Toyo Tyre says the Sendai plant in Iwanuma, Miyagi Prefecture, will start switching from coal and fuel oil used at its automotive base to natural gas.
The Sendai plant has been the company’s manufacturing base for tyres since 1962 and, until now, has burned coal and used tyres to produce thermal energy, as well as fuel oil combustion for the cogeneration boiler, which supplies steam and electricity to the factory.
Japan Petroleum Exploration has plans to lay a gas pipeline from Soma LNG Terminal (Shinchi, Fukushima) to Iwanuma, Miyagi Prefecture and to construct natural gas infrastructure which includes the plant area.
Toyo will install natural-gas-fired gas turbines with high heat recovery capacities, which can supply thermal power to each of the facilities at the plant.
Burning natural gas produces none of the SOx (sulfur oxides) which cause air pollution and acid rain and emits little of harmful gases such as greenhouse gas CO2 and NOx (nitrogen oxides), which significantly contribute to photochemical smog. It also allows for the suppression of gypsum sludge, fly ash and various other such waste by-products.
Toyo has set as a goal a 15% reduction by 2020 of carbon dioxide emissions at domestic manufacturing bases and is undertaking various initiatives at each base.
How well do you really know your competitors?
Access the most comprehensive Company Profiles on the market, powered by GlobalData. Save hours of research. Gain competitive edge.
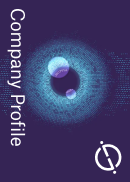
Thank you!
Your download email will arrive shortly
Not ready to buy yet? Download a free sample
We are confident about the unique quality of our Company Profiles. However, we want you to make the most beneficial decision for your business, so we offer a free sample that you can download by submitting the below form
By GlobalDataThe natural-gas-fired gas turbine cogeneration system will run using turbines driven by high temperature and high pressure exhaust gas emitted from the continual burning of natural gas with compressed air.
The torque of the turbines produces electric power, which is supplied to the plant as needed, while hot exhaust gas from spinning turbines is sent to a heat recovery steam generator to generate steam.
The steam is sent via piping within the factory to tyre production equipment (vulcaniser) and elsewhere, while exhaust gas which is waste heat from producing steam, increases water temperature supplied to the heat recovery steam generator through a residual heat recovery device known as an economiser.
The heated boiler feed water supply is raised to 161 degrees Celsius before it is sent to the heat recovery steam generator.