
Yazaki is the world’s largest manufacturer of wire harnesses, supplying harnesses to the major vehicle makers worldwide. Earlier this month, Matthew Beecham talked exclusively with David Scheffler, product manager for Yazaki North America, about how the company is pushing back the technical boundaries in the vehicle electrical and electronic distribution systems arena.
Yazaki Corp manufactures and markets a wide range of products, most prominent among them being the automotive wiring harness. Yazaki is the world’s largest manufacturer of wire harnesses, supplying harnesses to the major vehicle makers worldwide. The company manufactures more than 14.7m wire harnesses annually. It also produces some 1.7m junction blocks, 422m connectors and a mind-boggling 395,000 miles of automotive wire every month.
Yazaki is a completely vertically integrated wire harness supplier. The company believes that this drives innovation at all levels of the wire harness supply base, helping to intensify its focus on developing other products that enable the optimization of its existing wire harness design, particularly in the area of reduced weight and girth. Examples of such developments include Gateways, next generation physical layer products (fibre optics), instrumentation and Digital Power Modules – all of which support the increasing trend of multiplexing technology in vehicle designs.
In January 2005, Matthew Beecham talked with David Scheffler, product manager for Yazaki North America, about how the company is pushing back the technical boundaries in the vehicle electrical and electronic distribution systems arena.
Just-auto.com: What are the carmakers demanding of wire harness suppliers?
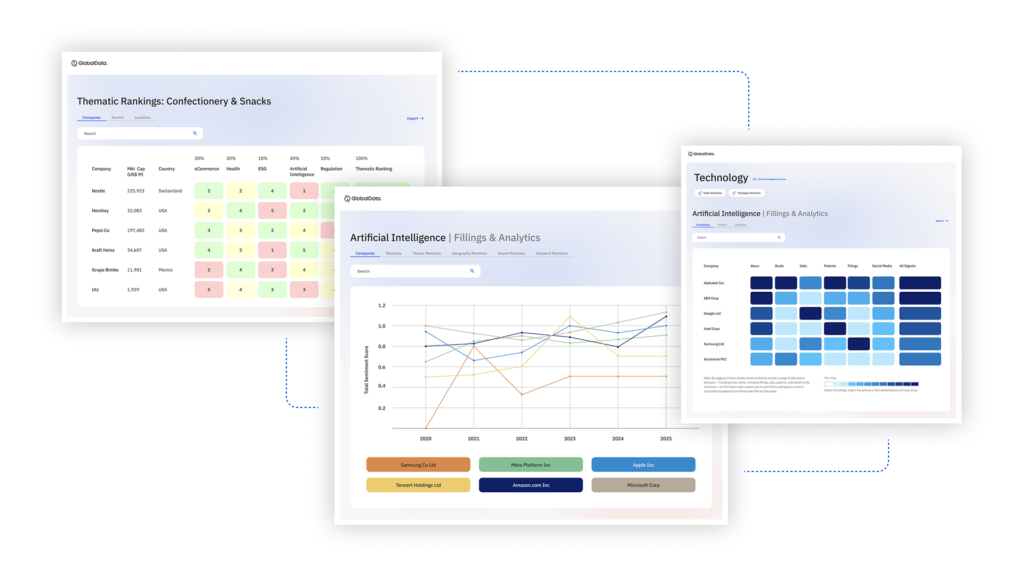
US Tariffs are shifting - will you react or anticipate?
Don’t let policy changes catch you off guard. Stay proactive with real-time data and expert analysis.
By GlobalDataDavid Scheffler: OEMs are demanding vehicle electrical systems with increased complexity and content while maintaining existing physical characteristics and providing annual price reductions.
j-a.com: As the complexity of wire harness design moves into uncharted territory, how does that impact on Yazaki’s design and development capabilities?
DS: It has required us to work with the OEMs to develop new tools that allow us to capture even earlier up-front vehicle requirements and information. Other tools have been developed in-house optimising the W/H manufacturing and logistic strategies to support the OEMs just-in-time and sequenced-parts delivery requirements. These strategies include setting up final assembly and warehousing next to the vehicle assembly plant.
j-a.com: What alternative solutions to the traditional wiring harness are you currently working on?
DS: Yazaki has developed devices and physical layer products that allow for multiplexing within the vehicle’s architecture. The products we choose to design into a vehicle are always studied upfront with a complete electrical system content analysis. We look at the requirements of the vehicle and make recommendations to the OEMs on what level of ‘device versus wire harness’ content is necessary based on such factors as: cost, weight and performance. We may recommend our Scalable Modular Architecture (SMA) for a vehicle with a high level of feature variance. This allows the OEMs to utilise our Digital Power Module (DPM) product line to optimise overall system design while continuing to meet the ever-increasing demands design complexity. Our DPM’s are strategically placed in device concentrated areas of the vehicle, which significantly reduces the overall wire harness content.
j-a.com: What about fibre optics?
DS: The current trend in America and Japan is copper based physical layer systems while Europe has led the fibre optic based initiative. Europe will continue to use fibre based systems for some time. There still seems to be some hesitation from America and Japan on truly embracing Fibre Optic based systems for vehicle networking. American OEMs still have concerns with Plastic Optical Fibre (POF) because of the perception that copper-based systems are more robust. Yazaki has been developing a next generation optical physical layer that addresses many of the concerns of POF.
j-a.com: And flexible printed circuit boards as an alternative to conventional wire harness?
DS: Flat flexible wiring will always need to be a tool within the wire harness toolset for unique applications that can not be accommodated by the traditional round wire harness. Key examples of this are headliner modules, instrument panels and door panel systems.
j-a.com: Are there any other breakthrough wiring technologies? What are there potential applications and long term prospects?
DS: Yazaki is continuously developing next generation wire harness products. We have developed Shielded Power Cable systems for the HEV market. We are a leader with the deployment of next generation high frequency coaxial cabling systems with our FAKRA line of products. We have been developing aluminium cable systems for high voltage and high current applications. This is especially useful for rear battery vehicles that require a very long battery cable. This reduces the weight impact of the necessary wiring.
j-a.com: How do you see the pace and focus of this evolution from basic wiring to an integrated electrical and electronic architecture changing as carmakers switch to 42-volts?
DS: Yazaki has the capability to provide product that will support any power or data requirement in any vehicle architecture. The trend is towards higher voltage systems that support HEV architectures. We have power gateways or DC to DC converters that would be able to support existing 14V systems as well as potential 42V systems such as lighting, HVAC, and electric brake.
![]() |
Expert Analysis
|
![]() |
![]() The above feature article was taken from a comprehensive just-auto.com report – to find out more about the report, download your sample and to order your copy, please follow this link. |
![]() |
![]() |