A third assembly line at Jaguar’s Castle Bromwich factory will start making cars for the company’s make-or-break new sportscar, the XK, next month, writes Julian Rendell.
Job One for the new XK, known as project X150, is December 5 and Jaguar is currently ramping-up production towards the plant’s maximum capacity of 13,134 cars a year.
“We’ve completely stripped the old factory and installed new body-in-white [BIW] assembly and final trim lines for the XK, all in the same building,” said Mark Curtis, manager of X150 body construction.
Production of the all-alloy XK has been transferred to Castle Bromwich after Jaguar decided to end production at its Browns Lane headquarters. The XJ flagship saloon was also moved, joining the S-type saloon, which has been built at Castle Bromwich since 1998.
The XK has moved into the old BIW factory, a more efficient production line design making room for both BIW and final assembly in the same factory.
How well do you really know your competitors?
Access the most comprehensive Company Profiles on the market, powered by GlobalData. Save hours of research. Gain competitive edge.
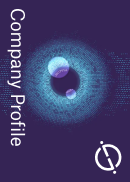
Thank you!
Your download email will arrive shortly
Not ready to buy yet? Download a free sample
We are confident about the unique quality of our Company Profiles. However, we want you to make the most beneficial decision for your business, so we offer a free sample that you can download by submitting the below form
By GlobalDataThe two body variants of XK, coupe and soft-top convertible, are made in the same building, each employing a mixture of alloy pressings, extrusions and castings.
Because the coupe is based on the convertible platform they share 95 per cent of their parts, so the BIW line splits into different body variants only at the last stage of production when the coupe has its alloy roof added. For final assembly they both roll-down the same line.
“By then we will have fitted 2615 rivets into a coupe and 2426 into a convertible and laid on 90m of adhesive,” says Curtis, “there’s just 0.5m of welding and that’s in the coupe only.”
The XK’s body construction is a departure from the XJ saloon, featuring more extrusions and castings in place of the XJ’s predominately pressed panels. “It’s a matter of matching the construction to the lower volume and engineering requirements,” says Curtis.
As a result the XK’s structure is built around two substantial extruded sills, which provide enough stiffness for the open-top convertible. Extrusions are used elsewhere in the XK, too, making up 42 of the parts. Whereas just 14 feature in the saloon.
The balance is reversed on the pressed panel count. In comparison, the XJ saloon uses many more panels – 230 compared to the coupe’s 201.
There’s not as much parts carry-over as might be expected between the saloon and coupe. Only 22 major components, mainly expensive castings, are carried-over.
Just like the XJ assembly hall at Castle Bromwich, the XK factory is eerily quiet, the main noise the hissing of pneumatic riveting machines.
And despite Castle Bromwich having a specialist press shop to make alloy panels for the XJ, all the XK’s major panels come from outside suppliers, mainly Stadco, which supplies them from three UK sites, including the ex-Mayflower facility in Coventry. Smaller panels come from Sertec in Birmingham.
“The XJ press shop is designed around nearly twice as much volume, so it makes sense to out-source them,” says Curtis.
There’s a much greater degree of automation on the new XK than the old one, which had only eight robots, a hangover from its 1970s XJS platform heritage.
By comparison, the new XK has 63 per cent automation on the body line alone. As a result, staffing levels are lower, with 50 workers per shift and a further 50 indirect/maintenance staff for a bodyshop compliment of 150.
Julian Rendell