Henkel and Fiat Chrysler Automobiles (FCA) have cooperated in the development of new treatment processes that boost strategies for reducing weight and were applied to the latest version of the Alfa Romeo Giulia.
FCA and Henkel worked together for almost three years to develop and tailor Henkel materials and systems for FCA's specific needs.
Henkel says that lighter car bodies manufactured from mixed steel and lighter metals like aluminium are requiring new approaches to surface treatments. The new processes are providing car makers not only with the opportunity to use lighter metal structures, but they are themselves using materials that are lighter than previous generations of treatment products. Processes and procedures are changing significantly as new materials and application technologies are launched.
The new Giulia has a body that is 90 kg lighter than a comparable all-steel body, Henkel says. This was achieved by the use of light metals in combination with new process materials and application technologies. To reduce weight and improve performance, FCA is using aluminium to account for 45% of car body weight. It has adopted a new acoustic package to enhance passenger comfort while saving more weight.
Pretreatment processes
The Bonderite two-step metal pretreatment process was developed by Henkel for multi-metal bodies with very high aluminium contents (up to 80%), providing superior corrosion performance while reducing investment- and processing costs. The dip-coating process uses zinc phosphate in the first step to treat the steel, followed by aluminium treatment in the post rinse.
How well do you really know your competitors?
Access the most comprehensive Company Profiles on the market, powered by GlobalData. Save hours of research. Gain competitive edge.
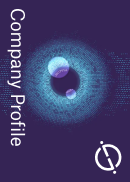
Thank you!
Your download email will arrive shortly
Not ready to buy yet? Download a free sample
We are confident about the unique quality of our Company Profiles. However, we want you to make the most beneficial decision for your business, so we offer a free sample that you can download by submitting the below form
By GlobalData"Aluminum can be eaten up by the acids normally used to phosphate steel, so there is a need to find a balance in the treatment process," says Manfred Holzmueller, Sales Director Transplant OEM Business at Henkel.
"Corrosion performance is equal to tricationic Zn-Phosphate, but the Bonderite process generates 30 – 50% less sludge, consumes fewer chemicals, and creates less surface roughness that demands rework. Lower operating temperature also saves energy."
Keeping the noise out
The Alfa Romeo Giulia also benefits from Henkel Teroson high expansion pillar fillers. These are moldings made from a special foamable elastomer that are inserted into cavities in the car body – in the A-pillars for example – during assembly in the body shop. When the body passes through the e-coat oven, the high temperatures cause the moldings to expand to up to ten times their original volume, completely filling and sealing the cavity. This prevents any air entering into the cavity while the vehicle is in motion, and eliminates any wind noise that would otherwise result.
A second Teroson product applied to the car body, Teroson AL7154, is a liquid spray-applied acrylic waterborne sound deadener (LASD) developed by Henkel to reduce noise generation in the passenger compartment caused by vibration of the body shell. During extensive tests at FCA, this product showed by far the highest loss factor (a measure of the damping properties) of all candidate materials. The total weight of Teroson AL7154 on the Giulia is over 10% less than standard bitumen pads that would have provided a lower level of acoustic insulation. A further advantage of this new LASD is that it can be applied robotically, without the need for any human intervention at all. This has important implications, not only in terms of costs, but also in terms of health and safety.
The Alfa Romeo Giulia was the first new car to benefit from the use of Teroson AL7154. Two other vehicles made by FCA on the same line in Cassino, Italy – the company's first SUV, the Stelvio, as well as the existing Giulietta (in a running change) – have also since adopted the product.
Also developed for fully robotic application on the Giulia is Teroson PV3414, a new interior and exterior seam sealer concept that replaces two different sealers – one for exterior seams, one for interiors, and both applied manually. It enables higher application speed, better sealing, better appearance, less dripping and significantly less manual touch-up work. Alfa Romeo is also the first adopter of this system, which is based on a PVC plastisol.
According to Holzmueller: "The new Cassino paint shop is providing FCA with a step-change in quality for its vehicles. The company now uses the most modern paint shop technology for the production of high class vehicles. We believe that the innovative spirit at Henkel is clearly on show in the new Giulia. We are facilitating weight reduction through the use of lighter metals, and we are helping our customer cut costs and improve sustainability by using fully automated application systems and reducing waste by avoiding sludge and overspray in its the processes.
"Furthermore, we are reducing the need for cleaning and maintenance. FCA has taken a major step forward with the simultaneous implementation of numerous new technologies and processes for the new Alfa Romeo Giulia. Very close and intensive cooperation between our two companies was essential, and I am happy that it has resulted in such a beautiful new car!"