
ZF’s UK passenger car axle assembly plant, ZF Lemforder at Solihull, on Tuesday (30 September) marked its 10th anniversary.
The plant near Birmingham, about 15-minutes’ lorry delivery run from the Land Rover assembly plant in Lode Lane, Solihull, has been producing axle corner modules for models such as the Range Rover and Range Rover Sport just-in-time and just-in-sequence since 2004.
The location received a ‘Manufacturing Excellence Award’ in 2010 for its efficient and flexible logistics system.
For the last decade, the plant has delivered products just-in-time and just-in-sequence to the Jaguar Land Rover plants only a few miles away. Between four and hours pass between the customer’s quantity-based call-off and the delivery of the finished product. At full tilt, JLR uses 40-42 vehicle sets an hour at Lode Lane and the ideal ‘buffer’ at ZF is about 185 sets.
Numerous complex protocols are in place to minimise plant downtime – key spare components for key machines are ‘on the shelf’ in known good operating condition, spare machine capacity sits alongside that in use for production ready to be switched into the line should a breakdown occur, and engineering staff are rostered on at weekends (when the plant is idle) to keep production-week maintenance downtime to a minimum.
The ZF plant has a rigorous ‘no fault forward’ approach to quality management resulting in 44 months of zero defects at its customers, an outstanding performance in the just-in-sequence environment.
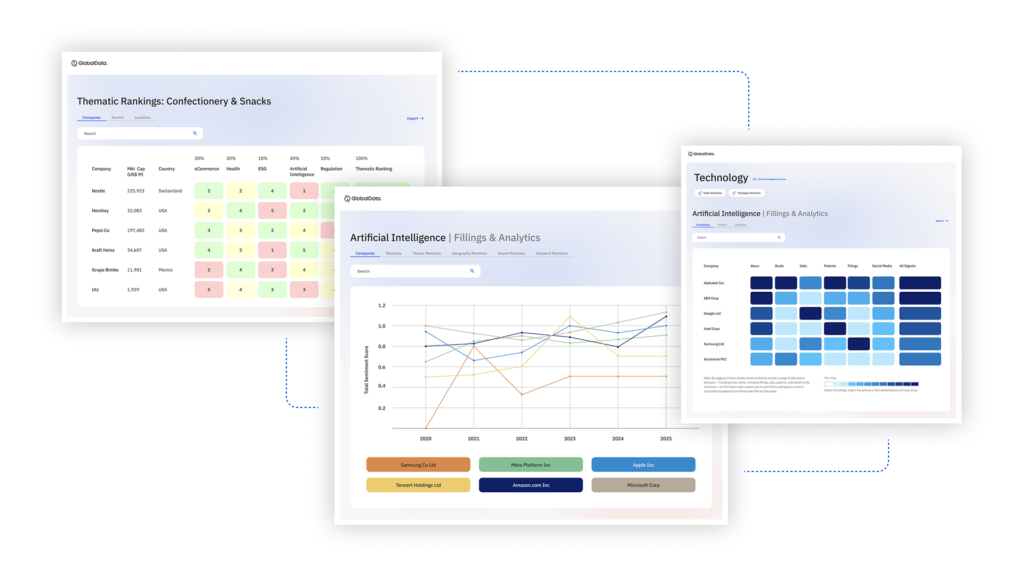
US Tariffs are shifting - will you react or anticipate?
Don’t let policy changes catch you off guard. Stay proactive with real-time data and expert analysis.
By GlobalDataA second assembly line was opened in August 2014. Currently, 113 employees on three shifts, five days a week, produce around 150,000 corner modules a year in the 4,132 sq m factory. The plant started with 43 workers on two shifts in 2004 and will expand output again in 2016 when the Discovery replacement goes into production at Lode Lane.
“The assembly of corner modules and complete front and rear axles for passenger car manufacturers has been one of the important international fields of action for the ZF Group,” said Peter Holdmann, head of ZF’s Chassis Systems business unit in the Car Chassis Technology division.
ZF has another plant in Darlaston, near Walsall on the northwest side of Birmingham, which makes numerous components including some of the parts used for axle assembly in Solihull. It also has two service centres handling aftermarket sales in the UK.
Solihull’s 150,000 corner units a year will contribute to the over 4m axle sets ZF’s Chassis Systems unit will produce this year, up from about 3.75m in 2013. In 2004, when Solihull opened, output was about 1m worldwide. This, ZF UK managing director Terry Somerfield said, reflected the auto industry’s increased outsourcing of axle technology in the last decade.
ZF has other axle assembly plants dedicated, like Solihull, to output for a single automaker. These include Tuscaloosa in the US, supplying Mercedes’ SUV plant there, Duncan supplying BMW in South Carolina, and Chicago for Ford. In Europe, Lebring supplies Mini axles to BMW’s contract assembler Magna Steyr and Rosslyn in South Africa supplies the local BMW factory. There is also a plant in Adelaide, South Australia, which supplies both General Motors’ Holden and Ford.
Solihull produces 68 variants alone of JLR’s front corner modules, each shipped line-sequenced for a particular vehicle. The parts used are a mix of ZF-produced components and those from suppliers JLR has selected so there is a complex logistics operation in place with lorries taking finished vehicle sets across to Lode Lane every 15 minutes or so (with backup routes in place should main roads become clogged) and returning with packaging. Meanwhile, ‘milk runs’ return packing to, and collect parts from, the various UK suppliers while truckloads of more parts arrive regularly from Europe.
Accommodating the second assembly line required a major re-work of warehousing within the factory, reducing the parts stock area from about half the floor space to about a third, extending its height so the storage area is about the same and buying in very flexible forklifts (UK made) that can operate in narrower areas and reach higher.
Separately, a small ‘cell’, using one highly skilled operator and several automated machines, produces knuckle assemblies for the four-wheel-drive Jaguar XF and XJ sedans sold primarily in North America. ZF added this work to the plant late in 2012.
[Editor’s note: ZF Lemforder UK won an award for ‘financial management’ and were also finalists for the ‘customer focus’ award at the National Manufacturing Excellence Awards on Tuesday night (30 September)]