Kia’s UK unit claimed on Friday (2 January) the automaker was already ahead of the game as new EU regulations come into force requiring 95% of a vehicle to be recyclable at the end of its useful life.
The new rules came in on 1 January 2015 and the carmaker said it had already taken a “holistic” approach to the environmental impact of its products, encompassing manufacturing, use and disposal thanks to pioneering techniques developed at the company’s Automobile Resource Regeneration (ARR) centres.
Kia pointed to the recently launched Soul EV which, it said, demonstrates how cars can be green before they even leave the factory through the use of significant quantities of recycled bio-based materials in its interior construction. The company has set itself the challenging target of zero waste from scrapped cars as soon as possible.
That may take some time until new dismantling and recovery techniques are developed but Kia said it can already meet the latest EU directive, which requires 85% of a scrapped vehicle to be recycled or re-used and a further 10% to be used for energy recovery from the combustion of non-recyclable residues.
At its Hwasung factory in Korea, the automaker has been developing end-of-life treatment technologies to reduce the environmental and social impact of its cars since 2005. Hwasung ARR has helped in the way cars are designed and assembled as well as with the choice of materials used in manufacturing.
It has developed an eight-stage dismantling process to recoup as many materials as possible for re-use while ensuring the few components which cannot be recycled are disposed of with minimum environmental impact. Once the car to be scrapped has been registered it is taken into an explosives chamber where its airbags are triggered. The car is then pre-treated for scrappage before all fluids are removed. The exterior, interior and powertrain components are systematically removed in sequence and finally the remnants of the car are crushed in a press.
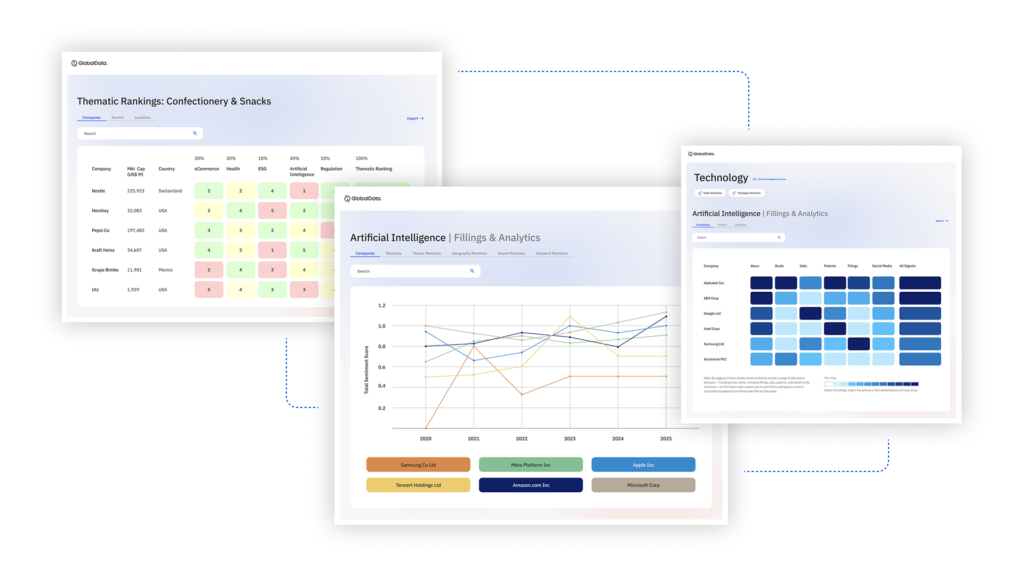
US Tariffs are shifting - will you react or anticipate?
Don’t let policy changes catch you off guard. Stay proactive with real-time data and expert analysis.
By GlobalDataMetal components such as the body, engine and gearbox are relatively easy to recycle, as is the battery and exhaust catalyst, but plastics and rubbers present a greater challenge. Now only 5% of a scrapped car is sent to landfill or incinerated without energy recovery.
The ARR centres work on a conveyor system, almost a disassembly line, so large numbers of vehicles can be dismantled and recycled in a short time span. The technology is used to dispose of crash test vehicles internally and also made available to other auto industry companies to develop end of life vehicle recycling standards and efficiency.