Automotive interiors supplier International Automotive Components (IAC) says it has launched its FibreFrame environmentally-sustainable and lightweight, natural fibre sunroof frame on the 2017 Mercedes-Benz E-Class. The proprietary innovation is made of 70% renewable raw material content and provides up to 50% in weight saving compared to conventional metal-reinforced steel sunroof frames. The new Mercedes-Benz E-Class going on sale this week marks the mass production debut of IAC’s latest proprietary interior solution.
“Sun and panoramic roofs are increasingly popular across all vehicle sizes and segments,” said IAC Director of advanced engineering Fritz Schweindl, located at the company’s Ebersberg, Bavaria, technology centre. “This market trend inspired IAC to develop stiff and lightweight concepts, which help realise different fixation concepts on the car body, the sun roof or the panoramic roof module. Within its strategy of viable innovation, IAC leveraged its integrated material and process know-how to provide our OEM customers with significant weight savings, a lower carbon footprint for their vehicles and a more efficient production process.”
IAC claims weight savings of 50%
IAC says its FibreFrame replaces the sunroof’s metal reinforcement frame with a lighter frame employing strong, natural fibres using a new raw material comprised of 70% renewable content. This lightweight solution is reinforced using IAC’s EcoMat natural fibre-based semi-finished material, which was especially developed for this application. The fibre mat is moulded with a thermoset binder and is manufactured in-house by IAC in a hot moulding process.
“In the specification of the IAC EcoMat fibre mat, as well as in terms of tooling technology and production process of this innovation, we were able to take advantage of more than 20 years of experience working with natural-fibre-reinforced materials in automotive interiors,” said Schweindl. “By manufacturing this product in-house in our head-liner plant, we follow our strategy and expansion of vertical integration of our interior systems. Thanks to our global manufacturing footprint and standardised processes, we are now able to adapt IAC FibreFrame to customer needs and supply it around the world.”
The new product has high stiffness for improved structural rigidity and enables up to 50% in weight saving compared with conventional steel frames, it is claimed. Compared to conventional thermoplastic frames, FibreFrame also prevents warpage after climate testing. In addition, moulding tooling concepts for IAC’s FibreFrame have much shorter lead times than conventional steel moulding tools.
How well do you really know your competitors?
Access the most comprehensive Company Profiles on the market, powered by GlobalData. Save hours of research. Gain competitive edge.
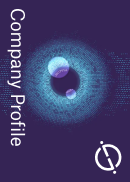
Thank you!
Your download email will arrive shortly
Not ready to buy yet? Download a free sample
We are confident about the unique quality of our Company Profiles. However, we want you to make the most beneficial decision for your business, so we offer a free sample that you can download by submitting the below form
By GlobalDataFibreFrame started production in November 2015 at IAC’s centre of excellence for overhead products in Prestice, Czech Republic, to support the Mercedes-Benz E-Class launch. The company also produces the headliner, the outer-rear wheel house liner, inner wheel house cover and rear seat cover for the vehicle.