
Ford has announced its first new ‘EcoBlue’ advanced diesel engine which, it said, would “offer optimised fuel efficiency and reduced CO2 and NOX emissions for customers, using sophisticated technologies and innovative design”. The new engine line supplements the automaker’s established EcoBoost petrol engines and will be used in a wide range of future passenger cars and commercial vehicles, with power outputs ranging from 100PS to 240PS.
The I4, two-litre EcoBlue made its European debut at the commercial vehicle show in Birmingham, England, in Ford’s Transit and Transit Custom vans.
The engine was developed completely in-house at Ford’s Dunton, England and German R&D centres and will be made at the automaker’s Dagenham Diesel Centre in east London. It is not part of the ongoing PSA Group-Ford joint venture that produces smaller capacity diesels for both automakers at Dagenham, a Ford spokeswoman confirmed.
The new two-litre motor replaces the long serving, 2.2-litre TDCi diesel. Ford said drivability is enhanced with 20% more torque at 1,250rpm. It also claims the new engine delivers passenger car refinement to the commercial segment, reducing radiated noise by 4dB at idle.
“EcoBoost created a new standard for petrol engines – smaller, more efficient with surprising performance. That same obsession to innovate for the customer is behind our new EcoBlue diesel engine range,” said Jim Farley, chairman and CEO of Ford of Europe. “This new engine lifts fuel efficiency and reduces CO2 by over 10% in Transit, lowering costs for our customers.”
A new engine architecture results in reduced friction and a cleaner-burning combustion system. Multiple innovations that reduce friction, contributing to a 13% improvement in fuel efficiency, include:
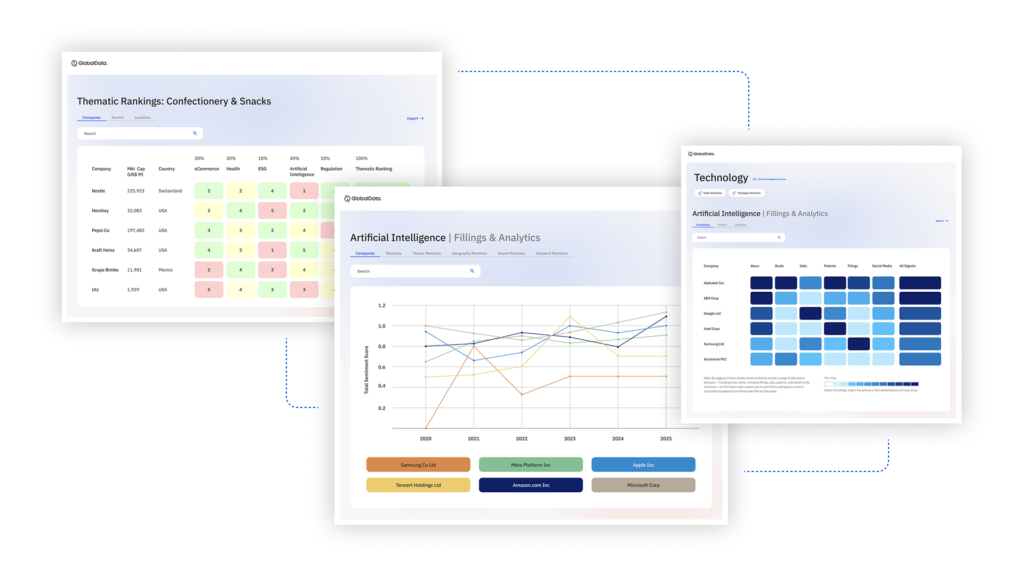
US Tariffs are shifting - will you react or anticipate?
Don’t let policy changes catch you off guard. Stay proactive with real-time data and expert analysis.
By GlobalData- A 10mm offset crank design that minimises piston side-load, reducing rubbing forces against the cylinder walls of the downsized four-cylinder iron block
- Minimised crankshaft bearing diameters
- A belt-in-oil design for the camshaft and oil pump drive belts
- An optimised valve train and a new single-piece camshaft module
Ford is for the first time using a new mirror-image porting design for the integrated inlet manifold that precisely controls the flow of air into the cylinders – with clockwise airflow for cylinder numbers one and two, reversed for cylinder numbers three and four.
This symmetrical arrangement ensures optimum mixing of fuel and air in the combustion chambers of all four cylinders. When fine-tuning the combustion process, computer experiments used measurements from more than 1,400 factors that affect performance of the valve lift and timing alone.
“Our first ever mirror-image inlet design in combination with an optimised combustion chamber layout helps us turn fuel into energy more effectively than any diesel engine we’ve ever produced,” Werner Willems, a Ford technical specialist, combustion systems, said.
New fuel injectors are capable of delivering up to six injections per combustion event, with each injection taking as little as 250 microseconds (0.00025 seconds) and delivering 0.8mg of diesel – equivalent to a grain of sugar. This tiny volume of fuel is injected through eight conical holes each 120 microns in diameter – about the width of a human hair.
Piezoelectric technology that uses electrically-responsive crystals to closely control fuel delivery – typically found in premium passenger-car engines – is incorporated into the body of the injector unit. The new injectors deliver reduced noise levels; minimal energy wastage from the fuel pump; more responsive and less intrusive auto-start-stop performance; and real-time calibration correction for maximum fuel efficiency.
Turbocharging
A new compact turbocharger has been specifically designed to deliver more air at lower engine rpm compared with the outgoing 2.2-litre TDCi engine, for a light and “urgent” feel across the rev range and up to 340Nm of torque at 1,250rpm.
An aerodynamically advanced turbine wheel – made from Inconel, an alloy used in extreme temperature environments such as rocket engines – is reduced in diameter by almost 10%. The aerospace aluminium grade compressor wheel is reduced in diameter by 15%. The reductions decrease inertia and enable faster boost performance with wheel speeds up to 240,000rpm, contributing to improved low-end torque.
“One important factor we noticed through customer feedback is a growing tendency for drivers to ‘creep’ their diesel powered vehicles by engaging the clutch while the engine is at idle – making low-down torque even more essential,” said Paul Turner, base engine technical leader, Ford of Europe.
Compressor wheels are milled from solid, rather than cast, improving tolerances to within two or three microns – around the size of a single bacterium – increasing durability and reducing noise and vibration. A new turbocharger actuator replaces a worm drive with a geared design that halves response times to 110 milliseconds.
Sophisticated after-treatment processes (urea injection; selective catalyst reduction SCR) for exhaust gases enable ultra-low emissions in line with the stringent new Euro Stage VI standards that will be introduced in September 2016, requiring a 55% reduction in NOx emissions compared to Euro Stage V. Ford said the new engine would comfortably meet future European emissions requirements supported by its first standardised selective catalytic reduction system. The system is close-coupled to the rear of the engine for maximum efficiency and excellent cold-driving performance. A short-loop exhaust gas recirculation channel is incorporated into the cylinder head, contributing to a more compact engine design and helping optimise cooling of gases.
Enhanced refinement
The two-litre EcoBlue engine will be the first diesel commercial vehicle powertrain from Ford to achieve passenger car noise, vibration and harshness criteria, contributing to enhanced driving appeal, the automaker claimed. The new engine radiates half as much sound energy at idle as the 2.2-litre TDCi. A noise-optimised cylinder-head, block, stiffening ladder-frame and oil pan were specifically developed to be desensitised to activity inside the engine, and non-flat mating surfaces are carefully designed to offer tight seals that trap noise within the engine.
“The basic structure of an engine can act as a soundboard for the movements happening inside it, just like a bell. So we try to develop a bell that does not ring very well,” said Dominic Evans, NVH specialist, Ford of Europe. “We’ve engineered every significant noise-influencing component of this engine to be quieter and smoother operating – resulting in the most refined diesel commercial vehicles Ford has ever built.”
A moulded acoustic cover that provides foam encapsulation of the cylinder head, and a front cover made from sound deadened steel, further prevent engine noise being transmitted to the cabin for a quieter driving environment.
Additional measures taken to enhance NVH include:
- Micro-geometry analysis of gear teeth down to a micron level (0.001mm) to achieve perfect meshing for smoother operation and less high-frequency whine
- An optimised oil pump featuring unevenly spaced vanes that break up the pump’s noise frequency to make it less perceptible to the listener
- Advanced fuel injectors featuring integrated piezo-stacks, noise softening software and optimised pilot injection
Commercial vehicle durability
The new engine meets Ford’s global commercial vehicle durability standards for extreme usage in markets as diverse as Europe, the US and China. The engine’s performance has been trialled through the equivalent of 3.4m miles of durability testing including 250,000 miles at the hands of real-world customers, comprehensive analysis in laboratories and at vehicle proving grounds, and CAE evaluations at every stage of development.
The oil system – including the oil specification, oil pan and filter dimensions, bore distortion tolerances and piston ring specifications – has been engineered to extend oil life, and maintenance-free components include the camshaft belt, camshaft module, and water pump.
“We developed the EcoBlue engine using feedback from customers around the world,” Turner said. “The versatile design even allows the same block to be used for front-wheel drive and rear-wheel drive applications, and the sophisticated design and technologies deliver future-proofed fuel efficiency and emissions.”
The engine initially will be offered with 105PS, 130PS and 170PS outputs in commercial vehicles. Capable of delivering more than 200PS, the engine will later go into Ford passenger cars alongside further new EcoBlue engines – including a 1.5-litre variant.