Engineers at Remploy Automotive have invented a range of ‘error proof’ machines that are revolutionising the way car parts are made.
The intelligent jigs, controlled by a PLC (programmable logic control), have been developed in a five-year research programme and now allow highly complex car, van and truck parts to be made completely fault-free.
The technology has put the firm at the cutting edge of advanced manufacturing techniques and has given the automotive industry a big step towards what it has always dreamed of – zero defect components.
Car, van and truck makers could save millions of pounds in the breakthrough.
General manager John Price said: “This really is the breakthrough the industry has been looking for. We are now building components and sub-assemblies with truly exceptionally low return rates, sometimes less than one-in-a-million.”
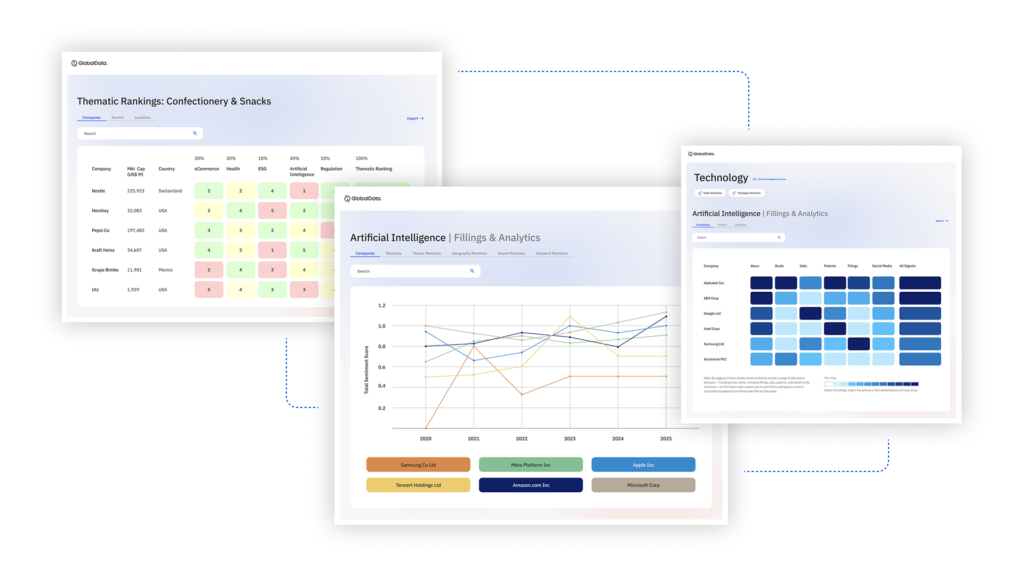
US Tariffs are shifting - will you react or anticipate?
Don’t let policy changes catch you off guard. Stay proactive with real-time data and expert analysis.
By GlobalData“Not only can we build error proofing into every assembly, but we are now introducing error proof management capabilities into the systems. We can now sequence deliveries direct to production lines with the exact part to fit the exact vehicle going down the line, supplied by us just-in-time.
“This isn’t just a step forward in automotive production, this is a world-beating first and everything has been developed by us in-house with the full involvement of our disabled workforce.”
Remploy Automotive was set up as a division of Remploy Limited two years ago and has expanded rapidly. It has grown from six to nine factories, has a workforce of more than 500 people, the majority of whom are disabled, and a turnover in excess of £50-million.
The intelligent jigs typically include as many as 70 individual quality checks. The job cannot be released from the machine until every check has been carried out and verified. Printed compliance stamps can also be added to each component.
Critical functions carried out include the correct orientation and presence of individual parts, torque settings on bolts and screws, leakage tests on emission sensitive parts and the correct operation of electrical components.
The intelligent jigs are already being used for contracts for Aston Martin, Honda, Jaguar, Land Rover, MG Rover, Mini and JCB.
They are used for making components such as thermostat assemblies, water passages, fuel burning heaters, fuel pump and filter systems, mounting brackets, charcoal emission canisters and heaters.
Remploy Automotive has now developed more than 70 of the jigs, each tailored to individual jobs, which are used in its factories at Kitts Green in Birmingham, Coventry, Bridgend and Stoke-on-Trent.
The first prototypes – often called Poka Yoke jigs, the Japanese name for error proofing – were based on a scrap wood frame with proximity switches to check if retaining clips on thermostat assemblies were correctly fitted.
Technical manager Alan Sangster, said: “It took us three months to design the first jig. Now we are producing highly sophisticated jigs that carry out a multitude of safety and quality checks, in just a few weeks.
“One development, which we call torque feedback, gives a massive cost saving on the nearest conventional testing system available, a DC gun. We are constantly looking for innovative cost effective solutions to problems and incorporating them into the new jigs.”
Audio and other systems built into the Remploy Automotive intelligent jigs allow blind and deaf employees to use the devices with 100% accuracy.
The next generation of jigs under development are PC controlled and will have interactive video teaching systems incorporated. Through the use of PIN numbers, linked to the training matrix incorporated in the system, any new employee will be meticulously taken through every part of the building operation, the job being released from the jig after every aspect has been checked.
The computer system will carry a full log of every process of every job so that the parts maker can supply full quality, safety and stock audits to customers on demand.
The jigs will have ‘preventative maintenance’ programmes, which automatically cut in and will not allow the machines to be used until essential calibration and maintenance checks have been carried out.
Sangster said: “Some of the complicated jobs we are being asked to handle can demand a number of management audits in addition to all the physical tests such as target setting, problem monitoring, start up checks, stock control and batch counts. We have devised unique ways of coping with these and have introduced bar coding techniques as well, all of this is vital to modern vehicle production.
“We produce assemblies which can have a number of variants when you take factors such as left hand drive, right hand drive, air-conditioned and non air-conditioned models, petrol and diesel versions and so on.
“If the wrong part is supplied and fitted, even if it is correctly made, the consequences can be devastating. It can halt production lines or result in major rework.
“Our intelligent solutions prevent that ever happening. We have developed intelligent systems that no-one else in the industry can match.”