GKN Driveline says it has created a new lightweight, high-speed propshaft joint for the all-new Audi Q5. It will be manufactured in Mexico to support Audi's factory there.
The UK Tier 1 supplier says the joint is smaller, lighter and more refined than predecessor technology, and represents a 'bespoke solution by GKN engineers to create a more compact joint'.
Its outer diameter is reduced by 7mm, representing an 8% reduction in the width and height of the space it occupies in the driveline. The smaller joint is also 350g lighter, representing a 23% weight reduction, yet there is no negative impact on torque capacity. Thanks to the smaller rotating mass, GKN claims the PVL joint improves performance and efficiency, and helps to lower vehicle emissions.
To support production of the all-new Q5, which is built at Audi's factory in San Jose Chiapa, GKN will manufacture the PVL at its manufacturing facilities in Mexico, demonstrating the company's ability to leverage its global footprint. Production of the PVL joint units for the Q5 represents the first time that GKN has built propshafts in its Mexico plants.
The new PVL joint uses a 10-ball bearing design rather than the 6-ball setup of standard propshafts. The larger number of smaller balls leads to 'finer geometry' between the driveline components, and reduces the noise and vibration between the different elements. it is claimed.
GKN's PVL technology is engineered to be universally compatible across VW's 'MLB Evo' architecture, which includes five brands and more than a dozen platforms. It is envisaged that the new joint could be supplied to existing product lines, to further reduce driveline weight and improve refinement.
How well do you really know your competitors?
Access the most comprehensive Company Profiles on the market, powered by GlobalData. Save hours of research. Gain competitive edge.
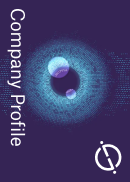
Thank you!
Your download email will arrive shortly
Not ready to buy yet? Download a free sample
We are confident about the unique quality of our Company Profiles. However, we want you to make the most beneficial decision for your business, so we offer a free sample that you can download by submitting the below form
By GlobalDataThe new PVL joint also features GKN's Direct Torque Flow (DTF) interface technology, which replaces the conventional and time-consuming bolted joint assembly with a unique 'mating' system, where the splined shaft from a third-party gearbox is inserted directly into the inner race of GKN's joint. This reduces component complexity, improves the torque flow efficiency and makes production line assembly faster for automakers.
Arnaud Lesschaeve, GKN Driveline Chief Executive Officer of Constant Velocity Joint Systems, said: "Global mega platforms are becoming increasingly common in the automotive industry, but that does not mean that GKN has a one-size-fits-all approach to its lightweight, high-performance technology. We lead the world in vehicle driveline systems, but we continually strive to innovate and improve, creating bespoke solutions to ever more demanding requirements. GKN has unrivalled capability to deliver those solutions to customers across a global network of engineering and manufacturing facilities."