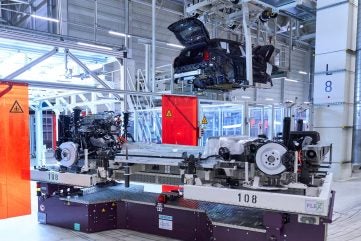
Four months after launching production of combustion variants of the Mini Countryman, the electric version is now being built at the BMW plant in Leipzig (eastern Germany) as well.
Effectively, it replaces the now axed i3, and the plant is making four models, three drive types and two brands on a single production line (the others are 1 and 2 Series models including a PHEV).
To boost capacity 100k to 350,000 units a year the plant has been continuously upgraded since 2018, with additions and upgrades to the body shop, paint shop, assembly and logistics.
“The group has invested around EUR1.6bn to produce additional vehicles and electric components,” said plant director Petra Peterhaensel.
Countryman output will rise to 500 units a day this year alongside 800 BMW models.
The different drive units are also all produced on one line in final assembly ahead of installation.
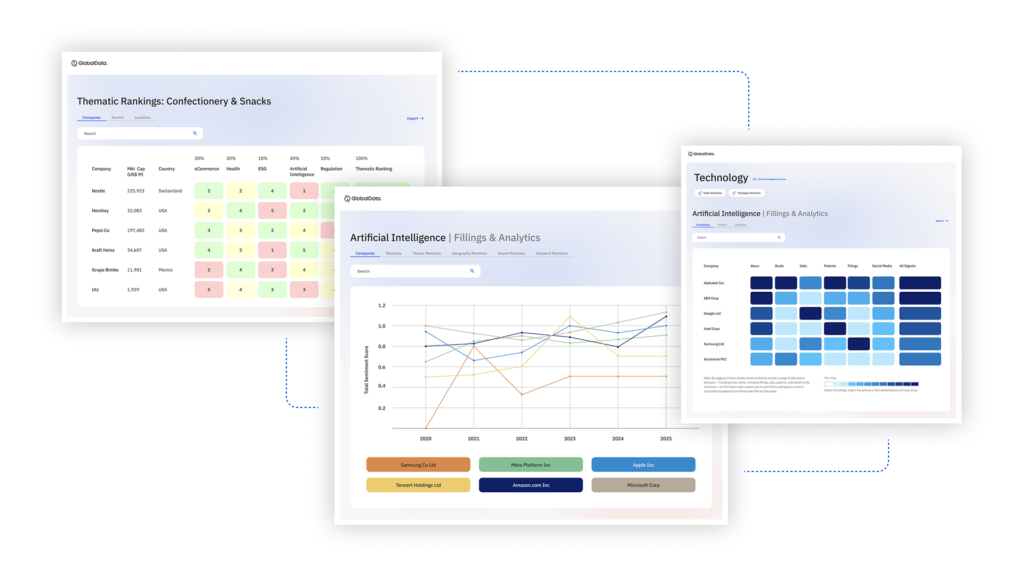
US Tariffs are shifting - will you react or anticipate?
Don’t let policy changes catch you off guard. Stay proactive with real-time data and expert analysis.
By GlobalDataE-drives, transmissions and control electronics are connected in the plant and a new line was required only for control electronics.
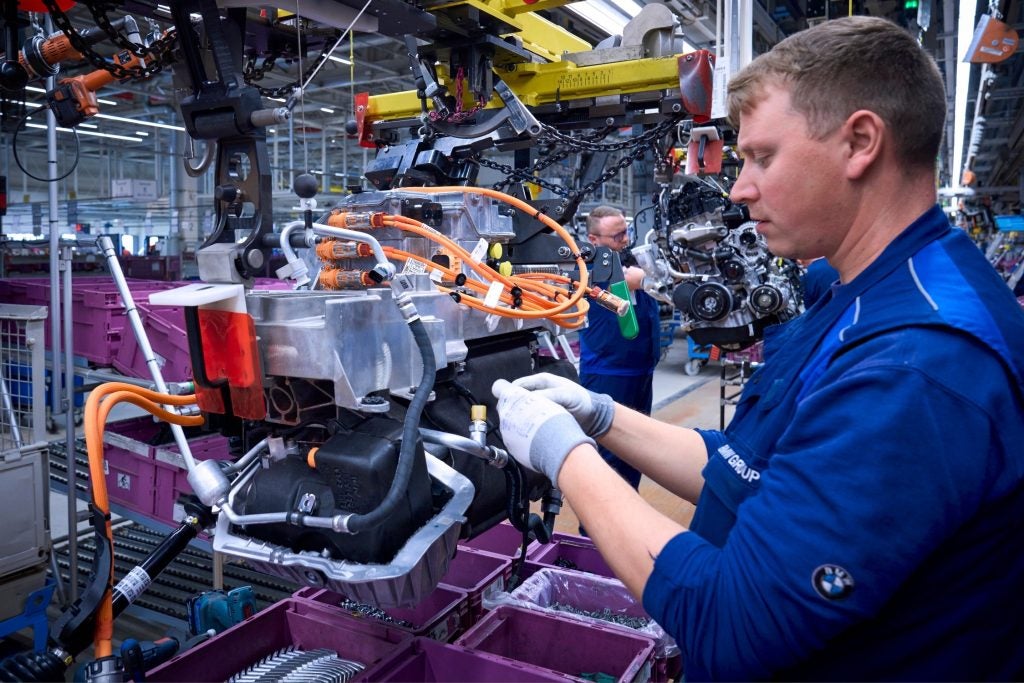
Leipzig is adding 900 extra workers for vehicle production and will have 7,000 people by the end of the year. Working hours are being adjusted with assembly night shift starting for the first time in September, taking the plant to three shifts.
The green field plant, known for its bodies in white trundling through above the main reception area, opened in 2005 with 2,600 employees in production.
The three stages of high voltage battery production are all now done at Leipzig with five cell coating, three module production and two HV battery production lines.
The recently added e-component unit currently employs 1,000.
For HV batteries, space previously used for i3 and i8 build have been converted and new buildings added including a new 61,000 sq m hall with two lines producing up to 300,000 sets a year.
The group has invested EUR900m in e-component production there.
The Countryman’s optional contrast roof is painted using a new overspray free method which makes it easier to paint in multiple colours as masking is no longer required. Air exhausted from the paint booth requires less cleansing and less conditioned air, reducing energy use.
Five burners used to dry the roof paint are now ‘bivalent’ and can run on hydrogen or methane gas and switch between the two while in use.
Other paintshop burners will also gradually switch to bivalent as the plant moves to replacing fossil fuels with ‘green’ hydrogen.
A regional hydrogen grid is currently in planning stages.