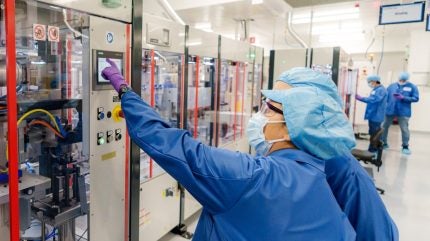
US supermaterials application company Lyten has said it is consistently surpassing 90 percent yield from its automated battery production line.
This, it says, confirms the manufacturability of its lithium-sulphur battery utilising a sulphur cathode and lithium metal anode.
Dan Cook, Lyten CEO and Co-Founder said: “Lyten now has demonstrated that lithium-sulphur can be built in standard cylindrical and pouch formats, can be scaled to automated manufacturing, and can be done on the same equipment and processes already being used around the globe to manufacture legacy lithium-ion.”
Lyten says it is executing engineering and design, procuring equipment, and evaluating locations to rapidly scale-up lithium-sulphur manufacturing to meet growing interest from EV, trucking, space, aerospace, and government customers.
Its lithium-sulphur battery contains no nickel, cobalt, manganese, or graphite in the cathode and anode, enabling an entirely locally sourced and manufactured battery.
It expects to achieve 98%+ yields at scale and will begin delivering commercial lithium-sulphur cells for non-EV customers in aerospace and government applications in 2024 from its San Jose pilot production facility.
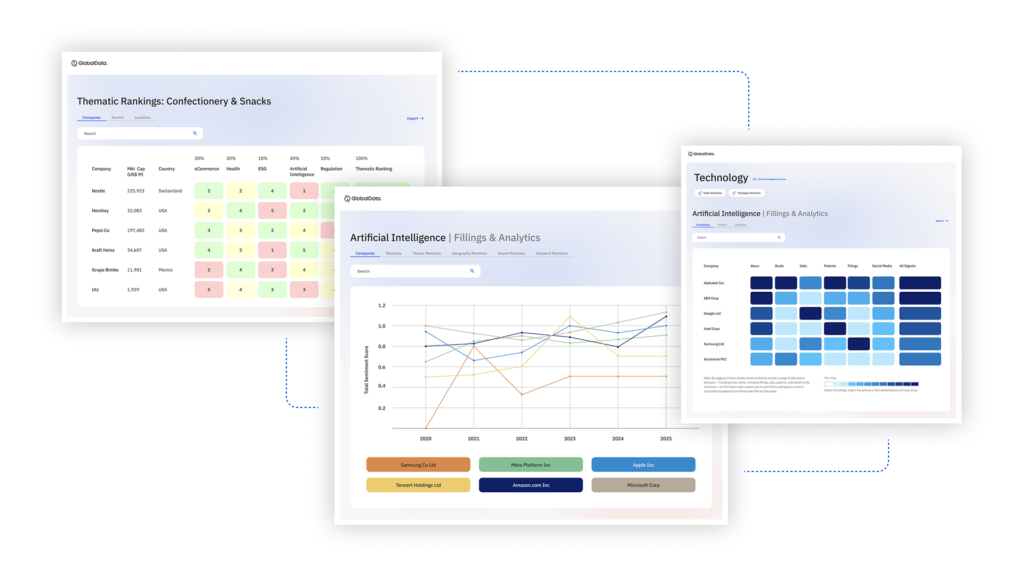
US Tariffs are shifting - will you react or anticipate?
Don’t let policy changes catch you off guard. Stay proactive with real-time data and expert analysis.
By GlobalDataCelina Mikolajczak, Chief Battery Technology Officer at Lyten said: “To achieve mass market adoption, lithium-sulphur must be able to be manufactured at enormous scale and at a price immediately on par or better than today’s already scaled up lithium-ion batteries.”