Ford and its consortium partners have received government backing for the introduction of 5G connectivity to speed up electric vehicle manufacturing.
A 5G mobile private network delivered by Vodafone Business, will be installed this year in the new E:PriME (Electrified Powertrain in Manufacturing Engineering) facility on the automaker's Dunton research and development campus.
Ford said the 5G network will overcome many of the issues surrounding wireless connectivity in the industrial setting.
It promises reduced delays, wider bandwidth, improved security and reliability, and faster deployment time.
By the time installation is complete in the autumn, E:PriME Dunton will have the fastest possible connectivity alongside the consortium's second network at welding research specialists TWI, based in Cambridge.
Both sites' connected equipment will offer real time control, analysis and remote expert support, ensuring new manufacturing processes are shop floor ready.
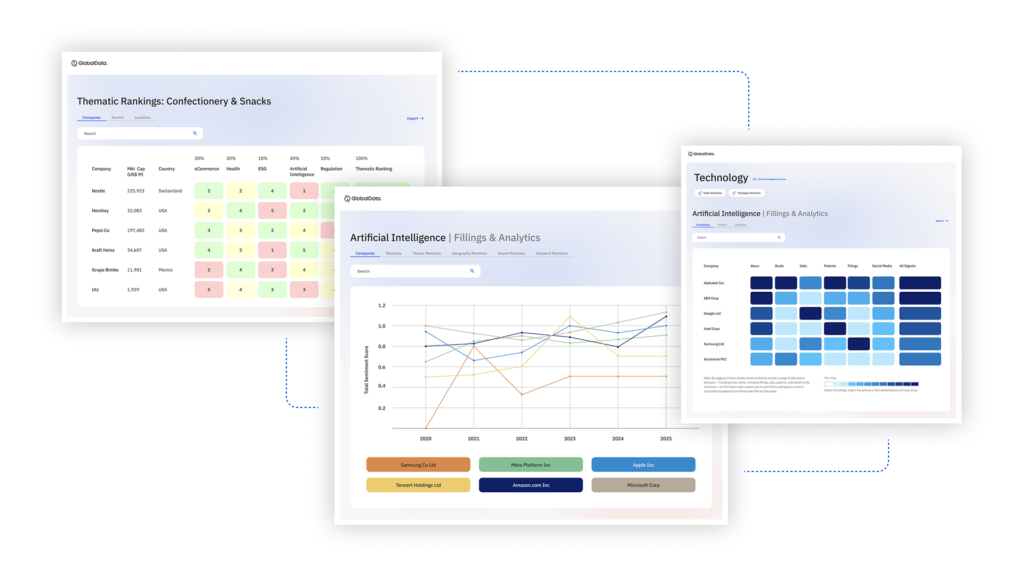
US Tariffs are shifting - will you react or anticipate?
Don’t let policy changes catch you off guard. Stay proactive with real-time data and expert analysis.
By GlobalDataFord will focus on the connectivity of the welding machines in the manufacture of electric vehicles.
The batteries and electric motors within an EV require around 1,000 welds.
For a single EV product, this could generate more than a half a million pieces of data every minute.
Fast, reliable, high capacity data capture and analysis will be a significant requirement of these processes.
Connecting the data with experts, such as TWI and manufacturers, is critical if processes are to develop at the same rate as these innovative products demand.
Chris White, Ford 5GEM project lead, said: "Connecting today's shop floor requires significant time and investment. Present technology can be the limiting factor in reconfiguring and deploying next gen manufacturing systems.
"5G presents the opportunity to transform the speed of launch and flexibility of present manufacturing facilities, moving us towards tomorrow's plants connected to remote expert support and artificial intelligence."
Public grant funding is subject to the conclusion of agreements between all parties.