Tower Automotive must get two new product programmes absolutely right in 2004 if it expects to reverse a slide in earnings. The next six months will be a critical period for CEO Kathleen Ligocki, who took over last summer, and the company’s even newer CFO, Jim Mallak.
The US supplier makes structural components and assemblies, lower vehicle frames and structures, chassis modules and systems and suspension components. The two programmes are for Ford, Ligocki’s previous employer, and Nissan.
For Ford, Tower has constructed a new body structures facility at Ford’s new supplier park in Chicago to supply the forthcoming Five Hundred and Freestyle models. The start of production is set for July. Component and assembly certifications are now underway. For Nissan, a new facility in Smyrna, Tennessee, will produce frames for the Pathfinder and Xterra. The start of production is scheduled for August, following what Tower describes as “a compressed launch schedule.”
“The single most important thing we can do for shareholders and customers is to launch these new [US] programmes well,” said Ligocki last week. “So far they have been challenging, but are on track.”
SWAT teams in Chicago
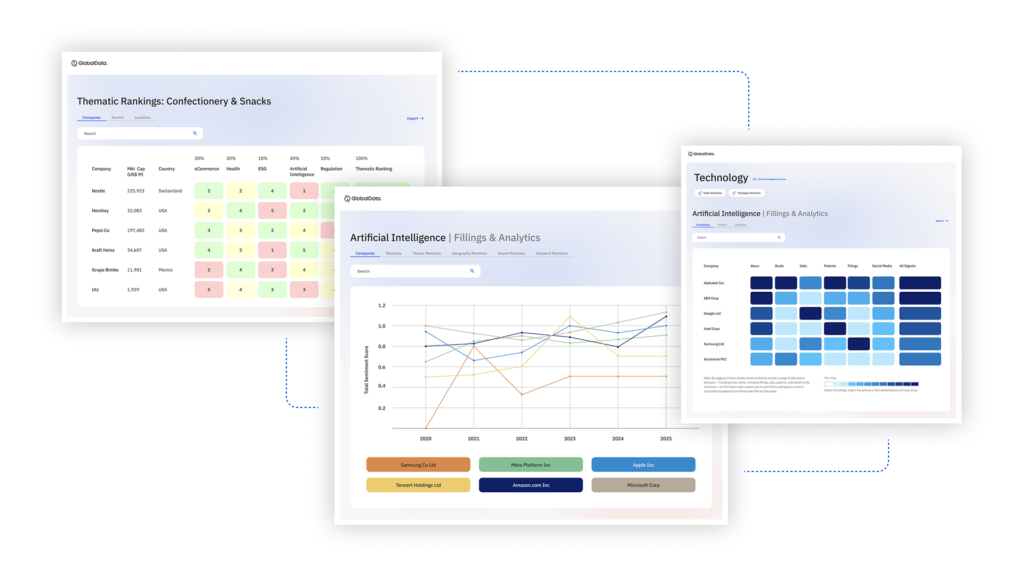
US Tariffs are shifting - will you react or anticipate?
Don’t let policy changes catch you off guard. Stay proactive with real-time data and expert analysis.
By GlobalDataWith the critical production ramp-up period approaching for both, Tower is leaving little to chance – especially in Chicago. SWAT teams with decades of engineering, development and manufacturing experience between them have been put in place to bolster local plant management. Tower’s recent programme launch history has been good, but not perfect, most notably in North America. The company’s Plymouth, Michigan, plant experienced a steeper than-expected learning curve in 2003 as output of an engine cradle for General Motors was cranked up.
Operational debugging, especially involving state-of-the-art laser cutting equipment, had to be carried out through the programme launch. Such experience is not unique. One of Tower’s European competitors, Wagon, has experienced similar teething challenges at its Fontaine, France, plant that is making the Peugeot 307CC body structure. But it is costly.
Glitch-free in Gent
New programme start-ups in Europe have been more relaxed. Commencement of body structures production for the Volvo S40/V50 models at Gent, Belgium, in September 2003 was largely glitch-free.
Tower is also confident that the start-up of body structures output for the BMW 1 and 3 Series in June – involving plants in Germany and Italy – will be equally smooth.
So why are the launches of the Ford and Nissan programmes so vital?
Fourth quarter sales were better than expected – $US717 million versus $681.6 million in the same 2002 period. But the operating profit slipped to $16.4 million from $46.2 million in the fourth quarter. There was a pre-tax loss of $14.2 million, compared to a $26.5 million profit in the same period a year earlier, and net loss of $24.7 million, versus a profit of $17.2 million a year before.
Operating, pre-tax and net losses in the 2003 fiscal year amounted to $57.9 million, $150.7 million and $116.4 million respectively on sales of $2.8 billion. Comparable operating and pre-tax profits in 2002 were $93.2 million and $21.8 million. 2002 net loss was $97.6 million on sales of $2.75 billion.
Launch costs of around $30 million dented second half operating performance in 2003, as did one-off restructuring and asset impairment charges ($157.5 million versus $61.1 million in the full year).
The net result was hit further with a $27.4 million write-down in the Yorozu joint venture.
Tower consumed $5.4 million in cash in the fourth quarter of 2003 and $45.3 million for the full year, pulling total available liquidity down to just $170 million.
With a negative cash flow inevitable in the first and second quarters of 2004, as a further $30 million launch costs in Chicago, Smyrna and elsewhere continue, the margin for error is tight indeed.
Yet Mallak is confident that positive cash flow can be restored as the third quarter progresses, and will accelerate nicely in the fourth quarter.
For 2004, Tower anticipates total revenues of $3.2 billion and EBITDA of $270-285 million ($250 million in 2003), generating operating earnings per share of $0.25-0.40.
Tower needs to get the new programme launches in North America dead right. This includes not only the Ford and Nissan ramp-ups but also the start-up of frame production for DaimlerChrysler’s Dodge Dakota in July.
The BMW contract in Europe also needs to be smooth. Tower’s management is putting every effort into ensuring blemish-free launches at programmed cost levels. But they must also be hoping that the OEMs concerned and other critical suppliers are equally diligent.
Ligocki is optimistic for the short and long term seeing “tremendous potential to improve the operational part of the company”.
But pulling the promise of top-line growth through to the bottom line will be a challenge. A nervous glance over the shoulder at rival Oxford Automotive’s recent financial history is almost unavoidable.
Lessons learned at Tower’s Gent, Chicago and Smyrna facilities will be used to build a more efficient, integrated global sourcing capability in the next 18-24 months with a manufacturing strategy based on sharing of best practice.
SupplierBusiness.com