
Toyota has announced multiple days of non-production in April at five Japanese assembly plants, citing Covid-19 related parts shortages.
The cuts affect:
TMC Tsutsumi plant line 2: 4 and 5 April; Toyota Corolla Sport and Camry
TMC Tahara plant line 3: 4 and 5 April; Lexus LS, IS, RC, F, NX
Toyota Motor Kyushu Miyata plant line 1: 4, 5, 6, 7, 7, 11, 18, 19 April; Lexus NX, NX PHEV, CT, UX, UX BEV
Line 2: 1 April; Lexus ES and RX
How well do you really know your competitors?
Access the most comprehensive Company Profiles on the market, powered by GlobalData. Save hours of research. Gain competitive edge.
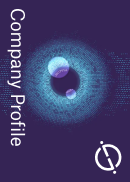
Thank you!
Your download email will arrive shortly
Not ready to buy yet? Download a free sample
We are confident about the unique quality of our Company Profiles. However, we want you to make the most beneficial decision for your business, so we offer a free sample that you can download by submitting the below form
By GlobalDataToyota Motor East Japan Iwate plant line 1: 4, 5, 6, 7, 8, 11, 12 April; Toyota CH-R, Aqua
Line 2: 16, 23 April; Toyota Yaris, Yaris Cross
Toyota Motor Body Fujimatsu plant line 2: 1, 4 April; Toyota Noah, Voxy
Toyota said in a statement: “We… have made repeated adjustments to our production plans due to the parts shortage resulting from the spread of Covid-19, causing considerable inconvenience to our customers and other parties concerned.
“Up until now, we have conducted recovery production with tremendous efforts from the various relevant parties with the aim of delivering to customers as many vehicles as possible at the earliest possible date. However, due to the parts shortage, we have had to make repeated last-minute adjustments to production plans, and this has imposed considerable burdens on production sites including those of suppliers.
“Under these circumstances and in light of a review of past developments, we have revised production plans to be more reasonable in line with recent realities. Specifically, we have positioned the three-month period from April to June as an “intentional pause,” and we will create plans based on the personnel structures and facility capacities of suppliers.
“By doing this, we will establish healthy workplace environments that place the highest priority on safety and quality, rather than exceeding the capacities of facilities, pushing people to their limits, and making do through overtime work. We will then inform our suppliers of plans that incorporate production reduction risks and other factors up to three months in advance, review production plans on a monthly and three-monthly basis, and share these plans with our suppliers.
“Based on the above, our global production plan for April including overseas production is approximately 750,000 units (250,000 units in Japan and 500,000 units overseas). Although the number of units we provided to our suppliers at the beginning of the year includes recovery from previous production cutbacks, due to the impact of semiconductor shortages, we have [cut] our production plan by approximately 150,000 units globally.
“The global production plan average from April through June is around 800,000 units.
“In addition to the shortage of semiconductors, the spread of COVID-19 and other factors are making it difficult to look several months ahead, and there is a possibility that the production plan may be lower. However, we will continue to closely examine the situation of parts supply and suppliers, an make every effort to reduce the scope of sudden production cuts as much as possible, to normalize the production plan, and to reduce the burden on suppliers.
“We would also like to extend our sincere apologies once again to those customers who have been waiting for vehicles to be delivered. By normalizing the production environment, we hope to deliver vehicles with high quality as many as possible. We continue to make every effort with concerned parties such as production, procurement, and sales.”