
Ford, with design and testing consultation from 3M, has developed a new powered air-purifying respirator (PAPR). Production started today (14 April) at the automaker’s Vreeland facility near Flat Rock, Michigan, with paid UAW volunteers, with the ability to make 100,000 or more.
Ford, in collaboration with the UAW, is also now producing face masks at the Van Dyke Transmission Plant for internal use globally and pursuing certification for medical use.
The automaker also plans to manufacture reusable gowns from airbag materials with supplier Joyson Safety Systems and is lending its manufacturing support to help Thermo Fisher Scientific quickly expand production of COVID-19 collection kits for patient testing.
Production of more than 3m face shields is already under way in Plymouth, Michigan.
“We knew that to play our part helping combat coronavirus, we had to go like hell and join forces with experts like 3M to expand production of urgently needed medical equipment and supplies,” said Jim Baumbick, vice president, Ford enterprise product line management.
“In just three weeks under Project Apollo, we’ve unleashed our world-class manufacturing, purchasing and design talent to get scrappy and start making personal protection equipment and help increase the availability and production of ventilators.”
How well do you really know your competitors?
Access the most comprehensive Company Profiles on the market, powered by GlobalData. Save hours of research. Gain competitive edge.
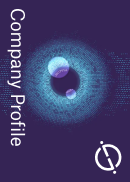
Thank you!
Your download email will arrive shortly
Not ready to buy yet? Download a free sample
We are confident about the unique quality of our Company Profiles. However, we want you to make the most beneficial decision for your business, so we offer a free sample that you can download by submitting the below form
By GlobalDataSince late March, Ford manufacturing, purchasing and supply chain experts have been embedded at 3M manufacturing facilities to help increase production of urgently needed products. With this additional help, both companies were able to increase the output of PAPRs and N95 respirators at 3M’s US-based manufacturing facilities.
Now Ford itself will start producing an all-new PAPR design – development time was cut to less than four weeks.
The newly designed PAPR includes a hood and face shield to cover health care professionals’ heads and shoulders, while a high-efficiency (HEPA) filter system provides a supply of filtered air for up to eight hours. The air blower system – similar to the fan found in F-150 truck ventilated seats – is powered by a rechargeable, portable battery, helping keep the respirator in constant use.
The development team expects the respirator design will meet the pending National Institute for Occupational Safety and Health (NIOSH) limited use protocol to respond to the COVID-19 public health emergency, with approval anticipated by the end of April.
Pending approval, 3M will distribute the newly designed PAPRs through its US network. Both companies will donate any profits they earn from the sale of the PAPR to COVID-19 related nonprofit organisations.
Ford’s global manufacturing and purchasing teams quickly sourced the necessary materials and equipment from its network of equipment manufacturers around the world and face mask production began this week.
Approximately 30 UAW paid volunteers are making masks in the transmission plant’s ISO Class 8 cleanroom, which is a controlled environment with extremely low levels of pollutants, enabling the safe production of face masks for medical use. Eventually, approximately 80 UAW paid volunteers will make masks as production increases.
Ford also is leading efforts to manufacture reusable gowns with airbag supplier Joyson Safety Systems. The go fast project has created re-usable gowns manufactured from material used to make airbags.
Production of gowns will reach 75,000 gowns a week by Sunday and scale up to 100,000 gowns for the week of 19 April. By 4 July, Joyson Safety Systems will cut and sew 1.3m gowns, which are self-tested to federal standards and washable up to 50 times.
Ford worked with Beaumont Health in Metro Detroit to quickly design the gown pattern and test for sizing during fit and function trials. More than 5,000 gowns have already been delivered to the hospital.
Ford is helping scale production of collection kits for COVID-19 tests at Thermo Fisher Scientific.
Thermo Fisher’s engineering team at the company’s site in Lenexa, Kansas, realised their expertise, combined with the manufacturing expertise of Ford’s nearby Kansas City Assembly Plant engineering team, could help set up additional collection kit production machinery. The Ford team also helped Thermo Fisher adapt machinery that currently runs glass vials for other products to run plastic vials required in drive through coronavirus test collection.
“Ford’s engineers brought a fresh perspective to production expansion, and together, we’ll more than triple the number of collection kits we can deliver each week starting 20 April,” said John Reuss, senior director, microbiology business for Thermo Fisher.
Ford also is continuing to manufacture transparent full face shields for medical workers. As of 13 April, it had produced more than 3m face shields for medical personnel and first responders. Besides the US, face shield production also has started at Ford facilities in Canada and Thailand and with Ford joint venture partner Mahindra & Mahindra in India.
Work at Rawsonville (Michigan) Components Plant is under way to transform a portion of the plant to manufacture a third party ventilator, in collaboration with GE Healthcare, with production expected to start the week of 20 April. Built by paid UAW volunteers, the goal is to produce 50,000 Model A-E ventilators by 4 July to help COVID-19 patients.
Ventilator pre-production activities are also under way in the UK where Ford and an industry consortium are preparing to make ventilators from Penlon.
Ford is providing manufacturing engineering capability, project leadership, purchasing support and assembly of the ventilators at its Dagenham engine plant. This production will help meet demand for 15,000 ventilators ordered by the UK government.