Coinciding with the five million cars and 200,000 aluminium bodied models production milestones, Audi has introduced a new manufacturing process in Neckarsulm, Germany, which enables customers to make last minute specification changes to their highly ‘bespoke’ vehicle as late as two days before it is due for completion.
Four years in development, the revolutionary new production system is claimed to be unique to Audi.
The pioneering new process will reduce production delays, allowing dealers to quote more precise delivery times.
The new production regime makes it is possible to maintain tighter control over vehicles on the production line than before.
The sequence of numbers allocated to cars during order scheduling is maintained systematically when directing cars through the plant, right up to the assembly stage. The completed vehicles leave the assembly lines in the same sequence that was scheduled at the beginning of the process chain –they are lined up and controlled like pearls on a string.
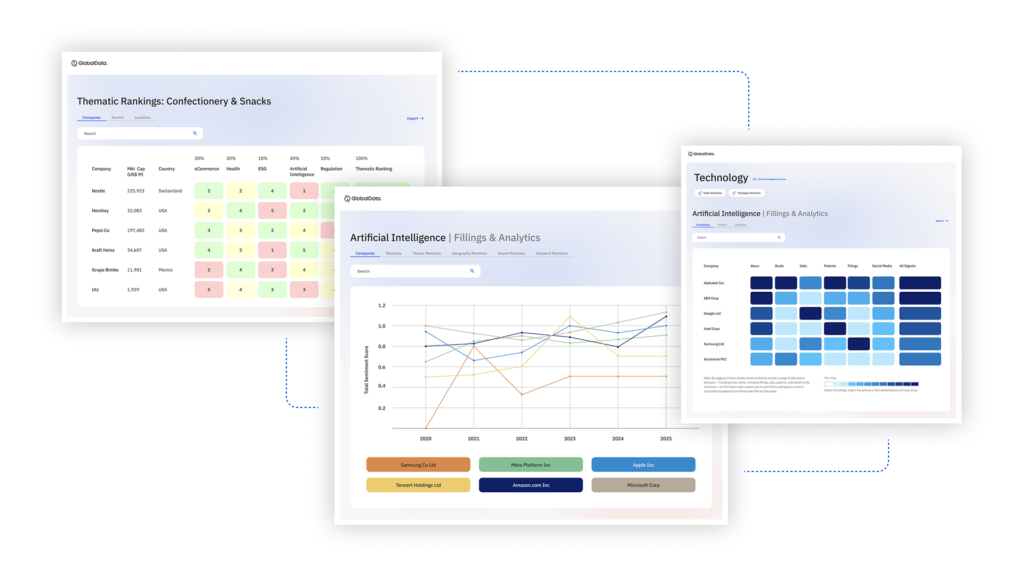
US Tariffs are shifting - will you react or anticipate?
Don’t let policy changes catch you off guard. Stay proactive with real-time data and expert analysis.
By GlobalDataIf the sequence is changed, for instance if a vehicle is removed from the production line for auditing, blanks known as ‘body buffers’ are inserted to maintain the original sequence. In order to compensate for these sequence changes, innovative planning and control computer software has been specially developed.
Another important benefit of the new system, particularly for maintenance of the vehicle sequence, is the ability to predict parts requirements more accurately. The consistent availability of parts makes the entire production process more stable.
Last year, prior to the introduction of the new manufacturing process, the daily production figures exceeded 1,000 vehicles per day for the first time.
Neckarsulm builds Audi’s A2, A6, RS 6 quattro, allroad quattro and A8 models. Annual production is around 250,000.