GKN Driveline’s new lightweight VL3 constant velocity joint (CV joint) system has launched in its second application on the all-new BMW 5 Series. The VL3 joint makes the driveline more efficient, with measurably reduced CO2 emissions – an improvement in current applications.
BMW Group and GKN Driveline
GKN has held patents on the VL series of CV joints for more than 50 years, and the last significant update to the design was in 2001 when the VLi joint appeared in the BMW 7 Series. It is fitting that the new design, VL3, also had its debut on the contemporary 7 Series.
The joint was launched last year on the new model of BMW’s luxury saloon. Working to a schedule of just 18 months, GKN Driveline delivered the new benchmark in lightweight, high-performance sideshaft systems to BMW Group in the VL3 system.
Stronger and more refined
At the heart of the advanced VL3 design is a brand new S-shape track in the housing, which changes the way that the ball bearings move around. Employing GKN’s Countertrack technology, the balls are given a wider range of movement, which helps to balance the forces in the joint by distributing the torque evenly between the bearings. In turn, this bolsters the strength of the cage and improves refinement in the joint movement.
Design flexibility for the automaker
Efficiency is improved by using eight ball bearings instead of six. Using more bearings results in a lower load per ball, in turn enabling each ball to be smaller in diameter – thus reducing the diameter of the packaging with no detriment to the torque capacity of the joint. Alternatively, by keeping the VL3’s eight balls of the same size as the six in the VLi system, higher loads can be transmitted through the joint, The design is flexible, which means that automakers have the choice of reducing packaging size, increasing torque capacity, or a mix of both.
See Also:
Grease lightening
The third key design innovation of the new VL3 joint is the diaphragm boot, which delivers a best-in-class sealing system. The diaphragm design replaces the conventional cap-and-boot solution typical for VL series joints, and instead uses a shallow, one-piece contoured cover. Shrinking the size of the cover significantly reduces the volume of grease needed to pack the joint. This innovative joint sealing method reduces the weight and cost of the joint, as well as the space needed to package it – giving more freedom to the design of the surrounding suspension components.
How well do you really know your competitors?
Access the most comprehensive Company Profiles on the market, powered by GlobalData. Save hours of research. Gain competitive edge.
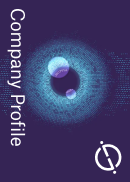
Thank you!
Your download email will arrive shortly
Not ready to buy yet? Download a free sample
We are confident about the unique quality of our Company Profiles. However, we want you to make the most beneficial decision for your business, so we offer a free sample that you can download by submitting the below form
By GlobalDataUwe Paksa, vice president Engineering Constant Velocity Joints, said: “GKN has pioneered the development of CV joints for more than 60 years, and the latest innovations in the VL3 offer improvements in every area of importance for automakers. We have developed a CVJ that is lighter, more efficient, stronger, delivers more torque and is more compact.”