Dual sourcing to avoid any repeat of the effects of the 11 March Japanese earthquake and tsunami is clearly on the mind of Toyota Motor Europe’s manufacturing purchasing chief but the automaker is not being rushed into decisions.
“I think that’s absolutely the right thing for us to be looking at but we haven’t made any conclusions yet,” Mark Adams, vice president purchasing, manufacturing group, told just-auto on the sidelines of a media event at the company’s Yaris-making plant in northern France.
“It’s really down to our Japanese colleagues at TMC (Toyota Motor Corporation) because they were directly affected by some first tier suppliers. For ourselves, we were affected by those somewhat down the chain, the third and fourth tier suppliers who supply the big multinationals that supply us, so I think the question has to be passed down the line to our first tier.”
Adams said one solution, where intellectual property issues might cause concern, would be to, for example, instead of dual sourcing, “to reserve the right to have programmable electronic chips in the event we were to lose the capacity for fully masked program chips”.
But he stressed that all such ideas and discussions were in “early days yet”.
He praised the “calm dignity” of the Japanese people who worked “astonishingly hard” to restore supplies from the country in many cases. Where that was not possible, alternative sourcing was generally arranged by first tier suppliers, normally from the same company but another facility.
How well do you really know your competitors?
Access the most comprehensive Company Profiles on the market, powered by GlobalData. Save hours of research. Gain competitive edge.
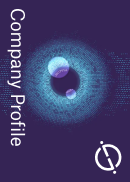
Thank you!
Your download email will arrive shortly
Not ready to buy yet? Download a free sample
We are confident about the unique quality of our Company Profiles. However, we want you to make the most beneficial decision for your business, so we offer a free sample that you can download by submitting the below form
By GlobalData“That is one of the functions they supply to us.”
Suppliers to the new third generation Yaris – final line training was under way and body panel stamping and welding was ramping up when we visited on Wednesday – were brought in three years prior to production (compared with 18 months). This is the earliest for any Toyota Europe project to date.
Adams said: “Project by project, we have been moving forward in the process the time in which we involve the suppliers.” He added it was always a balance between normal commercial pressure on the supplier and reaching the point where it was too late for the vendor to influence the design.
He said involving suppliers earlier actually reduced development time overall as the automaker wasn’t requesting design changes at an advanced stage; instead the design of parts evolved with the car and the simultaneous engineering brought productivity results.
“The main factor has been getting the quality of manufacturing considered more deeply earlier in the process.”