Ford has provided more details of the strengthened role of South Africa as a major vehicle and engine parts export hub after production of the Duratorq TDCI engine began at its Struandale, Port Elizabeth, engine plant.
Local production of the engine is part of SAR3.4bn (US$500m) export investment programme that includes the upgrade and expansion of production facilities at the engine plant as well as the Silverton vehicle assembly plant in Pretoria.
The upgrades have boosted Struandale capacity to 75,000 engines a year and 220,000 engine component kits.
Struandale’s Duratorq TDCi engines will power the next-generation global Ford Ranger pickup truck [the Thai rather than US version of the same name – ed], to be built in Silverton which now has an expanded annual production capacity of 110,000 vehicles.
“This new diesel engine will help drive our transformation in South Africa, and it is a key reason the new Ranger pickup truck is a class leader in such a globally competitive segment,” said Lewis Booth, Ford executive vice president and chief financial officer.
“I am pleased to announce today that this new Ranger will be exported from South Africa to 148 markets around the world, solidifying South Africa’s role as a key operation in Ford’s global manufacturing footprint.”
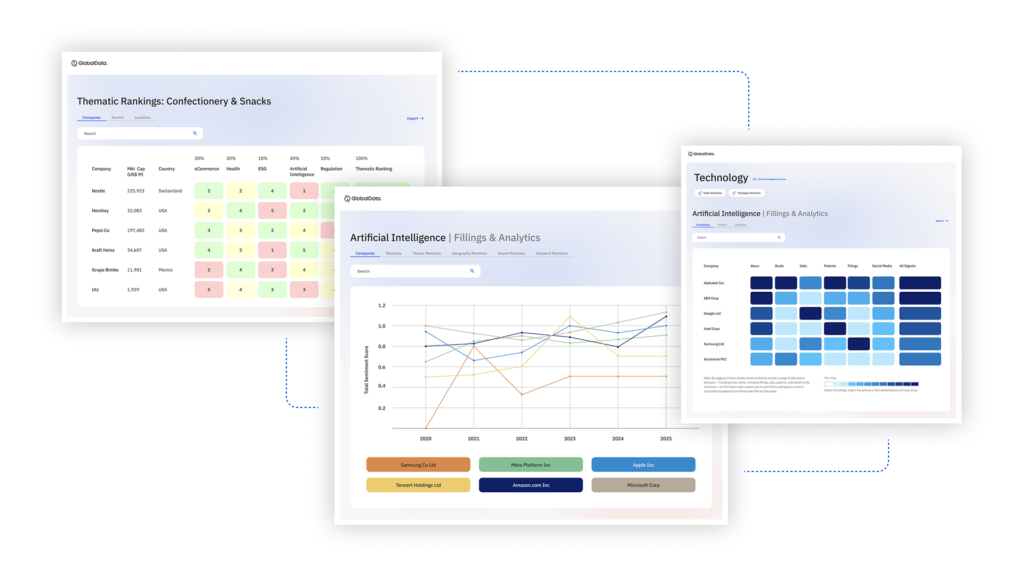
US Tariffs are shifting - will you react or anticipate?
Don’t let policy changes catch you off guard. Stay proactive with real-time data and expert analysis.
By GlobalDataFord has previously sourced all but US Rangers from the AutoAlliance plant operated with Mazda in Thailand. The plant also builds Mazda’s BT-50 variant.
Booth joined employees and key stakeholders at a launch celebration this week in South Africa, where he was group managing director from 1997 to 2000.
“This programme is more than just an engine, it is confirmation that our Struandale engine plant is truly world-class in every respect” said Jeff Nemeth, FMCSA president and CEO. “The remarkable transformation that has taken place is the result of the extraordinary dedication and support of our employees, suppliers and partners.”
Uniquely, the Struandale engine plant is the only Ford factoru that shares both component machining and engine assembly for the Ranger’s Duratorq TDCi diesel engine. The machined components are used for engine kits which are exported to other Ranger assembly plants and the fully assembled engines will be used in the South African-built Ranger.
“The diesel engine programme represents an entirely new era for the Struandale plant which, through Ford’s stringent global quality standards, has undergone a complete transformation to ensure that it competes with the best in the world.” said plant manager, Wallace Yearwood.
Over the last 24 months, the plant has been completely overhauled, including the construction of an entirely new assembly hall for the Duratorq TDCi, which expands the total floor area to 16,514 sq m.
The assembly hall was fitted with the latest, most advanced equipment, systems and processes and complemented by a specialised clean-room, cold and hot-test benches as well as a new dynamometer specifically developed for the production of the high-torque diesel engines.
“Employee training has been central to this project. We launched a new training centre last year, and every operator has been through extensive simulation training to ensure that we’re able to deliver engines that meet all quality, cost, and efficiency requirements. Our employees are simply the best.” Yearwood added.