Supplier Schaeffler said it was working with IBM to create a digital platform for processing large amounts of data, "generating valuable insight to transform" operations.
This month it introduced the 'Schaeffler Cloud' for first user cases and applications.
IBM will be the technology provider, consultant and development partner for a digital ecosystem to support Schaeffler in the integration of mechatronic components, systems and machines into the rapidly expanding 'Internet of Things' (IoT), as well as implementing market ready new business models based on digital services. To start, the two companies have built a platform for all of Schaeffler's added-value digital services.
"We are constantly working to offer significant added value for our customers. Our aim is to connect data from across products and processes. Using analytics we turn this primary data into valuable insight which is used to increase the efficiency of our operations and develop innovative services for our customers," said Peter Gutzmer, Schaefller's deputy CEO and chief technology officer.
Digital agenda
Gerhard Baum, the supplier's chief digital officer, said: "We are concentrating on expanding the integration of sensors into our existing products as well as developing new products with integrated cognitive software. Not only will the machines and transport infrastructure within the production environment be connected but individual plants will also be digitally linked to the whole supply chain. We want to digitally optimise processes and procedures as well as create new service-oriented processes, and thus drive the digital interaction between people and IT systems."
How well do you really know your competitors?
Access the most comprehensive Company Profiles on the market, powered by GlobalData. Save hours of research. Gain competitive edge.
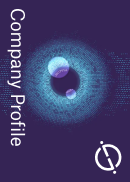
Thank you!
Your download email will arrive shortly
Not ready to buy yet? Download a free sample
We are confident about the unique quality of our Company Profiles. However, we want you to make the most beneficial decision for your business, so we offer a free sample that you can download by submitting the below form
By GlobalDataIBM Germany said the base would be a global, hybrid cloud infrastructure using the 'Bluemix' application platform with Watson IoT to create differentiating applications and mobile apps.
Schaeffler said it had put significant investment into auto components research and development in recent years and incorporated sensors, actuators and control units with embedded software into its products.
"With this, it is now possible for these parts to collect and process valuable data on the condition of a machine and then convert this data into added-value services."
New technologies will allow Schaeffler to extend the functionality and lifespan of components for the automotive industry. Real time analytics and cognitive systems will turn data from components and systems into valuable insight which can be used by manufacturers to increase the reliability of cars and offer new value-added services to customers.
IBM's cognitive technologies will support Schaeffler's Industry 4.0 strategy for tooling machines helping to improve overall equipment efficiency (OEE). This includes the optimisation of production processes, real time analysis of data and context-driven maintenance, networking and optimisation of multiple machines within a production line. The objective is to continuously optimise production and supply chain. Focus is on internal optimisation to increase efficiency and to leverage this for the creation of new service offerings for customers and partners.
Schaeffler workers are monitoring the condition of thousands of machines and pieces of equipment on and off site. 'Big data' is transmitted to the operation centrr and processed in the cloud. Algorithms and cognitive approaches will analyse data helping to make predictions about machine performance and create opportunities for optimisation. Irregularities and potential faults are automatically identified and corresponding actions rapidly initiated.