Suppliers to the redesigned Volkswagen Passat were involved in the development process “very, very early,” said Horst Koenig, project leader, for the B6 model programme.
The programme was signed off by Volkswagen’s management board in March 2002, at which point – 32 months before the start of production (SOP) – the interior and exterior styling was frozen.
“From then we have one year to decide the way to get [the car] to production,” said Koenig.
The development of the car started with the price — “the market has become very price sensitive” said Koenig. “The costs are derived from the price — what can we allow ourselves and what can we not allow ourselves?”
Volkswagen held supplier symposia at which the project team asked suppliers what it could do better, “and we implemented many of these things” said Koenig.
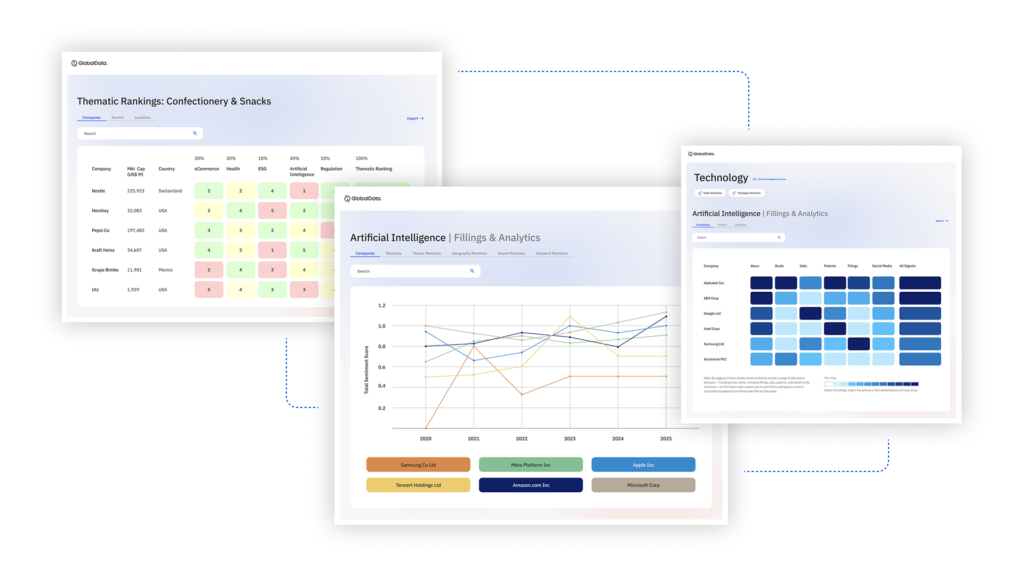
US Tariffs are shifting - will you react or anticipate?
Don’t let policy changes catch you off guard. Stay proactive with real-time data and expert analysis.
By GlobalDataThe team had about 20 supply reviews with, on average, 15 to 18 suppliers that spent half an hour in discussion with the programme team about technologies, deadlines, costs and the product vision, and what the suppliers’ requests were to Volkswagen.
Volkswagen built an information system, accessible to the suppliers, which included all the data of the project – ramp up curve, equipment levels and market introduction dates – except financial data. “Suppliers could get access to this so-called B6 information fulcrum and always get the latest information from it.”
200 tier one suppliers were invited twice to a supply workshop in Emden, Germany, the home plant for the Passat. “The most important thing that they said was ‘please tell us in time when you make changes’,” said Koenig.
The product team held a weekly change round, so there were no delays as a result. “The suppliers brought in very many ideas, some of which we put into the car where there is customer value, whether in acoustics, safety or comfort,” said Koenig.
Point of no return
In August 2002, six months after sign-off, the programme hit stage Lastenheft 1 (LH1). “LH1 is the description of the entire car, including costs, volumes, marketing and engineering costs,” said Koenig.
Over the following six months “we produced the whole car virtually to save cost and time: all the interior and exterior measurements were represented virtually,” said Koenig. This process led to the next key gateway in February 2003, V1PT (Virtualle 1 Protoyp). Also at this point, contracts for tooling the body-in-white were offered.
Then, in August 2003, the watershed stage of Lastenheft 2 (LH2) came around. At LH2, several key things happened: Volkswagen “made the first data control model, a complete car represented in reality and all the stages of cost were finalised” and approved by the management board. “This was the point of no return,” said Koenig.
Also at LH2, Volkswagen awarded series contracts to component and module suppliers, around about 16 months before SOP – exactly halfway between the board signing off and the beginning of series production.
Koenig was programme manager for the Volkswagen Golf IV from 1993 to 1998, then programme manager for the new Polo from 1998 to the end of 2001 and started work on the new Passat in 2002.
Big seller in China
The car is slightly larger than its predecessor, said Koenig, so Volkswagen introduced a new generation of steels that were both lighter and more stable. As a result, the body itself became lighter but the gains were essentially offset by many additional components – bigger wheels, components for the electric parking brake and so on.
The Passat is officially based on Volkswagen’s PQ 46 platform, but there are module and system similarities with the PQ 35 vehicles such as the Golf V. The electric power steering from ZF Lenksysteme is very similar to the system supplied for PQ 35.
Koenig estimated that 5-6% of parts are carried over from the old Passat, and about 8% are common with other models in the Volkswagen range. The Passat is one of the leading models in China, but Koenig says that the fact that it will probably be built in Changchun has had very little impact on its sourcing.
In Germany, the sedan and station wagon are both assembled at Emden, while only the sedan will be produced at Mozel/Zwickau. At full production, projected for the end of May, around 1,300 Passats per day will be assembled at the two sites.
SupplierBusiness.com