Denso Corporation has developed four new components for hybrid vehicles: a control computer; a battery monitoring unit; a DC-DC converter, and an electric compressor for air conditioning systems. All are smaller and lighter than conventional components, but still able to meet the needs of today’s larger hybrid vehicles.
In March, the Toyota Harrier and Kluger hybrid vehicles with these components installed were launched in Japan. This month, the components will be introduced in the United States on the equivalent Lexus RX400h and Toyota Highlander hybrids.
The hybrid control computer, developed jointly with Toyota Motor Corporation, integrates such control functions as hybrid system control, engine control, and battery control into one unit. The hybrid control computer enables a significant size reduction of the control units.
The new battery monitoring unit monitors the main battery’s condition including voltage, current and temperature, which traditionally were performed by the battery ECU. The battery monitoring unit was designed separately from the hybrid control computer, because the battery monitoring unit needs to be installed close to the main battery.
Denso’s newly developed DC-DC converter is approximately 10% smaller than a conventional DC-DC converter, but its increased output current from 100 amperes to 120 amperes is able to respond to the electric power needs of larger vehicles. The increased output current was achieved by adopting a new circuit control technology to reduce energy loss in the DC-DC converter. To handle the increased output current, the converter’s power elements were improved by changing the mounting method from soldering to welding. Customised integrated circuits reduce the area of the converter’s circuit board by approximately 40%, contributing to the 10% converter size reduction.
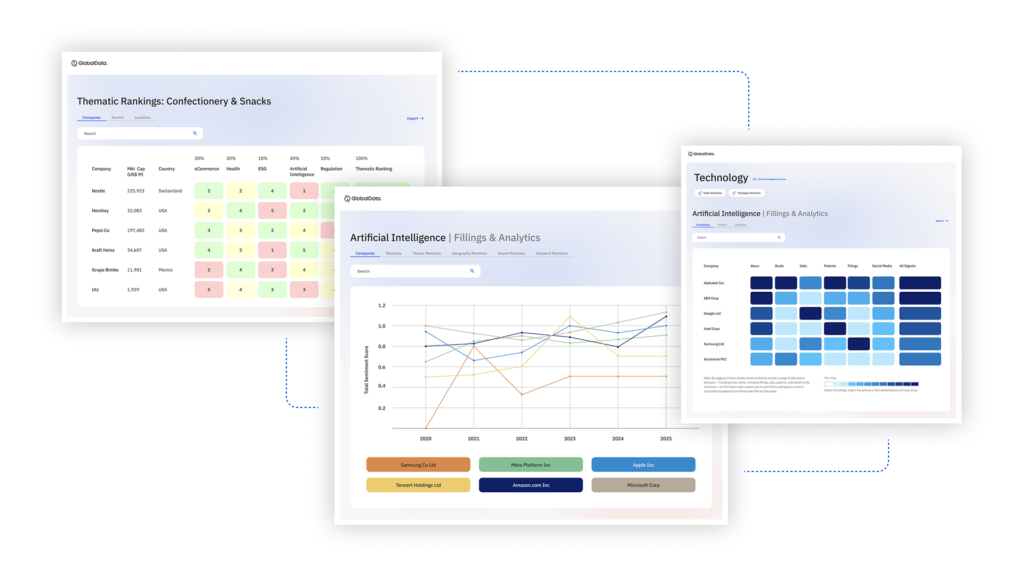
US Tariffs are shifting - will you react or anticipate?
Don’t let policy changes catch you off guard. Stay proactive with real-time data and expert analysis.
By GlobalDataThe electric compressor, jointly developed with Toyota Industries Corporation, is the first in the world to incorporate an inverter that drives the built-in motor. This structure reduces the compressor size by approximately 60% compared with a conventional electric compressor and inverter (when they are assumed to provide the same output). Denso miniaturised the inverter by using simplified circuits and a higher-density mounting with three-dimensional wirings.
It is difficult to integrate the conventional compressor and inverter, because the conventional inverter is cooled by the engine’s coolant system. To solve this problem, a new cooling method using air conditioning refrigerant in the compressor was developed, allowing the integration of the electric compressor and the inverter. The unique segment conductor wiring method, which was developed for alternators in 2000, reduced the size of the built-in motor.