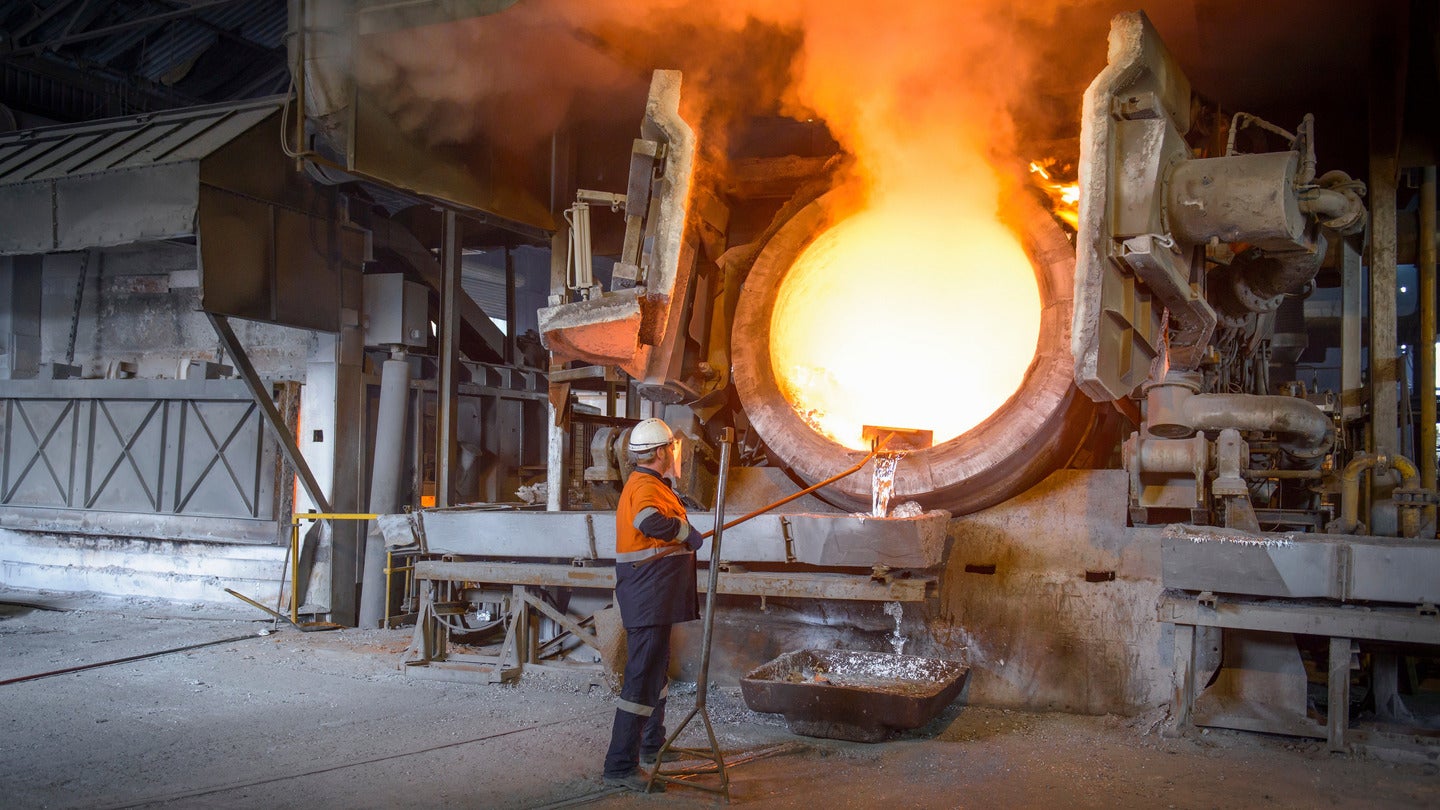
As the world gears up for the launch of COP28 on 30 November, automakers are facing unprecedented economic and logistical challenges in the effort to achieve “deep decarbonisation” across their supply chains.
Closed-loop aluminium recycling is one such challenge, with a mismatch between suppliers’ desired alloy mix and what is currently in the scrap recycling stream.
A panel of metal-recycling experts at the annual Aluminum Tech Forum in Detroit, held in November, noted that current recycling processes produce alloys that are contaminated with foreign materials, such as iron and copper, and that the current scrap stream largely consists of dismantled vehicles from around 20 years ago, making it ill-suited to the light-weighting requirements of modern vehicles.
Another difficulty is the growing switch from casting to wrought alloys, which require lower levels of alloying elements and impurities than what is typically found in post-consumer scrap.
The consequence is that while an impressive 91% of scrap car aluminium is recycled in the US, very little of this remains within the automotive sector, being downcycled into the construction industry.
Primary aluminium production, however, is environmentally costly, accounting for 3% of the world’s direct industrial CO2 emissions (270Mt of direct CO2 emissions in 2022). Conzade et al. found that aluminium represents 35-50% of the material carbon footprint of an EV, compared to 10-20% for other battery materials.
How well do you really know your competitors?
Access the most comprehensive Company Profiles on the market, powered by GlobalData. Save hours of research. Gain competitive edge.
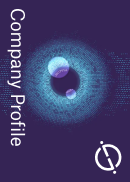
Thank you!
Your download email will arrive shortly
Not ready to buy yet? Download a free sample
We are confident about the unique quality of our Company Profiles. However, we want you to make the most beneficial decision for your business, so we offer a free sample that you can download by submitting the below form
By GlobalDataAluminium consumption and production in the auto sector is also ramping up, driven by increased usage in car bodywork, battery pack enclosures and charging infrastructure, with global production of bauxite ore expected to reach 406 million tonnes by 2027, according to GlobalData. Automotive consumption of aluminium is expected to increase by a factor of around four towards 2050.
In its 2022 Impact Report, Tesla reported that aluminium accounted for 18% of its scope 3 emissions while highlighting that its in-house alloy development was allowing for recycled inputs to be used in high-performance applications.
The company said, however, that “because of total rising global demand for aluminium, merely shifting to recycled inputs is not enough to affect the magnitude of change needed to reach a truly sustainable aluminum sector”, hinting at the need for decarbonising primary production.
However, a dynamic material flow analysis model published in March suggests that decarbonisation of primary production is insufficient to offset the increasing total carbon footprint of aluminium in cars. “[The decarbonisation] technology transition takes time,” the study’s chief authors said. “[According to the model], an increase in the annual carbon footprint up to 2030 seems unavoidable, making it hard to mitigate the increase in cumulative emissions, the most relevant metric for measuring the contribution of the sector to climate change.”
In light of growing aluminium demand, the researchers said that “without the deployment of alloy sorting technologies, all scenarios lead to a scrap surplus starting in the coming years and increasing to more than 10Mt/yr in 2050, highlighting the need for such technologies to support the transition to electric mobility.”
Engineering the way towards closed-loop recycling of aluminium
One solution is for OEMs to design cars with a higher tolerance of “dirty scrap”. Jaguar Land Rover, for example, has reduced the need for primary aluminium from 40-50% to 25%, after having completed its REALITY (Recycled Aluminium Through Innovative Technology) three-year research project looking at how aluminium waste can be recycled for use in new cars.
Arconic Corp is also innovating in this area, having developed alloys with improved recyclability and improved tolerance levels of recycled content. In its May company filing, it claimed that its C1A0 alloy is being used in several popular EV models on the market today.
Speaking at the Aluminum Tech Forum in November, Daniel Cooper, an assistant professor in mechanical engineering at the University of Michigan, said that emerging technologies such as laser-induced breakdown spectroscopy also offer a solution for better separation of alloy families. However, these dismantling and alloy-sorting technologies will need to be developed and deployed at the same pace as the electrification transition to avoid excess aluminium scrap.
Research into solid-state electrolysis for upcycling impure scrap into high-purity aluminium is also advancing. However, its practical feasibility or successful commercialisation has yet to be demonstrated.
*Metal decarbonization* is essential for deep decarbonization. Electrolysis is an elegant solution and is now being pursued for decarbonizing ironmaking and other industrial processes. However, aluminum is already electrolytic and is still stubbornly CO2 intense. Why? 🧵(1/19) pic.twitter.com/ror5eEWk56
— Jacob L Brown (@JacobLBrown) November 28, 2023
Other encouraging signs include Volkswagen’s Audi’s successful implementation of closed-loop aluminium recycling processes at three plants in Neckarsulm, Ingolstadt and Győr, yielding a saving of 633,881 metric tonnes of CO2 since 2017.
Mercedes-Benz has also expressed its intention to “transform its entire value chain into a closed loop”, and in December 2022, revealed that it had signed a letter of intent with aluminium manufacturer Hydro to develop and produce “practically CO2-free” aluminium and explore solutions for implementing closed-loop recycling.
Our signals coverage is powered by GlobalData’s Thematic Engine, which tags millions of data items across six alternative datasets — patents, jobs, deals, company filings, social media mentions and news — to themes, sectors and companies. These signals enhance our predictive capabilities, helping us to identify the most disruptive threats across each of the sectors we cover and the companies best placed to succeed.