There are tentative signs that the weak trends in the Polish automotive sector may be reversing. Car sales were up almost 12% in the first nine months of 2003, and the launch of the new Fiat Panda, produced in Tychy, will give production a strong boost. SupplierBusiness.com reports
Fiat currently produces three models in Poland: the Seicento, the Palio Weekend, and the new Panda. Fiat invested €570m in new production lines for the Panda, and local content is content is high at between 60% and 80%, depending on the specification. Around 180 suppliers to the Panda are based in Poland. This compares with 46% local content on the Palio Weekend. 44 international suppliers set up local entities to supply Fiat during the 1990s, when investment in the Poland by GM, Daewoo and Fiat was at its peak. These suppliers include Bosch, Delphi, Lear and Valeo, as well as Fiat-controlled Magneti Marelli and Teksid.
Having lost the opportunity to house the new PSA-Toyota plant, which went to the Czech Republic, and with the PSA plant now being built in Slovakia, Poland is once again on the shortlist for a major new OEM plant and is competing with Slovakia as one of the final two locations for Hyundai’s new US$1.5bn, 300,000-unit facility. While Slovakia remains the favourite to win the final selection, Poland’s position in the final two suggests it can now compete more strongly for new automotive investment. Victory over Slovakia would be a significant boost for the supplier sector. Hyundai’s new plant in Montgomery, Alabama, which is currently under construction, has attracted 22 tier 1 suppliers, including many from South Korea. While a new Hyundai plant in Poland would probably attract lower inward investment from tier 1s, the overall contribution to the country’s foreign direct investment would be substantial.
One of Poland’s problems is that it does not have a government agency that is fully able, on behalf of the government, to provide all necessary support needed in negotiations with international companies, automotive OEMs and suppliers included. As a result, in spring 2004 a new agency is being formed called the Polish Agency for Economic Promotion (PAPG). With no single investment agency, such as CzechInvest in the Czech Republic, or Sario in Slovakia, potential investors in Poland have found themselves communicating with several different institutions, which is both inefficient and time-consuming.
The overall business background in Poland has also become more favourable. In January 2002 Poland’s new left-wing government, led by Leszek Miller, unveiled its long-term economic programme. As part of this four-year plan there is a ‘Package for Entrepreneurship’, which offers advantageous policies to businesses. The package is aimed at easing the tax and administrative burdens on Polish and foreign companies. The government has also recognised the need to improve infrastructure. Most of the main roads in Poland were built or modernised in the 1970s and are not capable of handling consistent, heavy truck traffic. According to estimates more than 70% of the roads need renovation to meet EU standards. The government plans to invest US$4bn (€3.44bn, 31 October 2003) in new highways by 2005.
See Also:
![]() |
Click image to enlarge
|
Despite the challenges faced by OEMs and suppliers in recent years, some substantial pockets of progress have been evident. These indicate that Poland can become an important development and manufacturing base for international suppliers, even if domestic vehicle manufacturing trends are challenging. A number of key examples outline these successes.
How well do you really know your competitors?
Access the most comprehensive Company Profiles on the market, powered by GlobalData. Save hours of research. Gain competitive edge.
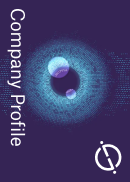
Thank you!
Your download email will arrive shortly
Not ready to buy yet? Download a free sample
We are confident about the unique quality of our Company Profiles. However, we want you to make the most beneficial decision for your business, so we offer a free sample that you can download by submitting the below form
By GlobalDataMahle has been active in Poland as an OE supplier since 1999 when it acquired a plant in Krotoszyn. Mahle now has two plants, Mahle Krotoszyn S.A. and Mahle Sp. Z.o.o., both of which are located in Krotoszyn. On 1 January 2004 the two companies will merge to form Mahle Polska Sp. Z.o.o. Birgit Albrecht, spokesperson for Mahle, is clear about the advantages and disadvantages of the country, “It is easy to export due to adapted rules and regulations, there is low inflation, a relatively stable currency, and other positive economic indicators. However, there is weak infrastructure in Poland compared to Czech Republic and Hungary.
CASE STUDY: DELPHI
|
Delphi initiated its business in Poland in 1994 with 250 employees. Today, Delphi’s organisation in Poland is the biggest in central and eastern Europe, employing over 5,000 people in six manufacturing plants and a Technical Centre in Krakow (TCK). Delphi has invested over $255m in Poland and is the biggest component manufacturer in the region. Delphi Poland exports nearly 80% of its total production, which has grown around 20% reaching $330m in 2002. The present OE customer base of Delphi plants in Poland includes: Alfa Romeo, BMW, Daewoo, DaimlerChrysler, Fiat, Ford, GM, Isuzu, Jaguar, Opel, PSA Peugeot Citroen, Renault, Rover, Saab, Suzuki, Toyota, Volkswagen, Volvo Cars and Volvo Trucks. DELPHI PLANTS IN POLAND: Jelesnia The plant in Jelesnia, which manufactures wire harnesses, employs around 2,400 people. The plant’s customer base includes Fiat, Volvo, Isuzu, DaimlerChrysler and Volkswagen. Blonie, near Warsaw The plant in Blonie manufactures round and rectangular fuel vapour canisters and EGR for customers such as: BMW, Daewoo, Fiat, Rover, Saab and Volvo. Tychy Delphi’s steering systems manufacturing plant in Tychy was built as a greenfield investment in the Special Economic Zone. The plant, employing 260 people, makes use of the latest ‘lean’ production systems, manufactures drive axles, hydraulic power steering gears and EPS columns. Among the clients are Toyota France, Saab, Opel and Daewoo. The site in Tychy is Delphi’s largest capital investment in Poland. Ostrow Wielkopolski The plant in Ostrow Wielkopolski was created in 1996 after the acquisition of Zaklady Sprzetu Mechanicznego, It is Poland’s largest manufacturer of car radiators and heaters and now employs over 600 people. The plant manufactures a large range of heat exchangers for its customers: Fiat, Opel, Daewoo, and Renault (Laguna II and Vel Satis). In co-operation with Delphi Diavia, Ostrow supplies Lamborghini (Diablo and Murcielago) and Ferrari with condensers. The operation supplies HVAC modules for the Volkswagen Touareg/Porsche Cayenne models. Gdansk This mechatronics plant was acquired by Delphi from Eaton Corp. in March 2001. It is a greenfield investment with employment of 600. The plant manufactures a wide range of switches for leading OEMs: Ford, BMW, GM, PSA and Renault. The plant has recently extended its production space (from 2000 to 4000 square metres), hired new employees and brought in production lines. Krosno In September 1997 Delphi acquired nearly 75% of the shares of the Fabryka Amortyzatorow S.A . (F. A. Krosno). Now called Delphi Krosno SA, it is the leading supplier of shock absorbers in central and eastern Europe. The present OEM clients are: Fiat, Opel Suzuki, Daewoo and PSA Peugeot-Citroen, and the plant also plays a significant role in the aftermarket (both domestic and eastern European: Russia, Ukraine). Delphi Krosno SA employs more than 1,100 people. Apart from shock absorbers, the plant also manufactures a large range of gas springs, ball joints and steering system parts. Technical Center in Krakow Delphi opened its Technical Center in Krakow in July 2000 with around a 350 employee capacity planned. Today TCK employs more than 280 engineers, technicians, administration and support personnel, most of whom are locally educated. This was the first R&D centre opened by an international supplier in Poland. Engineers at TCK support Delphi European and worldwide customers including: PSA Peugeot Citroen (first PSA contract with external supplier for rear shock absorbers), BMW, General Motors, Ford and DaimlerChrysler. Most recently, Citroen C3 shock absorbers were designed at Krakow and the facility is to become the supplier’s world absorber technology development centre in the future. |
Manufacturing activities in Poland of the top 201 global suppliers: | |
Delphi | Wire harnesses; fuel vapour canisters; steering systems; heat exchangers; switches; shock absorbers; also has a technical centre located in Poland |
Robert Bosch | Automotive technology; car multimedia; thermotechnology; components for braking systems |
Visteon | Powertrain and chassis |
Denso | Small motors; heaters; cockpit modules |
Lear | Six facilities in Poland |
Johnson Controls | – |
Magna | Two manufacturing centres in Poland |
Aisin Seiki | – |
Faurecia | Seat slides and frames, dashboards and door panels; modules and systems |
TRW Automotive | Airbag plant; seatbelt plant; braking plant; steering wheel plant |
Valeo | Electrical systems; electronics and connective systems; engine cooling; starters and alternators; wiper systems; lighting systems (2004) |
Siemens VDO | Car communication |
Dana | Automotive oil and air filters |
ZF | – |
ThyssenKrupp | Five facilities in Poland |
ArvinMeritor | – |
Yazaki | – |
Continental | – |
DuPont | – |
GKN | Manufacture and assembly of constant velocity ball joints, bi-pod joints and shafts |
Source: SupplierBusiness.com Note: 1Top 20 suppliers ranked on 2002 global OEM automotive component sales, as listed in Automotive News 2003 Global market data book |
There is a very slow adaptation to some regulations and rules of Polish law to European Union standards, there are a lot offormalities and procedures to implement different kinds of activities, and there are higher income taxes and other so-called local taxes versus Slovakia, for example.”
In August 2003 Johann Berger, a manufacturer of airbags and seatbelts opened a new factory in Poland and plans increased investments. At the same time Poznan-based Centra announced it had won a contract to supply batteries to Ford in the UK and Belgium. Centra will also supply batteries to Fiat for the Panda. In May 2003 Bosch invested €26m in the construction of a new brake system factory in Mirkow near Wroclaw, south west Poland. The plant will employ 500 people and will supply brakes, brake master cylinders and other brake products to car plants in Poland and Europe including Fiat plants. In March 2003 Valeo announced it was setting up a new lighting plant in southern Poland. Employment at the plant, which should open in 2004, could reach 600. The new investment brings Valeo’s total investment in Poland up to €100m. In January 2003 Autoliv announced it had opened a new seatbelt plant in Poland. Other foreign companies to have invested in Poland in the last two years include Delphi, Tibermec, Gestamp, SNOM, Bridgestone, Brembo, Faurecia, Thule, Huf, NGK, Ronal and Leoni. In March 2003 the Polish firm Inter Groclin won two contracts to supply car seat covers for new models from Porsche and Faurecia, a supplier of parts for Renault, Citroën, Peugeot, and Toyota. The total value of the contracts is ZL180m (€41.0m, 31 March 2003). Fiat-GM Powertrain B.V., a manufacturer of diesel engines, made the largest foreign investment in Poland in the first half of 2003, investing capital of US$432.2m (€378.0m, 30 June 2003). In August 2003, the joint-venture company of Fiat and GM was able to employ 100 more workers due to an increase in orders for the turbo diesel 1.3 Multijet 16v engines, which are primarily installed in Fiat and Opel cars.
The majority of international suppliers based in Poland have indicated to SupplierBusiness.com that they have not been greatly affected by the difficulties at Daewoo and Fiat – a large slice of their products are exported and only a small percentage is sold to domestic customers. For example, according to Birgit Albrecht when talking about the problems at Daewoo and Fiat, “our investments have not been affected very much. Fiat and Daewoo import complete engines and only have their assembly plants in Poland. Most deliveries from Mahle Krotszyn S.A. are OE exports.” Steve Gaut, spokesperson forDelphi, told SupplierBusiness.com that currently 80% of Delphi’s more than €330m annual sales are shipped to other European markets for assembly on customers’ vehicles. Stanislaw Kostka, general manager of Autoliv Poland summed up what many suppliers were saying, “I think that the pressure from OEM companies to decrease the prices of our products will force us to make further investments in low-cost countries such as Poland, but still the focus will be on capacity for exports, because the Polish market in the near future will not be big enough for the scale of our operation here.”
It is also possible for some Poland-based suppliers to still benefit from new OEM investments outside Poland. For example the Toyota and PSA Peugeot-Citroën joint investment in the Czech Republic has resulted in Toyota building a plant in Poland for the manufacture of engines andtransmissions. The joint venture also signed contracts with some of the two OEMs’ existing suppliers in Poland, such as TRW Automotive. PSA Peugeot-Citroën has not announced any similar plans to source supplies for its new Slovakia-based plant from Poland, but this cannot be ruled out in the medium term.
It is also worth noting that there are several suppliers that have invested in Poland that have had no problems with either the investment process or the level of infrastructure within the country. Lynette Jackson, spokesperson for TRW Automotive, points out, “TRW Automotive has five plants in Poland, employing more than 3,500 people. There are two plants in Czestochowa – an airbag and a seatbelt plant, a braking plant in Gliwice, a steering plant in Czechowice-Dziedzice, and a steering wheel plant in Pruskow.” With regard to support from Polish authorities she notes, “TRW’s Polish businesses have benefited from a variety of measures of governmental support including a ‘postgraduate training programme’ at our Czechwice-Dziedzice plant, which is supported by local employment agencies; and government grants for our Czestochowa plants for the employment of unemployed people; and support for the opening of our Gliwice business in a special economic zone.”
POLAND Sources: The World Factbook 2003; WMRC |
It is clear that the unfavourable economic climate of recent years and lack of attention to infrastructure and needs of potential investors have caused many companies to look elsewhere for investment locations in recent years. But the tide could be turning. Poland has recognised its problems and is addressing them and the new vehicle market is showing signs of life ahead of Poland’s accession to the EU. It is likely that investors could soon be tempted back to the country, especially if the bid to attract Hyundai is successful. Delphi’s example, which is outlined in the case study, illustrates how the country can become a pivotal location for suppliers in both engineering/product development and manufacturing.
QUESTIONS & ANSWERS – Steve Gaut Communications Director, Delphi Europe, Middle East and Africa
|
|
Why did Delphi decide to invest in Poland? Was it easy to invest in Poland, what assistance, if any, did you receive? What are the advantages and disadvantages of operating in Poland? If you have facilities in Slovakia/Hungary/Czech Republic how do these investments compare? |
operations, but most engineering and component manufacturing is completed outside the country. Our operations in the other eastern European countries mentioned above are much newer and we have just begun the journey of developing local suppliers and internal management talent from within the company. In Poland, we have almost 10 years of experience with employees, customers, suppliers and officials within the country. How have you been affected by the downturn in the Polish auto industry? How have the problems at Fiat and with Daewoo-FSO affected you? How do you see the future of the auto industry in Poland, will it pick up or decline further? Any other developments? |