Ford says a fully automated process using furnaces, robots and lasers to craft car parts with boron steel is strengthening the new Ford Focus, helping it earn a maximum five-star Euro NCAP safety rating.
The first fully automated hot-forming process shapes and cuts parts of the car – which are integral to protecting drivers and passengers – using giant furnaces, robots and 3,000° C lasers.
“We are building on techniques used to strengthen steel for thousands of years, incorporating modern materials and automation to speed and refine the hot-forming process,” said Dale Wishnousky, vice president, Manufacturing, Ford of Europe. “The resulting boron steel safety cell helps to make the all-new Focus one of our safest vehicles ever.”
The hot-forming line – fully integrated within the company’s Saarlouis Vehicle Assembly Plant in Germany – was built as part of a recent EUR600m investment in the Saarlouis facility.
Ford says the new Focus makes extensive use of boron steel – the strongest steel used in the auto industry – within the car’s safety cell. This helps to create a survival space in the event of an accident. In addition, the use of boron, also found in skyscrapers, helps the new model to achieve a 40 per cent improvement in the car’s capability to withstand head-on crashes.
Hot-formed steel pieces are subjected to temperatures of up to 930° C; unloaded by robots into a hydraulic press that has a closing force up to 1,150 tonnes; and then shaped and cooled in just three seconds.
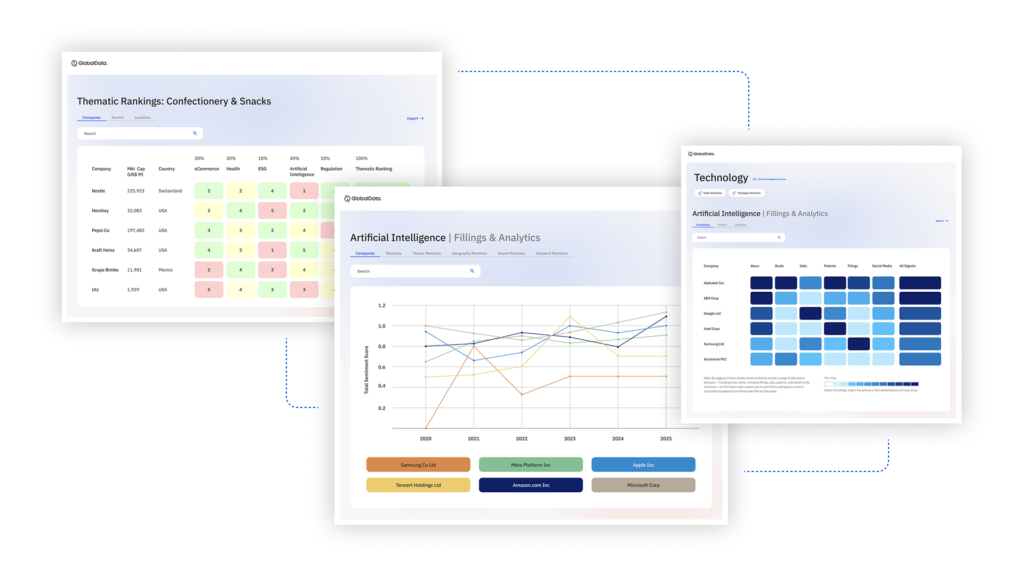
US Tariffs are shifting - will you react or anticipate?
Don’t let policy changes catch you off guard. Stay proactive with real-time data and expert analysis.
By GlobalDataFord has also produced a promo video that is worth a view: