Lear Corporation (NYSE: LEA), one of the world’s premier automotive interior suppliers, has launched two new polymer materials to be used in some of Lear’s future offerings of interior trim products: door panels, pillars and trunk trim. With properties promising optimized occupant safety and cost saving potential, these ultra- lightweight and recyclable polymers could literally save vehicle manufacturers both weight and money. Because they are composed of natural fibres that are replenishable, the two polymers are also environmentally friendly.
The two innovative polymers, natural fibre acrylic and natural fibre polypropylene, have been developed at Lear’s Manufacturing Operation Division’s development center in Ebersberg, Germany, where materials development focuses on vehicle safety and weight reduction. Lear made the announcement on the new polymers at the VISE & VIBEX 2000.
“With these two new polymers, Lear is addressing key material needs for European vehicle manufacturers, who want to reduce weight while contributing to passive safety,” said Randall Carron, President – International Operations for Lear Corporation.
Natural Fibre Acrylic for Door Trim, Package Trays
This patent-pending natural fibre acrylic polymer has been developed for automotive door panel trim, package tray and trunk applications. A so-called “modular binder system” allowing stiffness and impact resistance to be varied according to need offers extreme flexibility for customers. The exceptionally lightweight properties of the natural fibre acrylic polymer also could make it suitable for a range of other automotive interior applications in the future.
“In our extensive testing we have reached a record low weight of 1300 g/m2 – a weight savings of greater than 40% when compared to conventional injection molded substrates,” said Armin Schwaighofer, Material Development Engineer, Lear’s Manufacturing Operations Division in Ebersberg.
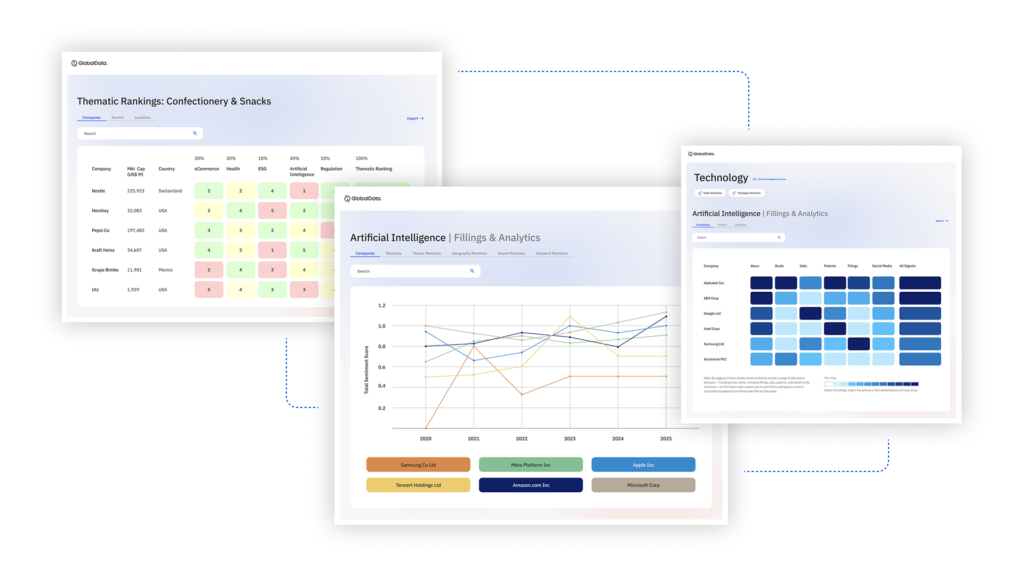
US Tariffs are shifting - will you react or anticipate?
Don’t let policy changes catch you off guard. Stay proactive with real-time data and expert analysis.
By GlobalData“The bending strength of this polymer has proven to be very high, which puts this polymer among the very best in the market right now. The fact that the material consists up to 70% of plant that regrow makes it an environmentally friendly way to use natural resources,” Schwaighofer added.
Selected after months of research, this unique formula of plant fibres and acrylics also offers an improved environment for production workers compared with glass fibre-based polymers.
Natural Fibre Polypropylene for Door Trim, Trunk trim
Natural fibre polypropylene is made from plants that can be regrown that are combined with polypropylene. In this natural fiber, Lear replaced the flax fibre with kenaf, hemp and jute. Additional improvements in mechanical properties were achieved with the use of coupling agents that improve the chemical bonding of fibre and polypropylene. This new material from Lear has superior elasticity, providing high impact resistance. This new “elastic” environment could mean improved occupant safety by eliminating potentially sharp edges caused by conventionally brittle panels that may fracture during an accident.
“Broken interior panels in accidents can sometimes be serious. Our tests have shown that, in an accident, interior door panels furnished with our natural fibre polypropylene are more ‘impact friendly,”‘ said Ulrich Probst, Vice President and General Manager, Lear’s Manufacturing Operations Division in Ebersberg.
Significant cost savings are achieved through the thermoplastic properties of the polypropylene, which allow the material to be reheated. A one-step- process for manufacturing is possible whereby the natural fibre polypropylene is covered with the actual surface material in just one step.
Lear Corporation, a Fortune 150 company headquartered in Southfield, Michigan, USA, is one of the world’s largest automotive suppliers, with 1999 sales of $12.4 billion. The company’s world-class products are designed, engineered and manufactured by more than 120,000 employees in over 300 facilities located in 33 countries. Information about Lear and its products is available on the Internet at www.lear.com