back to the application engineers to maintain quality.
Union cooperation
Working with the Canadian Auto Workers (CAW) union, Windsor Assembly conducted over 345,000 training hours in 2006 and 2007 in order to prepare employees to build the 2008 minivans.
Recent agreements with unionised employees cleared the way for new operating principles and allow for work teams, self-designed work stations, a framework for flexible job classifications and extensive employee training, Chrysler said.
Originally built in 1928, Windsor is the largest of Chrysler’s 14 assembly plants at 4.01m sq ft and was one of the first to implement the flexible manufacturing strategy, in 2003. It employs 4,600 people on three shifts.