Maruti Udyog, the Indian manufacturer of Suzuki-designed car, on Monday said that total energy consumption per vehicle at its Gurgaon factory has been reduced 26% over the last six years.
In a statement issued on the eve of World Environment Day (June 5), the company said that in recent years, several innovative measures have enabled it to “drastically” reduce consumption of power and water and waste generated in car manufacturing.
Power consumption has come down by 31% while water consumption per vehicle has dropped by 63% over the last six years. Landfill waste has come down by 67% over this period.
CO2 emissions per vehicle (produced during manufacturing) have also been successfully brought down by over 39% in the last five years.
The automaker said benefits to the overall value chain are much higher, as it has worked with its suppliers implement the best environment practices at their facilities as well.
How well do you really know your competitors?
Access the most comprehensive Company Profiles on the market, powered by GlobalData. Save hours of research. Gain competitive edge.
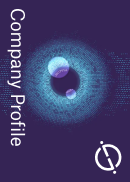
Thank you!
Your download email will arrive shortly
Not ready to buy yet? Download a free sample
We are confident about the unique quality of our Company Profiles. However, we want you to make the most beneficial decision for your business, so we offer a free sample that you can download by submitting the below form
By GlobalDataMaruti Udyog said it has based its operations on the principle of “smaller, fewer lighter, shorter and neater”, a value system shared with parent company, Suzuki Motor Corporation in Japan, and which defines the environment-friendly initiatives at Maruti.
While a full department co-ordinates environment initiatives, employees and partners contribute in promoting the “three Rs”: reduce, recycle and reuse.
In the air conditioning plant, water use has been eliminated by introducing air-cooled condensers and closed cycle cooling towers in compressed air plant.
Other water use has been reduced by a ‘just in time’ supply using sensors on various water hoses, toilets and wash areas to bring down consumption.
To reduce consumption of raw paint, multi axis painting robots have been introduced in the paint shop to increase the efficiency of paint transfer and thereby reduce consumption. This also reduces paint sludge generated by the process.
Maruti said a lot of energy is lost because of over-sizing of equipment so it operates a ‘rightsize’ policy for machinery selection.
Energy consumption is also reduced by using renewable or free energy such as natural light – the factory and office buildings have been designed so that abundant natural light is available throughout the day.
Solar lamps and heaters help power conservation along with natural ventilators that use wind instead of electricity to keep rooms cool.
Other measures include increased use of energy efficient lighting systems; common pumps and automated switch boards for shop floor and emergency lights.
The installation of “noise curtains” in certain areas and enclosing compressors minimises noise pollution, providing better working conditions for employees in those areas.
“While specific environment friendly initiatives have helped reduce resource use, the overall improvement in the company’s manufacturing process has also contributed,” Maruti said.
“Improved layouts, better efficiency on the shop floor, reduction in wastages, focus on quality and cost have all had a beneficial impact on resource use as well.”
The automaker is also reusing waste gases, generated during power generation, in the car manufacturing process.
It has installed a compressor, powered by a steam turbine, which compresses high-pressure steam to optimum levels required for manufacturing.
This is has eliminated the requirement of an electrical motor with savings of about 4,225 megawatt hours a year.
Sheet metal scrap from the press shop is used to make smaller components, sludge from the sewage treatment plant sludge is reused in horticulture, reducing landfill waste by about 250 tons a year and wooden and cardboard packaging material is reused.
Initiatives like soak pits, recharging shafts and water lagoons help in recharging up to 55% of the annual average rainfall into the ground.
An effluent treatment plant uses ‘tertiary treatment’ and ‘Reverse Osmosis’ technology to recycle water.
For materials that cannot be recycled, incinerators burn industrial wastes at high temperatures with minimal pollution and specially-designed landfills store hazardous waste in a manner that avoids leaks or chemicals mixing with each other.
The new facility at Manesar (opened last February 2007) was designed to be as environment-friendly as possible and features translucent polycarbonate side wall and roof panels that let in abundant natural light to reduce the consumption of electricity while blocking harmful UV rays.
The plant also has an advanced waste management module that burns wasyerat a very high temperature to convert harmful chemicals into harmless gases, and independent water management and treatment plants.