The manager of Land Rover’s Solihull body shop has told just-auto.com that the JLR division has not only just completed a second shop but that the frame of a third one is presently going up.
Demos Hoursoglou has been at JLR since October 2011 after 17 years at Honda of the UK Manufacturing (HUM). This week, as part of Land Rover’s 65th birthday media events, he showed journalists around the body shop. This facility was once the East Works during the British Leyland era – the Rover SD1 was built there in the 1970s and ’80s.
“Every shift here has 150 people, each working a 37 and a half hour week. Fifty of those are maintenance workers,” he said. When the operation is running at capacity, Body Shop 1 can produce 95,000 vehicles a year. Currently, it is temporarily at two shifts – series production of the new Range Rover Sport will be the extra shift.
“We start building L494 bodies next week (from 6 May) and many of the outside contractors you see here training our people will begin to leave gradually.” The main suppliers are VDL Steelweld, Comau & ABB (robotics), Tucker (welding guns and rivets) and Kuka (for the cladding line). Many contractors’ employees will remain at Solihull for “two or three years”, Hoursoglou noted.
Will there be many changes needed for the hybrid Range Rover bodies that the shop will commence making later this year? Hoursoglou said no, everything is already planned, though there is of course much to do before Job One (scheduled for the fourth quarter). The model itself will premiere at September’s Frankfurt motor show, and further details are awaited. A Sport Hybrid is reportedly scheduled to follow during 2014.
On the topic of expansion, Hoursoglou proudly revealed a second shop has been fitted out – he wouldn’t be drawn on what it will build – and that a third one is in the first stages of construction. When pressed for more details, a telling grin was followed by a firm “sorry, but no more details”.
How well do you really know your competitors?
Access the most comprehensive Company Profiles on the market, powered by GlobalData. Save hours of research. Gain competitive edge.
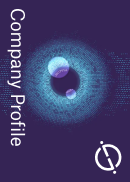
Thank you!
Your download email will arrive shortly
Not ready to buy yet? Download a free sample
We are confident about the unique quality of our Company Profiles. However, we want you to make the most beneficial decision for your business, so we offer a free sample that you can download by submitting the below form
By GlobalDataMaybe those rumours about X260, a supposed alloy-framed XF replacement are true, while X760, the long-overdue effective successor for the X-TYPE, could well be on course for a 2015 or 2016 introduction, as some have said. Will the latter be a 3 Series sedan, GT and/or Touring rival, or perhaps a competitor for the X3? A drip-feed of rumoured details continue to emerge but everyone at JLR remains tight-lipped.
On with the tour of this quiet, sparklingly clean factory where, apart from the robots and shiny aluminium panels, the main thing you notice is how few people are about. Despite the lack of visible population, this is claimed to be the world’s largest capacity aluminium bodyshop. Bodies for the new Sport will be joining those for L405, the still-new Range Rover. Both vehicles are on JLR’s Premium Lightweight Architecture, or PLA.
Hoursoglou kept moving on, keen for us to see as much of the shop as permitted. Having said that, the tour took up only a small, carefully selected part of the plant, though, amazingly, my iPhone camera shot was allowed.
“You will of course notice that we have minimal manpower in this part of the operation. The application of glue and rivets is 100% automated”.
This is the first time I have toured a car factory and not been handed a pair of earplugs. I wondered why there was such little noise.
“There is no welding here”, Hoursoglou said. What about the environmental story? Glad you asked. Our guide said 50% of the aluminium coming into the plant is recycled while a further claim is that just one quarter of the energy of a traditional steel body shop is used here.
Soon it’s time to go but Hoursoglou, a man with an astonishing memory for details of his plant, adds that a body comes through Shop 1 precisely every 142 seconds. Which is after it has received 17 types of rivet, of which there will be 3,722.
I blogged about this earlier so forgive me if you’ve already seen this other statistic but how about this as a final fact? An astonishing (to me) 161m of glue is applied to every Range Rover bodyshell. Leaving Body Shop 1, I found myself dwelling on those expansion plans. Dare I suggest this? Could we be seeing the first seeds sown of a new golden age for vehicle manufacturing in the English Midlands?
[Note to self: find out which adhesive supplier JLR uses and buy some of its shares.]Author: Glenn Brooks