Mobis is implementing a new just-in-sequence production system a spokesman claimed was “more advanced” than Toyota’s just-in-time system, according to the Korea Times.
The just-in-sequence system allows car dealers to configure a custom-made vehicle ordered by a customer, and for parts deliver and assembly to begin a few days later.
When a request comes in, the system considers the availability of parts nearby, the time to re-sequence the assembly line and whether the change would unbalance the line by scheduling, for example, too many models loaded with time-consuming options one right after the other.
The spokesman reportedly said car makers’ assembly lines and Mobis’ module plant must operate precisely like meshed cogwheels.
According to the Korea Times, Mobis, together with Hyundai and affiliate Kia Motors, has spent several years revamping its ordering, manufacturing and distribution in South Korea to make it easier for dealers and customers to order custom-built vehicles, without disrupting carmakers’ smooth-running assembly lines.
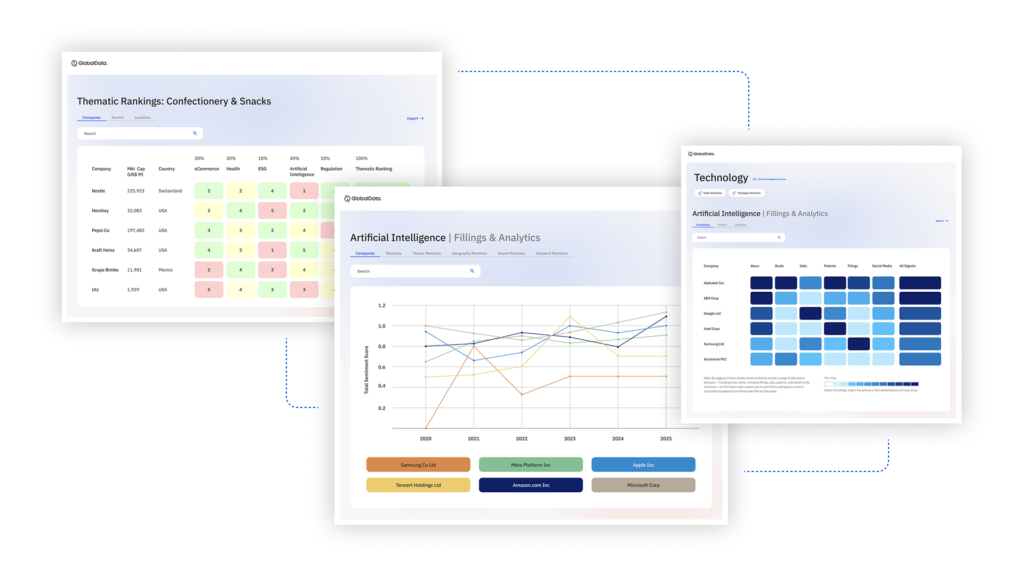
US Tariffs are shifting - will you react or anticipate?
Don’t let policy changes catch you off guard. Stay proactive with real-time data and expert analysis.
By GlobalDataThe aim of just-in-sequence production is to keep assembly line productivity at a maximum by delivering modules in time and to reduce average time between dealer order and delivery from months to a few weeks.
That keeps customers happy, cuts inventory costs and reduces the need for carmakers to spend money on rebates to shift slow-selling vehicles.
Mobis said the just-in-sequence system has trimmed much of the biggest single chunk of time in the order-to-delivery timeline – getting modules from the factory to the carmakers’ assembly lines.
“For the sake of smooth operation of car assembly lines, module plants have to be located in nearby areas. Just-in-sequence is based on the supply park concept. Module plants should be within 120 minutes of car assembly lines at most,” the spokesman reportedly said.
“Mobis will extend the just-in-sequence process to foreign markets where our production bases are located, including the United States and India,” he added.
The Korea Times said the auto parts maker plans to apply the just-in-sequence system to the production of Hyundai’s Santro, called the Atoz in Korea, in India by early 2007, as annual production ramps up to 400,000 units by then, from 250,000 units last year.