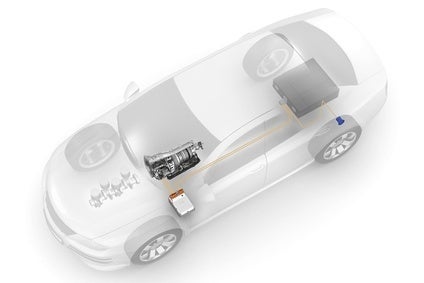
ZF has started production of a transmission that integrates a high-performance and compact electric motor into its latest eight-speed automatic gearbox – a hybridised drive system that has been specifically designed to meet plug-in requirements. Vehicles can now be driven purely electrically over comparably long distances and significantly faster at up to 120km/h (80mph).
Testing shows fuel reductions of up to 70% depending on the capacity of the battery system. The BMW X5 xDrive40e will be the first model to get the new driveline components.
ZF CEO Stefan Sommer said: "Electrifying the driveline is an essential means for ZF to further increase efficiency and significantly reduce emissions. As plug-in hybrid vehicles become more prolific, consumers are exposed to the performance capability of hybrid technology in general, for which we expect demand to increase for a long time, and our plug-in hybrid transmission in particular. It makes individual mobility more environmentally friendly, more dynamic, and also more sustainable, and is completely suitable for everyday use at the same time.
"??The most significant difference of the modularly designed ZF hybrid transmission compared to the volume-produced 8HP is its integrated electric motor, which is placed in the housing instead of the torque converter and fits into any available installation space."
Despite its compact dimensions, the electric motor is strong: in the X5 it provides maximum power of 83kW (113 HP) and a torque of 250 Nm from a standstill. That means that the vehicle can be driven purely electrically at a speed of up to 120 km/h and within a range of 31km (20 miles). When the vehicle decelerates, the electric motor is used as a generator to convert the braking energy into electric energy and to charge the battery.?
Purely electric driving represented one key area of development. The drag torque of the separating clutch to the combustion engine must be as low as possible.??In addition, clearly improved torsional vibrational decoupling better supports the downsizing and downspeeding concept. The functionality of the starting element has been improved and the associated comfort has increased: two dampers have been installed to reduce the torsional vibrations of the combustion engine; one is configured as a speed-adaptive damper.
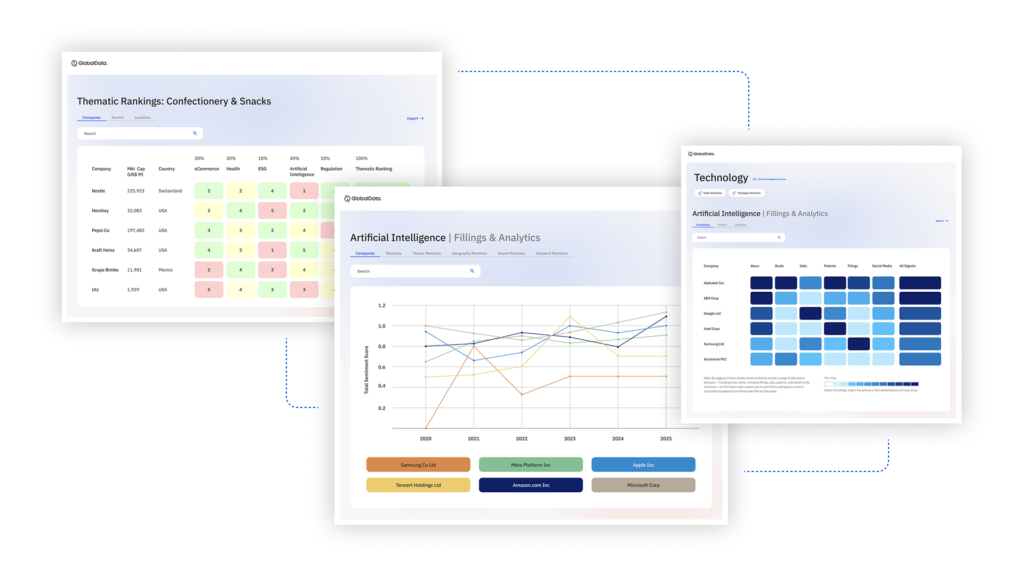
US Tariffs are shifting - will you react or anticipate?
Don’t let policy changes catch you off guard. Stay proactive with real-time data and expert analysis.
By GlobalDataThus all current combustion engines can be operated at high load from idling speed without annoying noise or vibrations.??The electric motor, which is designed as a permanent-field synchronous machine (PSM), is integrated fully into the transmission housing and is cooled by atomised oil. The integrated starting element is able to transfer up to 550 Nm of starting torque. Comfort and robustness have been improved, compared to the previous generation, by introducing a host of measures in terms of mechanics, hydraulics, functionality, and manufacturing.?
The hybrid construction kit presents diverse application possibilities: Based on hybrid-capable basic transmissions, individual tailor-made solutions are possible. The hybrid components used are part of ZF's product range. One core component is the electric motor; it is available in various output versions depending on the hybrid class. For full hybrid applications, ZF also supplies a hybrid module with an integrated separating clutch – a technical precondition for purely electric driving.
Mild, full, and plug-in hybrid applications can be provided with a high percentage of identical parts, thus creating major synergy effects.