It takes a little while to notice and then you realise something is different about Toyota’s Miyata plant in Kyushu, Japan: it’s quieter, much like the Lexus models it builds.
Travel up and down the assembly lines and there’s the same busy pace as in any modern car assembly plant – line workers hurrying back and forth and up and down the conveyor attaching parts to cars, co-workers fetching and placing those parts handy line-side, and a busy end-of-line team making sure all the right bits are on the right car, and everything’s properly installed and working just right.
Then you notice the absence of the ‘eeeeeeyeeewwww’ sound of pneumatic hand tools – everything that tightens a bolt, nut or screw in this plant is electrically operated. More precise, more easily computer-controlled, and much, much easier on the ear, spokesmen proudly told a visiting group of European journalists on Monday, therefore nicer for the workers.
In fact, the plant operates under the theme ‘clean and quiet’ and it is immaculate both inside and out.
The term ‘Toyota Motor Kyushu’ actually encompasses multiple plants: Miyata with both No.1 and No.2 body weld, paint, and assembly units fed by a common stamping plant plus plastics, suspension and fuel tank units and a hybrid component sub-assembly facility on a site two kilometres long and 850m wide; supported by Kanda, about 30 minutes drive away, which makes engines.
How well do you really know your competitors?
Access the most comprehensive Company Profiles on the market, powered by GlobalData. Save hours of research. Gain competitive edge.
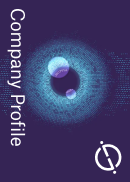
Thank you!
Your download email will arrive shortly
Not ready to buy yet? Download a free sample
We are confident about the unique quality of our Company Profiles. However, we want you to make the most beneficial decision for your business, so we offer a free sample that you can download by submitting the below form
By GlobalDataThe No.1 weld/paint/assembly plants date back to 1992 when the Toyota Mark II (exported as the Cressida) assembly began; the smaller No.2 facilities opened in 2006 with production of the latest Lexus ES, a Camry-based luxury sedan sold mostly in North America. It also does the entry-level Lexus IS line while No.1 builds the Toyota Harrier/Lexus RX models in both petrol and hybrid forms and the export Highlander petrol and hybrid derivatives of the Toyota Kluger SUV.
Outputs are comparable – No.1 puts out just over 1,000 cars a day and No.2 around 850 – both on two-shift operation with workers averaging 45 hours a week. There’s 8,500 staff – 5,600 on the Toyota payroll and 2,900 with outsourcing suppliers.
No.2, opened only last year, is about half the size of the No.1 original, thanks to continuous process improvements since No.1 was laid out in the early 90s. Two examples: car bodies go through paint dry ovens sideways in No.2, shortening the line length, and fewer pre-sequenced parts are kept line-side, reducing the space taken up by the two assembly lines.
The No.2 plant bristles with technology innovations. Toyota’s policy is use robots where it makes sense in repetitive tasks and to assist workers with heavy jobs and make best use of people for the really dextrous craftsmanship. So robots do the flat panel paint spraying and well-trained people paint the door openings and boot and under-bonnet areas.
Wireless communications between equipment tell workers exactly how many of each part to take from a line-side station to install on the vehicle model approaching. The worker sets a counter to zero as he (or one of the very few female line workers) takes the last nut and a sequencer/replenisher, notified wirelessly, races to re-stock the bins for the next few cars.
Over at final set and test, a computer-controlled headlamp beam aimer scans the lights and sets an electric wrench – the operator simply applies it to each headlight adjuster screw and the electronics spin it just the right number of turns.
About 90% of the combined Kyushu plants’ output is exported – 65% to North America, 10% to Europe (a RHD IS for the UK is a rare sight on the line), 10% to Asia and 10% for the domestic market.
It takes just 19 hours from weld to final inspection to make a car here, yet plant managers – surprisingly candid for Japanese executives – admit there is room for improvement – in No.2 30% of vehicles assembled require some sort of rework at the end of the line, mostly paint, which is to an exceptionally high standard on the Lexus models. Plant No.1 is running at 10%, so its on-site ‘rival’ is hard at work narrowing the gap.
Graeme Roberts