A Czech-Korean plastics supplier says it has been compelled to use more robots in its factories as the contracting pool of employees in Eastern Europe starts to become a serious difficulty.
Located in the Moravian region, Plakor manufactures bumpers, spoilers, dashboards, and other interior and exterior automotive applications but, in common with other suppliers in the region, is coming up against myriad companies vying for a diminishing employee base.
The battle for staff was a rich seam running through last week’s Central and Eastern Automotive Forum in Prague, organised by Adam Smith Conferences, with several companies highlighting the same problem as the Czech Republic continues to attract large numbers of overseas OEMs and Tier 1 suppliers.
“The most pressing problem for us is a shrinking labour pool in the Czech Republic,” said Plakor Czech director, Tae Yun Yee in Prague. “Now we are facing the problem we can’t find entry level operators just for the factory.
“We are very happy we invested in the Czech Republic but the problem is other suppliers know it is a great place to have a company so we are facing competition for the same small labour pool.
“So we have resorted to increasing use of robots in our factory. We also use sub-contracting companies for work which, of course, is not without its own problems. Related to this problem is the very quickly rising economy of this region.”
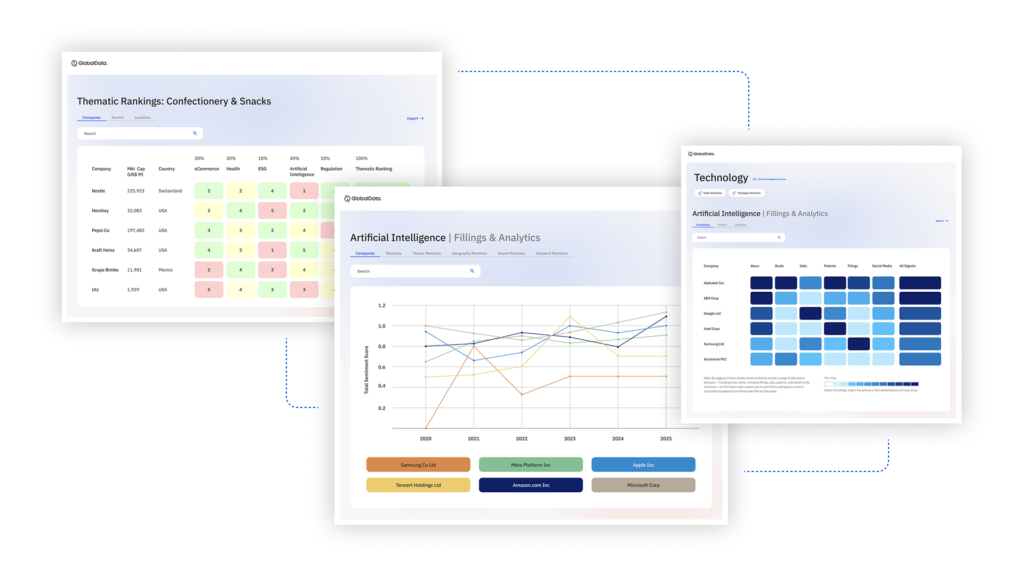
US Tariffs are shifting - will you react or anticipate?
Don’t let policy changes catch you off guard. Stay proactive with real-time data and expert analysis.
By GlobalDataPlakor maintains access to staff – and crucially retaining them – has become a distinct challenge leading the supplier to offer incentives to encourage employees to stay and also offer training.
“Whether it is working or not, I don’t know, it is something we are trying to work out,” added Tae. “We are looking forward to working with other suppliers and central government to find a solution for this very small, shrinking labour pool.”
Tae also offered the observation Plakor – Plastics Korea – had developed its own internal form of communication as the two languages of Korean and Czech met in a mutual way of comprehension while there were other cultural differences to overcome as well.
“We had Korean-style broken English meeting Czech-style broken English,” he said. “They have developed their own language at our company.
“Another difference is the very different work style. The Korean system is very militaristic, top-down decision making, which we learned very quickly, does not work in Czech Republic.
“You can’t expect someone to follow orders without knowing why. We want to have feedback from our employees. Czech employees work to live – Korean employees live to work.”
Plakor is a group of Tier 1 suppliers with companies in China, South Korea, Mexico, Czech Republic, UK, Germany and Japan.