
Ford said it had shipped the first powered air purifying respirators (PAPR), developed with 3M, to help protect health care workers fighting COVID-19.
Since late March, the automaker has been working with 3M to develop PAPRs and put them into production, using design help from 3M and off the shelf auto industry parts, like vehicle ventilator fans and power tool batteries.
In a separate effort, 500,000 reusable medical gowns distributed by Ford will soon be on their way to the state of New Jersey.
The automaker and 3M worked with Ford's automotive supply chain to progress the new PAPR from idea to product in fewer than 40 days.
The product development team moved quickly to design the new PAPR, combining vehicle air conditioning expertise with 3M knowledge of medical devices.
Hand drawn concepts were created one day after starting the project. Engineers also used vehicle seat trim expertise to design the PAPR hood. In parallel, an advanced manufacturing team rapidly prototyped the PAPR using 3D printing while purchasing worked with suppliers to procure and produce components and the manufacturing team designed the production process. Assembly lines and production started within three weeks of the initial request.
How well do you really know your competitors?
Access the most comprehensive Company Profiles on the market, powered by GlobalData. Save hours of research. Gain competitive edge.
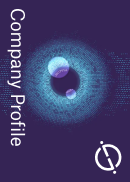
Thank you!
Your download email will arrive shortly
Not ready to buy yet? Download a free sample
We are confident about the unique quality of our Company Profiles. However, we want you to make the most beneficial decision for your business, so we offer a free sample that you can download by submitting the below form
By GlobalDataThe PAPR has a hood and face shield to cover health care professionals' heads and shoulders while a high-efficiency (HEPA) filter system provides a supply of filtered air for up to eight hours.
The air blower system – similar to the fan in the F-150 truck ventilated seats – is powered by a rechargeable, portable battery.
Approximately 90 paid UAW volunteers have assembled 10,000 PAPRs at Ford's Vreeland factory near Flat Rock, Michigan and there is provision to make 100,000 or more.
Around 10 companies in the automotive supply chain are providing new and off the shelf parts for use in the PAPRs. Components include hood tops, filters and fans, power electronics, switches and foam seals.
3M will sell and distribute the PAPR through its own distributors but they also can be ordered directly from Ford. 3M will provide technical support.
In addition, Ford suppliers are now producing 200,000 washable medical gowns a week and over 400,000 have been shipped to medical workers around the US.
The state of New Jersey has also ordered 500,000.
The health care equipment was spearheaded by Ford's Project Apollo team which was inspired by the effort in 1970 to help NASA's disaster stricken Apollo 13 astronauts.
Engineers back then had to come up with a way to produce a system to 'scrub' (remove CO2 from) air in the lunar module 'lifeboat' using different shaped filters designed for the unuseable command module atop the service module which lost most of its electricity supply when a fuel cell exploded.
Ford also is making and supplying PPE and health care equipment, including 12m face shields, ventilators in collaboration with GE Healthcare and medical masks for its own workforce.