An innovative new process to produce soft-feel trim for cheaper cars is expected to be available in vehicles from model year 2010, according to interiors specialist Johnson Controls.
The aim of the dual component injection-moulding process for automotive interior parts is to produce a high-performance component from substrates and soft foam surfaces in a single processing step.
The process is being developed by the ‘Dolphin’ consortium which includes BASF, Engel Austria, Georg Kaufmann and P-Group.
Oliver Becker, JCI’s director of advanced manufacturing engineering, said: “The Dolphin process has the potential for fast, high-quality, economical production of sandwich-moulded components such as central consoles, armrests and glove compartments. At the same time, it will help secure the competitiveness of even high-wage manufacturing locations.”
One of the main benefits is the reduced number of processing steps required, compared to the classic process that typically involves multiple stages. At the same time, the number of tools required is also reduced from four to just one and a half. The advantage of this is that significant cost savings can be made in producing practically identical components. This has already been verified with an armrest of a current vehicle model of the lower middle segment. Initial testing of the parts according to the specifications of individual automakers has been very promising.
How well do you really know your competitors?
Access the most comprehensive Company Profiles on the market, powered by GlobalData. Save hours of research. Gain competitive edge.
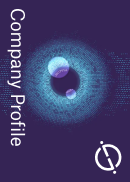
Thank you!
Your download email will arrive shortly
Not ready to buy yet? Download a free sample
We are confident about the unique quality of our Company Profiles. However, we want you to make the most beneficial decision for your business, so we offer a free sample that you can download by submitting the below form
By GlobalDataThis new development is primarily aimed at vehicles in the lower segments, which, for cost reasons, are built using components with untreated (tool blank) or painted surfaces. At the same time, soft touch surfaces in these segments could also greatly enhance the perceived value of the cars.
This new production technology for soft touch interior components will replace the previously required steps – of injection-moulding a substrate, producing a surface and then connecting the two components together to form one part – with a single processing step.
A substrate is initially formed on one machine with dual injection-moulding units by the classic injection-moulding process. Then the tool turns over into the second injection-moulding unit, where it is sprayed with special polyester blown with nitrogen gas. As the gas expands within the tool, the polyester begins to foam. At the same time, a compact skin forms on the surface of the tool.
Since the substrate material and the outer surface are chemically related polyester plastics, good adhesion occurs between the two layers. And – unlike the conventional combination of completely different types of plastic – it is also easier to recycle.