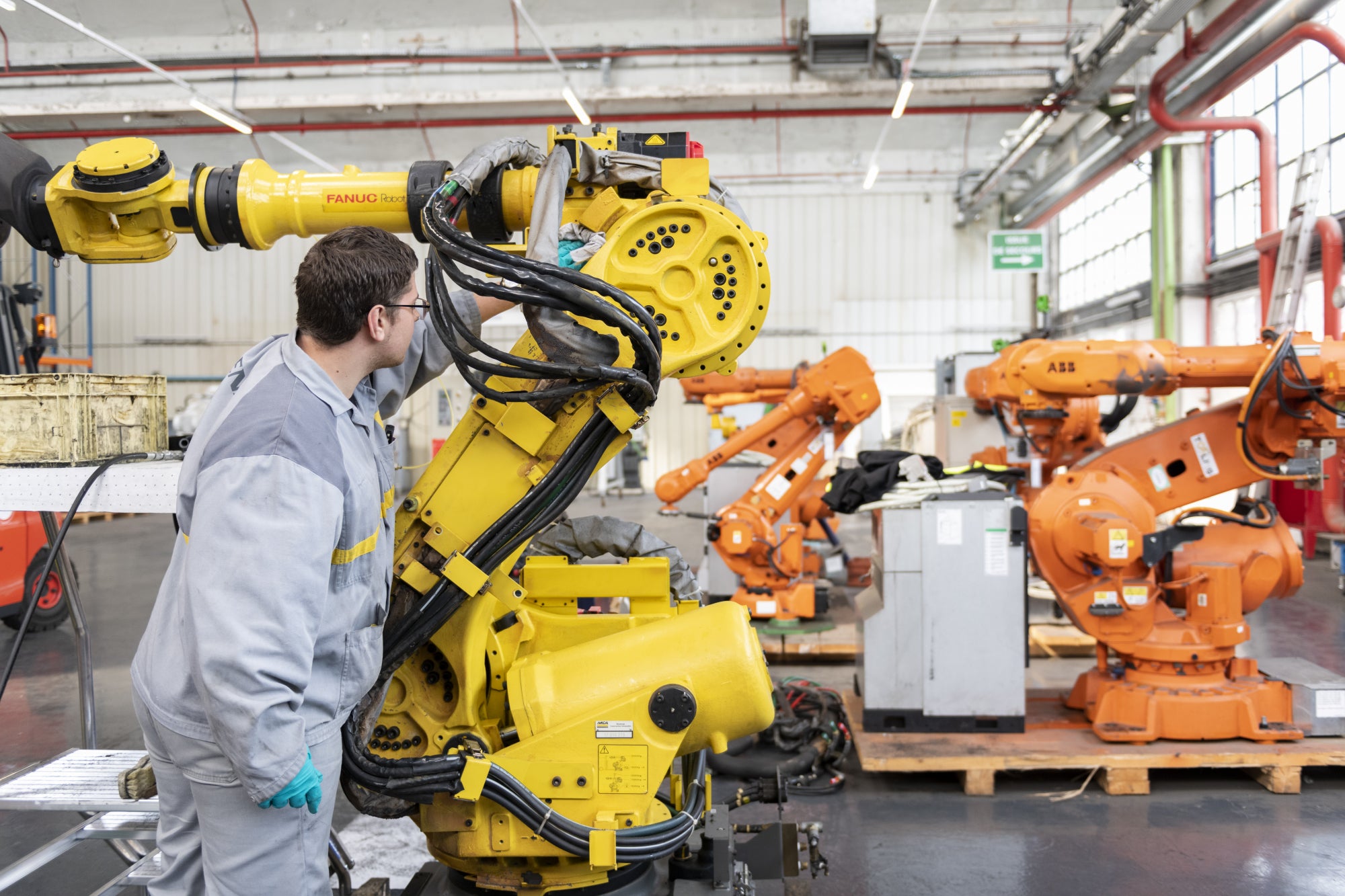
At the end of 2020, the Renault plant in Flins (France) embarked on a new path to focus entirely on the circular economy. The consequent Refactory was developed to refurbish used vehicles and now houses a new workshop that retrofits robots.
The Retrofit unit is tasked with refurbishing them before they return to production lines. This unit has revamped 40 robots so far this year to contribute to substantial projects such as the starte of Megane E-Tech Electric in Douai.
Sandouville, Maubeuge and Douai… sharing robots
Robots retired from plants in Sandouville, Maubeuge and Douai are gathered in the workshop which Nathalie, Deputy General Manager Tooling in Flins, runs. In the past, each plant retrofitted its own machines. Now, the Refactory revamps them all, to enjoy the benefit of specialist teams pooling their expertise in a dedicated workshop. By 2023, the team will double in size and have eight technicians and a scheduler.
Once the robots are cleaned, the ‘roboticists’ examine them to determine what they need to do to recondition them. It can be replacing the electronic card, harness, motor or wrist (part of the arm). It takes about 40 hours to retrofit a robot.
The robots that came here in 2021 were from Maubeuge plant, when it stopped producing the previous Kangoo and started producing the new version in a new building. The first 18 welding and handling robots were dismantled and sent to Flins for a makeover. Once refurbished, they will take up their new duties in Douai, on the Megane Electric assembly line.
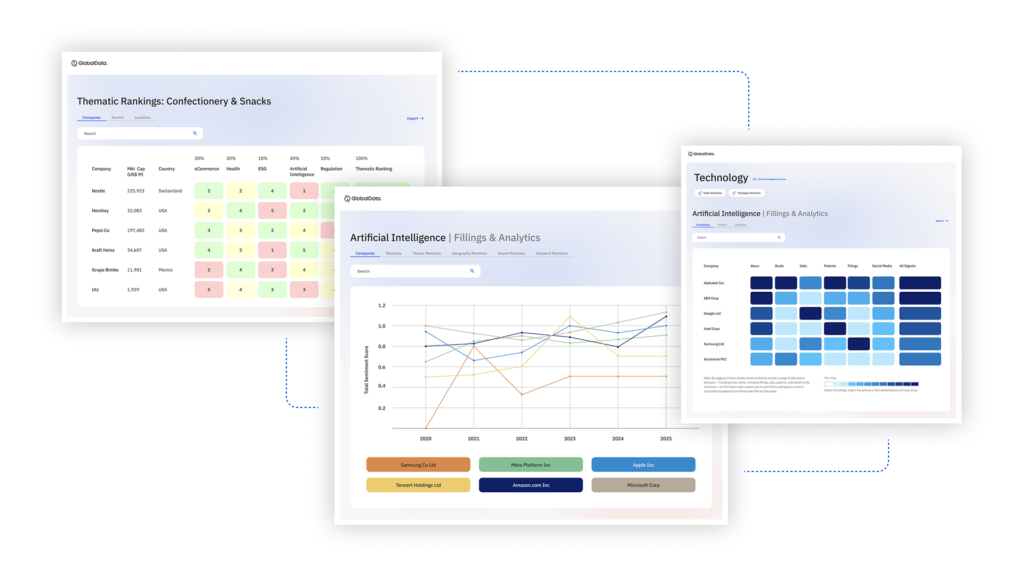
US Tariffs are shifting - will you react or anticipate?
Don’t let policy changes catch you off guard. Stay proactive with real-time data and expert analysis.
By GlobalData“By pooling robot retrofits, we have reduced investments in new projects and repair costs. This operation has also shortened supply chains – which are getting longer and longer for new robots – 40 weeks instead of 20 weeks initially,” said Nathalie, deputy general manager tooling
Stages of metamorphosis
There are several steps to go through before retrofitting robots: recording the models’ end of production dates, determining when facilities will be available and centralising plants’ requirements. This is what Gabriel, an industrial capacity life cycle architect, does. His job is to coordinate all the inventory operation with a contact at each plant and liaising with future customers. After the first step, assigning, the retrofit crew takes over robot dismantling, transport and transformation. They clean them, drain them, change parts, update the system, test their accuracy and endurance, and prepare them to ship. All those steps are necessary to revamp production systems properly.
The workshop, which started up a year ago, is already extremely successful and orders for robots are flowing in. Renault Spain has signed up to revamp part of the sheet metal shop at the plant in Valladolid (where the Captur is made). The plant has ordered six robots (including four crimping ones), which will be supplied by Sandouville then retrofitted in Flins. To deal with all these requests, the workshop is also planning a makeover: in July, it will be extended and house new facilities to increase its capacity.
It is already preparing a few robots for the upcoming electric Renault 5 which will be made in Douai within the ElectriCity sites.
“We are using every opportunity to increase our choice of robots and meet group plants’ requirements,” said Pascal, an assembly process design specialist. “Starting in 2023, our objective is to retrofit 170 robots a year to supply ElectriCity projects. This operation will save EUR3m a year.”
“This new and economically virtuous operation is meeting challenges around the ecological transition and more sustainable consumption. Buying less, extracting value from products that already exist and creating a new industrial model centred on the circular economy is one of Renault Group’s priority commitments,” the automaker said.