Volvo has started production of the world’s first diesel plug-in hybrid powertrain which has gone into its V60 model.
In initial batch of 1,000 cars will be delivered during 2013. This will be ramped up to 4,000-6,000 cars from model year 2014.
Assembly of the diesel plug-in hybrid has been integrated on the same production line as regular powered models at Volvo’s Torslanda plant in Gothenburg – something of an achievement considering that the sophisticated plug-in hybrid technology includes two complete drive trains and a battery.
Peter Mertens, Volvo’s research and development head, said: “We are first in the industry to integrate a plug-in hybrid in an established production flow together with other car models.
“The integration in the standard production flow gives the plug-in hybrid buyer the possibility to choose in principle all options available for the standard V60.”
The equipment and additional systems for the plug-in hybrid have seen the final assembly line rebuilt and modified to integrate the assembly of over 300 more parts compared to an equivalent V60.
How well do you really know your competitors?
Access the most comprehensive Company Profiles on the market, powered by GlobalData. Save hours of research. Gain competitive edge.
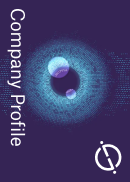
Thank you!
Your download email will arrive shortly
Not ready to buy yet? Download a free sample
We are confident about the unique quality of our Company Profiles. However, we want you to make the most beneficial decision for your business, so we offer a free sample that you can download by submitting the below form
By GlobalDataThe electric motor, along with its drive shafts, is fitted on the same station as the final drive on the standard all-wheel drive models.
The cooling system and the high voltage cables are assembled on the pallet which is used to assemble the car’s drive train and chassis parts. The battery pack is lifted in through the car’s tailgate short side forward. It is then spun a quarter of a turn in the passenger compartment – a manoeuvre that takes 60 seconds and carried out with less than 20mm to spare.
Mertens said: “The 11.2 kWh lithium-type battery is the single most complex system in the car. The precision manoeuvre to get it in place is an excellent example of the assembly process.”