Land Rover is expected to commit in the coming months to make its next generation Range Rover flagship and Range Rover Sport models from a lightweight rivet-bonded aluminium chassis.
The radical weight-saving technology, which will improve fuel economy and cut tailpipe emissions of ‘greenhouse gases’, awaits only the final rubber stamp from Ford high-ups, according to well-placed sources. It is already dubbed the ‘premium lightweight architecture’ by insiders.
“The strategic decision is taken, we’re just waiting to hear go,” said an inside source.
Land Rover will base project L405, the code-name for the new RR, on a development of the monocoque technology developed for the Jaguar XJ.
That means a conventionally-pressed set of inner and outer panels rivet-bonded together with the use of castings at key structural nodes, but very few extrusions. A ‘bolt-on-front-end’ or BOFE, which reduces repair costs after a frontal crash, is said to be part of the design idea.
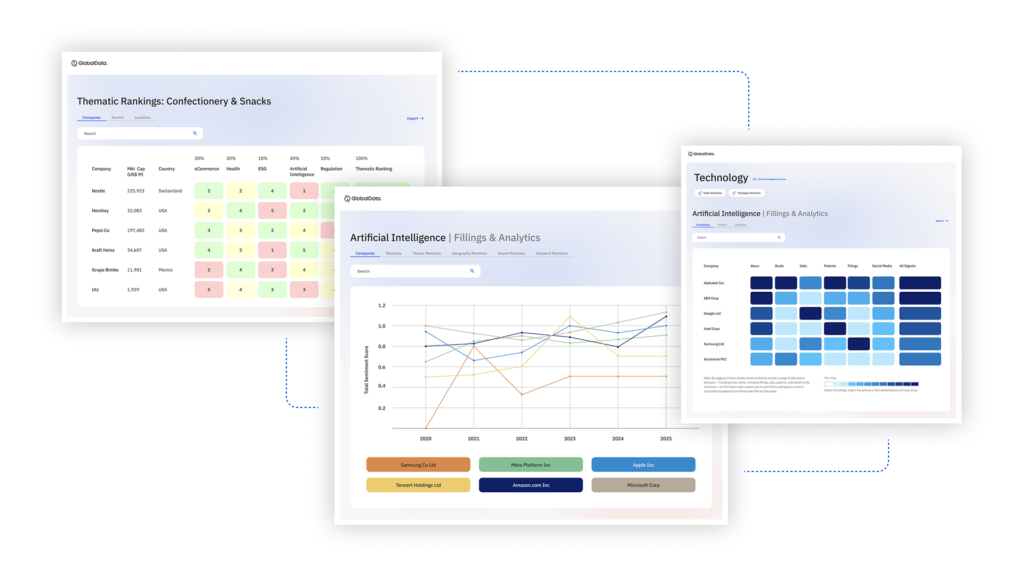
US Tariffs are shifting - will you react or anticipate?
Don’t let policy changes catch you off guard. Stay proactive with real-time data and expert analysis.
By GlobalDataThis design structure and production method suits the 30,000-a-year volume planned for the Range Rover when it hits Job One in mid-2011, ahead of a 2012 on-sale date. That was the volume also envisaged for the Jag XJ, although it has undershot its sales predictions and in reality is running at about 12,500 a year.
Jaguar’s most recent launch, the new XK sports car, uses a different structural method, employing extrusions linked to castings for the under-structure, with pressed panels for the outer skin only, a method that better matches tooling costs to 10,000-a-year production volume.
Further volume will come from the highly-successful Range Rover Sport, which will become a platform variant of the Range Rover. The current RR Sport is based on LR’s rugged, semi body-on-frame T5 platform, originally developed for the new Discovery, but pressed into service to underpin the Sport to speed that model’s time to market.
The move to alloy for Land Rover’s up-market models will mean considerable changes at the Solihull factory.
Welding guns on the body-in-white line will have to be either converted or replaced with air-powered rivet guns to drive the roughly 3,500 Henrob self-piercing rivets needed to hold together each body-in-white (BIW).
There could also be changes to Land Rover’s pressing operations. Local Midlands suppliers like Stadco, Polynorm and Hydro, who have won alloy pressing and fabricating business from Jaguar and Aston Martin, are now in line to win business from Land Rover, too.
The switch to alloy construction is expected to save 40% from the RR’s unpainted BIW, translating into a 300-400kg kerb weight saving over today’s steel monocoque-bodied Range Rover, a vehicle developed by BMW before it sold out to Ford in 2001.
“We’re targeting the upper figure and are pretty hopeful of getting there,” said another source.
A saving of 400kg will reduce the RR’s kerb weight to around 2,200 to 2,300 kg, while still allowing the car to maintain its essential road presence and roomy, luxurious cabin.
If the sort of fuel savings experienced by Jaguar on the XJ are repeated on the RR, it’s not unreasonable to imagine an alloy Range Rover powered by a V8 petrol engine averaging 22mpg compared to 19mpg – a 15% increase, an improvement difficult to achieve through better engine technology alone.
Sharper styling inspired by Range Rover’s new ‘premium sophistication’ styling theme will keep the RR at the top of the luxury SUV/4×4 segment, insiders believe. Expect an even more luxurious interior than today’s model.
Together with new powertrains, like the direct-injection five-litre V8 petrol and its supercharged version, plus an enlarged four-litre V8 diesel, Land Rover insiders are even talking about pushing the transaction price of a well-loaded RR with supercharged engine towards GBP100,000 (about $US200,000) at today’s prices. The most expensive RR today lists at GBP70,000, and can reach well over GBP80k with options.
Also under strong consideration is a hybrid powertrain previewed in the Land-E concept. Work is proceeding apace on this technology, centred on an integrated electric rear axle drive, which makes sure that the hybrid’s electric motor drives all four-wheels. This is essential if a LR hybrid is to work as well off-road as on-road.
The Land-E showed, for example, that in the ‘rock crawl’ mode of LR’s excellent ‘terrain response’ system, drive is purely electric, offering unbeatable ‘green’ credentials in remote countryside.
Land Rover engineers are also convinced that they can solve reliability concerns off-road, for example, successfully waterproofing electric parts like the critical motor.
Julian Rendell