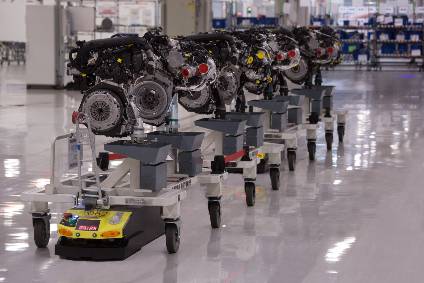
A study by a consulting unit of PwC forecasts that the size of the workforce on auto industry assembly lines and in body and paint shops will be halved because of automation and the new types of vehicles being assembled.
It also said the number of shop-floor logistics roles will be reduced by around 60%, partially because humans will be replaced by autonomously guided vehicles.
However, the study also predicts the number of ‘data engineers’ required will almost double in some types of plants, and increase by 80% in others, while the number of software engineers needed will rise by as much as 90%.
The study also maintains that standardised, shared vehicles — used simply to get from A to B — will account for at least 30% of the market in Europe.
The study by PwC’s Strategy& consultancy suggests that vehicle production will have split between mass-market, largely ‘no-frills’ “cars on demand” that will be rented journey-by-journey and more customised vehicles for those who still want to drive, or be driven in, their own vehicle.
PwC’s Strategy& expects that this will require OEMs to rapidly develop two distinct types of factory. The first will be focused on standardised, networked ‘plug and play’ vehicles aimed at young, urban drivers. The second ‘flex champion’ model will produce customised vehicles for a range of consumers, akin to today’s luxury prestige market.
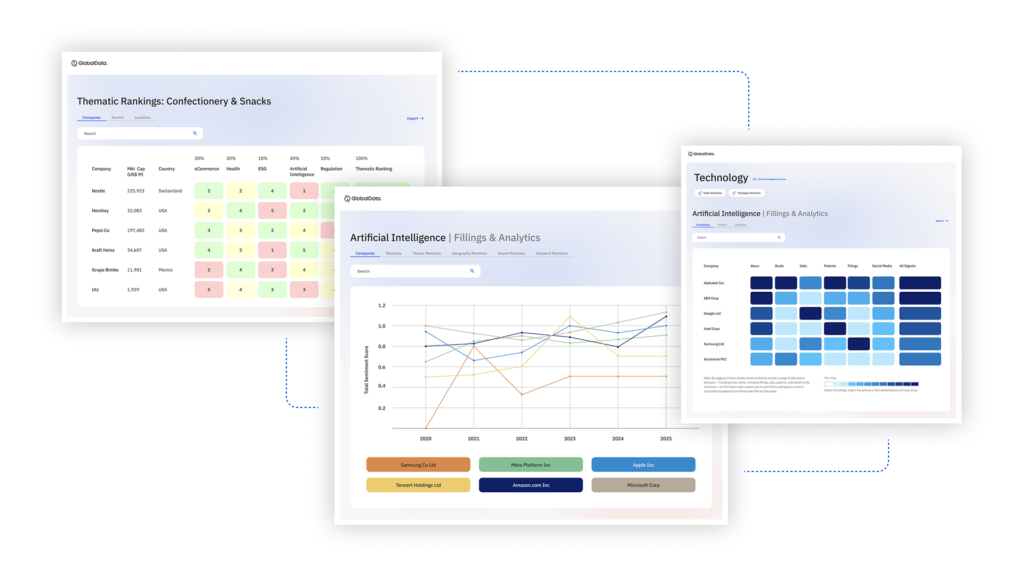
US Tariffs are shifting - will you react or anticipate?
Don’t let policy changes catch you off guard. Stay proactive with real-time data and expert analysis.
By GlobalDataThe study expects this change to radically alter the current workforce as robots take on a greater share of the work, on both assembly lines and in the R&D function. It is estimated that between 40-60% of today’s workers with contemporary skills will be needed on the shop floor, although the required number of data engineers and software engineers may rise by 90%.
“The auto industry has not substantially altered its model since Ford’s assembly lines were introduced over a century ago,” says Heiko Weber, partner in PwC Strategy& Germany, “yet we expect to see many of these changes to gather pace by 2021.
“OEMs must start now to build the workforce they will need over the next decade, both by hiring people with the right skills and by retaining and retraining their existing employees. By 2030 the number of data engineers will almost double in the flexible plant and increase by 80 percent in the plug-and- play plant, while the number of software engineers needed will rise by 90 percent, and 75 percent, respectively,” Weber says.
The study also notes that the pace of change will accelerate in other areas, with the time between R&D and production to shrink to two years, compared to 3-5 years today. There will also be growing competition to OEMs from technology companies who will be able to provide Mobility-as-a-Service (MaaS) solutions directly to consumers.
At the same time, there will be growing pressure on manufacturers to create far more cost-efficient production processes to accommodate an increasingly diverse range of vehicles and designs.
“The auto industry is on the brink of a revolution where data management and the ability to adapt will be essential to survival,” says Weber.
“OEMs should act now, making the right choices for their production models and future workforce,” he adds.