Ford claims diesel engine production at its wind-powered Dagenham plant is now saving thousands of tonnes of CO2 and diverting almost twice as much waste from landfill.
New data shows that 6,500 tonnes of CO2 a year are avoided by wind turbines installed over three years ago. Other eco-efficient processes prevented over 12,600 tonnes of waste being sent to landfill for disposal.
The Business Commitment to the Environment group had already highlighted in June Ford’s environmental plan behind Dagenham’s new 1.4/1.6-litre engine line with a premier award.
The automaker’s UK eco-efficiency drive was also nominated at Business in the Community’s national “Awards for Excellence 2007” gala this month.
Stuart Burn, Ford technical specialist, said: “We are delighted that our eco-efficient production at Dagenham is recognised.”
How well do you really know your competitors?
Access the most comprehensive Company Profiles on the market, powered by GlobalData. Save hours of research. Gain competitive edge.
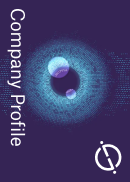
Thank you!
Your download email will arrive shortly
Not ready to buy yet? Download a free sample
We are confident about the unique quality of our Company Profiles. However, we want you to make the most beneficial decision for your business, so we offer a free sample that you can download by submitting the below form
By GlobalDataDagenham recently started making 1.4 and 1.6-litre diesel engines. The engines’ machining and assembly operation was installed with the target of achieving best-in-class environmental protection.
As Dagenham’s output expands towards 1,000,000 engines a year by 2009, the automaker is deploying a parallel plan to improve environmental efficiency including : reduced gas and electricity consumption – resulting in 6,500 less tonnes of CO2; waste elimination and reduction –12,620 tonnes of landfill avoided; ‘green’ vegetable oil for metal working and other fluid actions – over 500,000 litres of mineral oil saved.
Apart from the bragging rights, the eco-efficiency is worth GBP3,400,000 a year in a savings, according to the company.
Dagenham Diesel Centre is Ford’s only wind-powered plant in the world with 3.6MW capacity turbines producing over 6,000,000 kWh of renewable electricity.
Gas and electricity bills are down 12%, thanks to a strict focus on energy intensive operations such as the generation of compressed air for handheld tools on the production line.
Such high usage equipment was scientifically optimised on the new 1.4/1.6 line, requiring 70% less energy per engine compared with other manufacturing lines.
The diversion of 12,620 tonnes of waste from landfill is principally divided between the recycling of dried fluids and of old concrete for the new production floor.
Metal filings and other waste from the machining process are squeezed dry of lubricants and sold on as briquettes for recycling.
When the plant was being prepared for its new 1.4/1.6 line, alongside the existing 2.7/3.6 facility, 20,000m2 of old concrete was broken, pulverised and reused for the production hall floor.