
Ford on Thursday said it was completing a US$2.6bn spend at in its Valencia, Spain, factory, transforming it into what it claimed as “one of the world’s most advanced, flexible and productive auto plants”. But the unmentioned cost was the closure, at the end of 2014, of Ford’s Belgian plant in Genk which used to produce some of the model lines now made at Valencia.
The automaker claimed its spend was the largest in the history of Spain’s auto industry and would allow Valencia to increase output by 40% this year to about 400,000 vehicles with eventual capacity of 450,000.
Eighty percent of production is exported and the plant now employs about 8,000, up from just under 5,000 in early 2013. Suppliers have added a claimed 1,500 jobs since 2013. The axe in Genk cost 4,300 direct jobs and an estimated 10,000 in the supply chain.
Valencia this year will build six Ford models in numerous body styles – Mondeo [Fusion], Kuga, Transit and Tourneo Connect are under way while the redesigned S-Max and Galaxy follow later with the Mondeo gaining a posh Vignale variant later this year.
2011 start
The spend started with an initial $1.25bn announced in 2011, followed by a further $1.37bn since 2013. Valencia will be the sole European production source for the six nameplates assembled at the plant.
How well do you really know your competitors?
Access the most comprehensive Company Profiles on the market, powered by GlobalData. Save hours of research. Gain competitive edge.
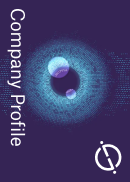
Thank you!
Your download email will arrive shortly
Not ready to buy yet? Download a free sample
We are confident about the unique quality of our Company Profiles. However, we want you to make the most beneficial decision for your business, so we offer a free sample that you can download by submitting the below form
By GlobalDataValencia has produced more than 11m vehicles and 15m engines since production started with the then completely new Fiesta in 1976.
A new 89,000sq m body shop constructed over nearly eight months raises the plant’s vehicle production capability to about 2,000 units per day. For Mondeo production, the plant was retooled to deliver a claimed industry-first application of hydro-formed high strength steel.
An additional paint shop added automated paint processes that remove the need for paint-drying between application stages, and dirt detection technology. This improves quality while delivering energy and productivity savings.
New assembly line processes improve efficiency, all components are now transported alongside the vehicle in a pre-assembled kit, saving time and effort.
Since 2011 more than 900 new robots have been installed in the body shops and 34 in the final assembly areas.
“[New models] will grow the number of parts we manage from 7,000 to 18,000, requiring some fresh and innovative solutions,” said Tony Ades, operations manager, Valencia.
Vignale Centre
Valencia will in 2015 also complete a new Vignale Centre, a specially created department dedicated to ensuring exacting levels of quality and fulfilling customer expectations of Ford’s new upscale Vignale product and ownership experience.
The brand launches this year with the Mondeo and each vehicle will pass through an additional sign-off process where trained experts will assess criteria including paint finish and panel alignment assisted by the latest laser and camera technology.