Nissan Motor has opened a Field Quality Centre (FQC) in Japan in an effort to combat defects and problems with its vehicles. The centre will focus on what the company calls the “vehicle quality enhancement processes”.
In a statement, the automaker said the Centre would conduct field quality investigation analysis (FQIA) to identify the root cause and solutions to vehicle problems.
“The FQC serves as a central collection base for incident parts received directly from the dealerships, where the parts are then subjected to detailed analysis. The FQC is equipped with testing equipment and measuring instruments that can replicate actual field conditions in order to define the root cause of the problem. This allows the FQC to identify the customer’s vehicle problem earlier and find a solution more quickly, in order to implement the right countermeasures to the products,” Nissan said.
The FQC will work jointly with the product development and manufacturing engineer teams in order to facilitate a continuous “quality improvement” process. The FQC findings are fed back to the Nissan Technical Centre (NTC), where future vehicles are developed.
Nissan senior vice president, total customer satisfaction, Kazumasa Katoh said: “The FQC will boost Nissan’s ability to deliver higher customer satisfaction. At the FQC, we will work to improve the quality of Nissan’s vehicles from every aspect in accordance with the Nissan product quality policy.”
Nissan said it had invested JPY900m ($US7.29m) in the FQC, which occupies a 4,400m2 area, within the Nissan Technical Centre campus. Approximately 210 employees will be based there. Construction and installation of test equipment were completed in June.
How well do you really know your competitors?
Access the most comprehensive Company Profiles on the market, powered by GlobalData. Save hours of research. Gain competitive edge.
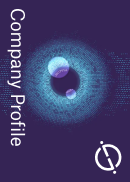
Thank you!
Your download email will arrive shortly
Not ready to buy yet? Download a free sample
We are confident about the unique quality of our Company Profiles. However, we want you to make the most beneficial decision for your business, so we offer a free sample that you can download by submitting the below form
By GlobalDataThe FQC facility, Nissan said, is able to process four times the quantity of parts investigation compared to its previous capacity. Prior to FQC, Nissan’s field quality improvement team was located at the Shinkoyasu operations centre in Yokohama.
Globally, Nissan has had three other FQC facilities in operation since 2006 – two in the US at Smyrna and Farmington Hills and another in Cranfield, UK, for Europe. The FQC in Atsugi will serve the Japanese domestic market and about 140 countries in what it calls the ‘general overseas market’.