Ford’s president and CEO Alan Mulally on Wednesday launched volume production of the automaker’s smallest petrol engine – the new one-litre, turbocharged, direct injection EcoBoost unit that will be available first in Europe in early 2012 and eventually worldwide.
In its launch Focus application, it will produce 125PS and CO2 emissions performance of 114g/km – a level Ford claims is unmatched by competitors such as the VW Golf and GM Opel Astra. A planned 100PS version will deliver claimed outright best-in-class petrol CO2 emissions of 109g/km. The 125PS version uses as little as five litres of petrol per 100km.
Ford said it has spent EUR134m ($200m) to develop a special assembly line at its Cologne engine plant to build the new motor. The plant’s 870 employees will build up to 350,000 units a year.
European production capacity could increase to up to 700,000 units per year when a new plant in Craiova, Romania, starts making the new engine early next year. The automaker expects eventually to expand production outside Europe to up to 1.3m worldwide.
Nearly 100 new machining units and a 580-metre purpose-built assembly line have been installed in Cologne.
Fifty-five automated and 14 semi-automated processes are used, alongside 90 work stations. The technology is capable of machining to an accuracy of 10 microns.
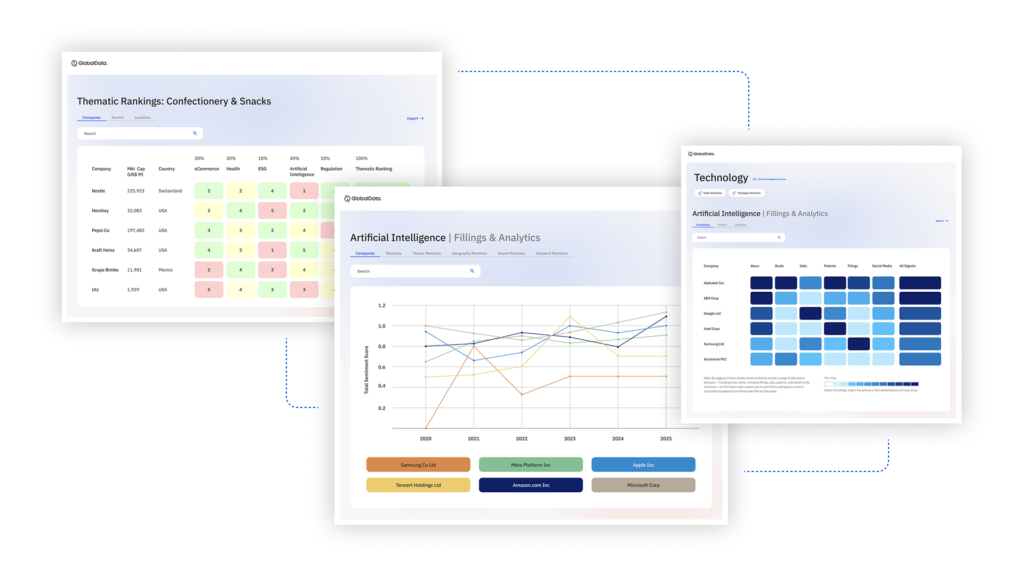
US Tariffs are shifting - will you react or anticipate?
Don’t let policy changes catch you off guard. Stay proactive with real-time data and expert analysis.
By GlobalDataNew manufacturing techniques reduce the volume of coolant required when machining aluminium engine parts to just four or five millilitres per component from a previous requirement of up to two litres, a reduction of over 99% that contributes to a reduced environmental footprint from manufacturing.
New “cold testing” technology allows completed engines to be tested without being started – reducing fuel usage and CO2 emissions from the process by 66% – while 100% of the remaining energy required to run the plant comes from renewable sources. Total electricity demands have been reduced by 66% compared with production of Ford’s four-litre V6 engine – which ended today.
Rival GM is doing much the same with a 1.4-litre I4 turbo unit used widely in Europe and North America. Initial supplies came from Opel plants in Europe but US production – for models such as the Chevrolet Sonic, Cruze and Volt – was added later. GM is also planning a new family of small I4 engines from one- to 1.5-litres.
Ford said the one-litre EcoBoost engine delivers performance to rival a traditional 1.6-litre engine and with significantly improved fuel efficiency and lower CO2 emissions.
“Ford’s commitment to Germany as a high-tech manufacturing location is significant,” Mulally said. “Nowhere outside of the US do we have a stronger design engineering and manufacturing presence than we do here in Germany.”
The engine will be available later in the C-Max as well as the upcoming B-Max which enters production in 2012.
It was developed in Europe at the automaker’s European Research and Advanced Engineering Centre in Aachen, Germany, and the Dunton Technical Centre, UK.