Bosch says it has extended its steering-angle sensor offering to include a new cost-effective model.
The company claims that the LWS6 meets all standard requirements of today’s safety and comfort systems, and is especially suitable for ESP applications in vehicles of compact class and below.
The signals from the LWS6 can also be used for systems such as electro-hydraulic power steering or ACC adaptive cruise control. The sensor recently went into series production.
Steering-angle sensors measure the steering wheel’s actual position, the value which an increasing number of systems use to determine the direction the driver wants the vehicle to take. The new LWS6 measures relatively over an unlimited measuring range.
Bosch describes the technical characteristics of the new system:
“Its typical steering-angle signal resolution is 1.5 degrees. The current LWS5 steering-angle sensor, which provides very accurate measurement, is based on a technology known as GMR (giant magneto resistance). The LWS6 steering-angle sensor, by contrast, uses the Hall effect.
How well do you really know your competitors?
Access the most comprehensive Company Profiles on the market, powered by GlobalData. Save hours of research. Gain competitive edge.
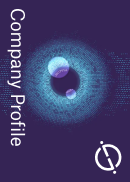
Thank you!
Your download email will arrive shortly
Not ready to buy yet? Download a free sample
We are confident about the unique quality of our Company Profiles. However, we want you to make the most beneficial decision for your business, so we offer a free sample that you can download by submitting the below form
By GlobalData“For this purpose, a multi-pole magnet is fixed to the steering column. Hall elements detect changes in the sensor’s magnetic field without contacts and without gear wheels. As two or more Hall elements are used, any rotary motion generates square-wave signals, which show a certain phase shift relative to each other. These square-wave signals are transmitted directly to the control unit, thus ruling out any need for evaluation logic in the LWS6. Processing of the sensor signals is carried out by the system control unit, which calculates the position, rotation direction, and rotation speed of the steering wheel.
“The control unit also validates the sensor output signals and detects short-circuits, for example. Moreover, due to the incremental measuring principle of the LWS6, it no longer has to be calibrated by the car manufacturer.. Thanks to the new concept used in the LWS6, Bosch has reduced the cost, not only of the sensor, but also of the system as a whole – and has also made a further contribution to achieving the goal of “safety for everyone”.
“As there is no mechanical link between the Hall measuring elements and the magnetic hub, the sensor is wear-free. Unlike optical sensors, the magnetic measuring principle makes the LWS6 resistant to contaminants, such as dust, which can find their way into the housing over the course of the device’s service life. As with the LWS5, the LWS6 does not require stand-by current when the vehicle is parked. Customer-specific designs offer extensive adaptation options for a variable steering column installation or integration into the switch unit. The new Bosch sensor has been developed in accordance with current environmental requirements and is made of lead-free components.”