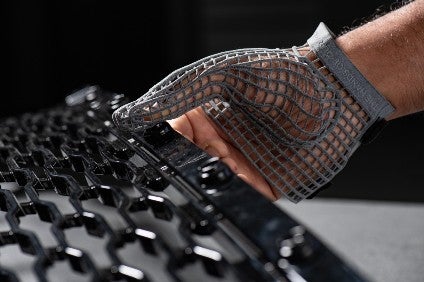
Multiple automakers, including Hyundai Motor Group, BMW, General Motors and Ford, have all announced trials or introduction of exoskeletons and other plant worker aids and now it's Tata Motors-owned Jaguar Land Rover's turn to announce its own, unique innovation: a 3D-printed glove intended to prevent musculoskeletal disorders.
The automaker said musculoskeletal disorders make up about 30% of all workplace injuries so it has developed the glove's innovative lattice structure to protect employees working on its assembly lines.
The glove initially is intended specially for workers required to fit clips or fasteners onto vehicle bodies.
JLR said musculoskeletal disorders include over 100 different types of conditions, account for around 30% of all workplace injuries that result in time off and also for a third of the money paid in compensation to employees.
Musculoskeletal disorders affect an estimated 10% of the global population, rising to as much as 40% in certain industries.
Engineers at the automaker's Gaydon site – where a new development centre has just been opened, and which houses one of the largest 3D printing facilities in the UK – saw an opportunity to use the company's manufacturing expertise to design and 3D print a lattice-style structure which would provide support to reduce muscle fatigue and also be flexible and comfortable enough to wear during an eight hour shift.
Using 3D CAD software, engineers modeled designs in different densities using a variety of materials for testing.
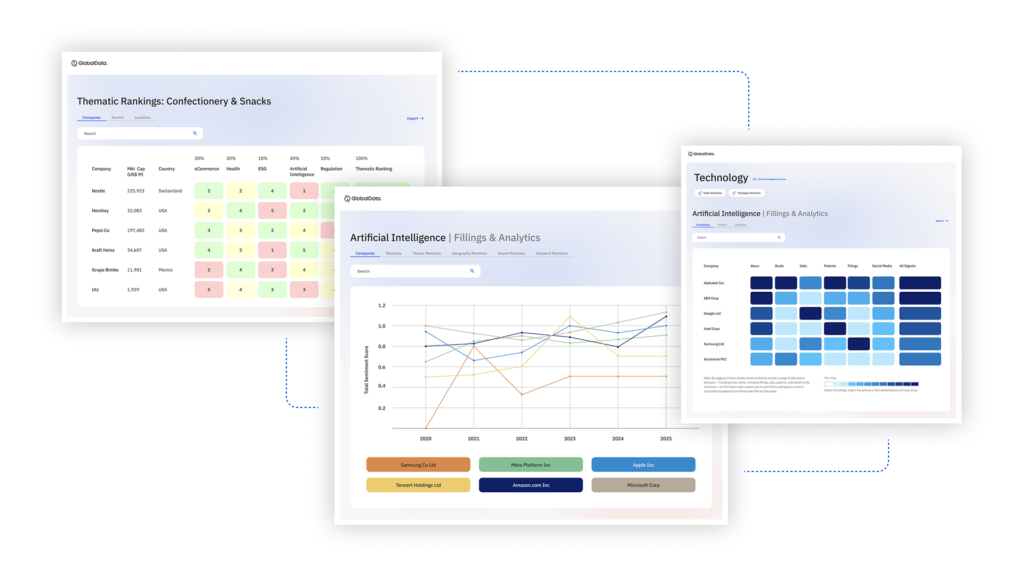
US Tariffs are shifting - will you react or anticipate?
Don’t let policy changes catch you off guard. Stay proactive with real-time data and expert analysis.
By GlobalDataFollowing feedback from trials, they are now working on a second generation prototype which will include a foam pad made using impact additive D30, a polymer material which absorbs impacts when placed under pressure. This will make the glove suitable for those who fit parts, such as door casings, using the palm of the hand.
In the short term, the gloves will be used by workers across all facilities, helping to protect against musculoskeletal disorders.
This project is part of a wider future plan to deploy a range of technology to assist those with muscle weakness, or patients who suffer from physical or neurological disorders, helping employees return to work.
Chris Noble, JLR's additive manufacturing strategic engineer, said: "The health and wellbeing of our workforce remains our priority across all factories and facilities.
"Technologies like the 3D printed glove allow us to use the world leading expertise and equipment we have in house to protect the hands of our [employees], developing equipment that will make JLR a great place to work."
The automaker's additive manufacturing centre produces over 80,000 parts a year for a variety of applications including functional prototyping, design mock ups and manufacturing assembly aids and fixtures.
The automaker can also 3D print parts for production cars with the Jaguar XE SV Project 8 one of the first vehicles to use them.
JLR said the programme forms part of its 'Destination Zero vision', an ambition to make societies safer and healthier, and the environment cleaner.
The company said it focuses is on achieving a future of zero emissions, zero accidents and zero congestion across facilities, and through its products and services.