The adoption of the “design to cost” method, use of carry-over parts to optimise reliability and manufacturing costs and the application of digital design in developing the Renault Logan ‘emerging markets’ car made it easier to keep to the programme costs laid down at the start of the project.
The final development budget for the Logan was €360 million and the investment for production by country was: Romania €205 million; Russia €230 million; Morocco €22 million; Iran €300 million; and €16 million in Colombia.
“The ‘design to cost’ method was introduced at Renault in 1992 with the Twingo project, and underwent a decisive development with the launch of the X90 project in 2000”, said engineering project manager Odile Panciatici, who was also involved in the Twingo development.
The idea is to keep the design process firmly focused on reliability and cost-cutting by using tried and tested solutions. The method also incorporates some aspects of product and process analysis.
The parameters are feasibility, expected benefits, local opportunities and, most important of all, reliability. So it was decided to use traditional types of steel to build the Logan because they could easily be adapted to production methods and equipment at the planned production sites, where processes are less automated, and they can be sourced locally.
How well do you really know your competitors?
Access the most comprehensive Company Profiles on the market, powered by GlobalData. Save hours of research. Gain competitive edge.
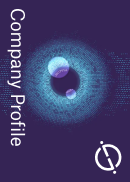
Thank you!
Your download email will arrive shortly
Not ready to buy yet? Download a free sample
We are confident about the unique quality of our Company Profiles. However, we want you to make the most beneficial decision for your business, so we offer a free sample that you can download by submitting the below form
By GlobalDataSimilarly, from the early stages the limitations of stamping were taken into account in the Logan’s design. The number of contours in the bodywork was kept to a minimum to simplify the production of manufacturing tooling, make the stamping and body-in-white assembly processes more reliable, and restrict costs. The slight curve of the glazed areas, especially the rear screen, keeps machine tool costs low.
Despite the lack of automation, it was still possible to fit a one-piece exhaust to the underbody.
Further significant progress has been achieved by moulding brake pipes at the plants and protecting them with longitudinal members that have no added parts, and using a fuel tank with integral filler neck and a removable external filter for countries that use “non-stabilised” fuel.
Another key factor in reaching the cost targets set for the Logan was the choice of a front suspension similar to that used by the Clio, with no anti-roll bar, and rear suspension taken from the Renault-Nissan alliance’s B platform.
In addition, to keep down tooling costs and make assembly simpler, the rear view mirrors and protective mouldings are designed so that they can be placed on the left or right hand side of the vehicle. Using a single window in the rear doors avoids the cost of adding a quarterlight.
Carry over parts for reliability and cost control
Using the same components in several vehicles helps a carmaker to ensure reliability for customers and achieve savings for the brand. This approach, which has proved its worth for the most successful Asian manufacturers, can be seen at all levels in the X90’s development.
The Logan can trace its roots to two existing projects: the Alliance B platform and the Clio. It has a B platform-style body structure, which helped keep down chassis development costs, manufacturing process expenses and production tooling costs.
The heating system is the same one that will be used in other Renault B segment vehicles, such as the new Modus mini-minivan launched a few weeks ago in Madrid.
The single-part design approach, using simple pipework and short circuitry, ensures high mechanical reliability and helps to make savings on design costs without sacrificing thermal performance, which is said to be among the best in the segment.
Electronic functions are grouped together in a central cabin unit based on the one used in the Clio and Twingo. The Logan has the same engine compartment as the Clio, designed using the same interfaces so that proven assembly procedures can be used.
The Logan also has the Clio’s engines, front suspension system, steering and rear brakes, as well as its instrument panel, door handles, steering wheel and column switches. Some parts, such as the air vents and gear lever knob, have been used in the Espace minivan.
The advantages of digital design
The X90 was a pilot project for using digital simulation in designing vehicles and production tooling, as well as for adjusting manufacturing processes.
Calculating vibrations and testing acoustics on digital models helped designers to predict noise levels in the vehicle without using a physical model. The advantage of the digital method, especially in defining and developing the body structure, is that costly prototypes of vehicles and tooling do not have to be built so many physical stages in the design process are eliminated. The total cost saving is estimated at about €20 million.
The X90 project plans for vehicles to be assembled at production sites that have highly competitive costs. Renault has decided to take a labour-intensive approach for assembly while using the technologies available locally, with low automation levels.
Because of the mainly manual assembly process, the engineers have tried to optimise the use of materials and have not developed any large body panels.
They have also managed to avoid using laser butt welding technology for sheet metal assembly.
Powertrain development has benefited from the competitiveness of Dacia’s Pitesti plant. Many powertrain parts are machined at the site, such as the cylinder head cover, mounting brackets, engine mountings and oil sump. The engines and transmissions will also be entirely assembled locally.
The plants that will produce the Logan will deploy the Renault Production Way (French acronym SPR – Système de Production Renault). This system, introduced in 1998, has ensured the group’s sites are among the most efficient in the world, according to Renault.
SPR brings together everyone involved in the production process –purchasers/suppliers, logistics experts, engineers and manufacturers – to focus on common targets and procedures. One aspect has been the setting up of “dexterity training” or “patterning”, which helps operators to perform movements more easily and effectively.
SPR, which is based on Nissan’s approach to production, makes the workstation the focal point of industrial organisation and standardises the movements made at each workstation in great detail. This approach optimises plant productivity, product quality and workstation ergonomics.
Another system which deals with programmed, efficient logistics for workstations makes parts directly available to the operator, while the standardisation of workstations and drafting of standard operations sheets make it clear to operators exactly what they have to do.
The X90 project calls on 143 first-tier suppliers, 43 of which are located in Romania, nine in Turkey, five in Eastern and Central Europe and 10 in Western Europe.
Three types of support have been devised to support suppliers on a case by case basis: strengthening their legal structure and analysing their financial situation; introducing optimised management and work organisation; and making experts available in engineering, quality, methods, logistics and purchasing.
The international deployment of the X90 project will use a strategy that combines the supply of CKD (Completely Knocked Down) kits from Romania and from local suppliers. It will take full advantage of the synergies achieved by RNPO (Renault-Nissan Purchasing Organisation).